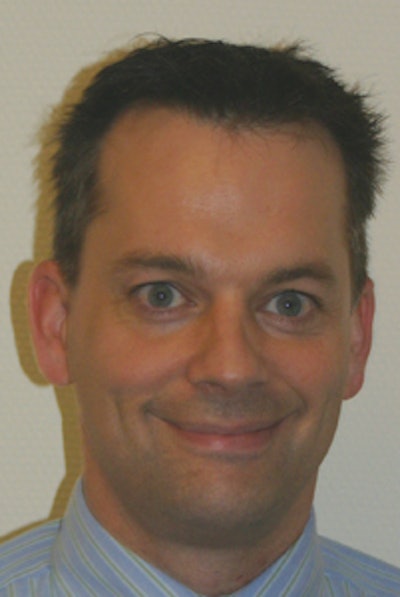
Kuehne+Nagel's distribution center in Veghel, the Netherlands, one of the largest dry food warehouses in Europe, was experiencing growing pains. The third-party logistics provider was manually handling more than 30 million cases of product a year for its two largest customers—Unilever and Masterfoods.
These customers were calling for cases of goods, rather than full pallet quantities, to be palletized and shipped to customer, DC and retail locations. Assembling mixed pallets, however, is labor intensive, time consuming and costly. It was a tough job for the 20 or so K+N workers who picked an average of 250 cases per hour.
Tim Beckmann, Veghel's site manager, wanted to automate the process, but knew he was taking a gamble. "You don't see much innovation in distribution centers," says Beckmann. "Automation is risky for small-margin warehouses—especially since we are dealing with short-term contracts. We already had high throughput in our facility and didn't want to jeopardize that.
But 50 percent of our outgoing volume for Unilever was in cases that could be delivered in whole layers, so we thought we would investigate the market and see what options were available."
K+N faced a number of challenges. About 800 to 900 of daily outgoing pallets to customers would be picked as mixed pallets in whole layers, from source pallets to customer pallets.
"We had to figure out how to automate the task of picking diverse products directly from source pallets and transferring them to customer pallets, which could be done through layer picking. But how would we handle different packaging types, shapes and stacking patterns, since these are often changing?" says Beckmann.
In addition, when retailers ordered cases, they didn't necessarily order in "layer" quantities.
"Our customers may order 30 cases of an item, not knowing that 38 would be a full layer," he says. "Yet, we knew for layer picking to be an efficient process, we would have to get them to order full layer quantities. This would require a lot of attention because suppliers often introduce new packaging materials, so the number of cases per layer or pallet is changing, as are packaging dimensions."
Automating The Layer Picking Process
After evaluating a number of layer picking systems, K+N turned to Univeyor, a material handling equipment provider headquartered in Denmark. Univeyor designed a unit, called the LayerPicker, which can de-palletize whole layers from pallets, as well as pick layers from pallet to pallet.
While layer pickers have been available for years, Beckmann says that there was not one, besides Univeyor's unit, that could handle the variety of products that go through K+N's distribution center. What's unique about the LayerPicker is its specially-designed low pressure vacuum head that can gently lift whole layers of products, including cases and cartons, cans, glass and plastic bottles, liquid containers and bagged goods.
"The LayerPicker is a fast, reliable and cost-efficient system for handling whole layers of almost any product. It can also handle shrink-wrapped articles, loose items in trays and all types of pallet patterns—even those with voids," says Kristian Dohn, global product manager for Univeyor and one of the inventors of the unit. "Plus, it enables the user to assemble multi-product pallets to customer orders without the costs, labor concerns and product damage associated with manual handling."
"The unit can handle up to 180 layers or 2,400 cases per hour. It would take more than a dozen workers to achieve this level of throughput in a manual operation," he says. "The units can be used to handle more than 95 percent of all products that are sold in supermarkets, which have the volume throughput to justify the investment."
The unit is controlled by a standard Windows platform and allows the user to make changes in product and/or pallet patterns. The system integrates into existing warehouse management systems (WMS) and can be used in a number of semi- and fully-automated applications including:
- Order assembly of mixed pallets;
- Order assembly of sandwich pallets;
- De-palletizing of whole layers to feed cross docking systems and sorting or replenishing flow racks or pick fronts;
- Layer picking and inserting slip sheets.
K+N tested the unit and found, to Beckmann's delight, that it could handle 90 percent of its products. "The unit was able to handle just about any item we fed it, so if our suppliers decided to change packaging, for example, the LayerPicker would be able to accommodate the new dimensions," says Beckmann.
Working With The WMS
The unit proved to be a perfect solution for K+N and the 3PL installed two LayerPickers in the Veghel facility four years ago. They are at the center of its automated material handling system. The WMS collects incoming orders in batches, decides which orders can be collected as full layers and passes the information to the LayerPicker about product type, dimensions, quantity and stacking sequences for each pallet.
Once the system has received an order, it automatically moves full pallets through the 410,000 square-foot facility, from a high bay warehouse, to the LayerPickers. There, layers are removed from the source pallet and crossed over to the customer's pallet, which is being built according to the order. The mixed pallet is finished, stretch-wrapped and moved to the loading area.
Today, more than 20 percent of K+N's volume at Veghel goes through the LayerPickers, and the company plans to add units at some of it other European distribution centers.
Beckmann says the system was well worth the investment. "We've reduced our staff from 20 pickers to four and increased our picking efficiency by 20 percent," he says. In fact, K+N has been able to pass the savings to its customers as well, offering a 20 percent discount to those who order in full layers.
"Our customers are key to our success. We had to work in close cooperation with them in terms of the packaging specifications. We had to make sure that the packaging wouldn't create a problem with the automation and it has worked out well for all of us," he says.
Smaller, More Frequent Deliveries
With more stores requiring smaller, more frequent deliveries, the LayerPicker is also appealing to European retailers such as Albert Heijn and Netto.
Albert Heijn (AH), a leading Dutch supermarket chain, has two LayerPickers integrated into its order-picking system at its Pijnacker distribution center, which sends some 130,000 items each day to its 189 stores throughout the Netherlands.
"We wanted to increase our order-handling capacity, reduce the need for manual labor and improve efficiency—especially for the fast movers," says Hans Eil, project manager of the Pijnacker facility. "We replenish our stores within 24 hours of receiving an order and the LayerPicker is a key component of our order-picking modules."
The order-picking modules are flow racks designed to handle 3,000 cases per hour, which are sequenced into store orders. Before the cases are entered into the system, however, they must be removed from the pallets, which is where the LayerPickers come into play. "The unit is responsible for product de-palletizing and de-scrambling and automatically replenishing flow racks, from where individual store orders are assembled into the roll carts," says Eil.
Like K+N, one of the biggest challenges of employing the LayerPicker was getting suppliers to adhere to packaging standards, says Eil, and it took a lot of trial and error to get it right, but it was well worth it. The LayerPicker now handles 97 percent of the products in the order-picking module—about 43 percent of the products that go through the distribution center as a whole.
Accuracy has increased, labor has been dramatically reduced and the best part? "The LayerPicker doesn't call in sick," says Eil.
Netto is Denmark's largest grocery chain, serving 1,000 stores under the Netto banner. Its distribution center in Koege is located about 50 miles south of Copenhagen. The 400,000-square foot facility, the largest in Denmark, was built in 2003 and features two high bay warehouses—one for dry product and one for refrigerated.
"When we analyzed our old warehouse back in 1999, we found that we were making 11,000 unnecessary pallet movements each day," says Joergen Larsen, the warehouse distribution manager. "We wanted to design a system to fully automate both the pallet handling and the picking process. We handled 9,000 cases an hour that needed to be sorted and batch picked."
The Koege facility receives and sends out 6,000 pallets and half pallets each day—some 15 million cases a year. Unlike AH, which delivers only cases to its retail customers, 70 percent of Netto's products are delivered on mixed pallets, which it creates with three LayerPickers. The units handle 85 percent of the picking from pallets. They pick whole layers of pallets, remove slipsheets and de-palletize layers to single cases.
The system includes automated pallet conveyors from the storage area to the LayerPickers and case handling conveyors to an automated sortation system.
"Our new facility handles triple the capacity of our old warehouse," says Larsen. "We could have never reached this volume without the automated system."
Is It Right For Your Operations?
Automated layer pickers have become popular in Europe over the past five years and it's a trend that is taking hold across the pond. A growing number of grocery retailers in the United States are demanding rainbow pallets containing a wide mix of SKUs. For the wholesalers, distributors and suppliers that fill those orders, it typically means that order selectors assemble pallets with individual cases pulled from storage racks by hand.
That is a labor-intensive, physically de-manding and costly exercise that is quickly becoming unnecessary, thanks to layer pickers such as Univeyor's unit.
In addition to K+N, AH and Netto, com-panies such as Kroger, Coca Cola Australia, Edeka and Mercadona are using the Layer-Picker in their facilities.
While these units require capital invest-ment, typical payback takes about one to three years, according to Univeyor's Dohn. "The majority of the savings come from a substantial reduction in manpower," he says.
Take K+N, for example. Its automated storage area requires only four workers per shift to supervise equipment operation, replenish picking areas and forward completed pallets to the dispatching area. The same area used to require at least 15 people per shift prior to the automation.
As labor is reduced, warehouse operators can also eliminate many of the occupational safety concerns associated with manual case picking because workers do not have to bend and lift cases to take them from one pallet to another. They can also reduce the amount of product damage and picking errors associated with it.
For any distribution center that is doing a lot of manual picking, a solution such as the LayerPicker may be right for your operations.