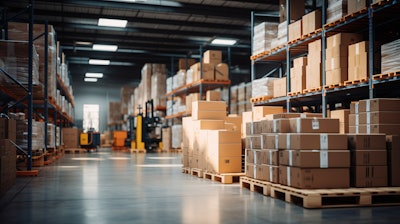
Speed can be fatal. That’s true on highways, and it’s true in a warehouse.
In the case of warehouses, speed is also a necessity. It’s a price of entry, and it’s critical for competitive advantage. This paradox — speed as both a massive safety hazard and a foundational element of success — has plagued the industry since its inception.
Skyrocketing demands for supply chain productivity during and after the pandemic have exacerbated supply chain issues. Economic concerns and widespread labor shortages compound the challenge. With fewer resources, workers are left scrambling – oftentimes with little to no training or onboarding. When this occurs, injuries are inevitable and productivity lags.
Warehouse Safety: Visible Problem; Clear Solution
In the supply chain industry, injuries and accidents pack an obvious toll on workers and their families while lost time, delayed operations and liability disrupt efficiency and profitability. There’s an urgent need to enhance safety measures for the sake of the business and especially for the sake of workers.
Does that mean slowing down?
Not necessarily.
Instead, it means pivoting to complementary solutions that enable warehouse workforces to increase output and productivity without increasing staff numbers or overburdening existing staff.
Enter Autonomous Mobile Robots (AMRs), which are not just a technological advancement but a true paradigm shift. With AMR-assisted order picking, order fulfillment and other material handling tasks, they’re reshaping operations, productivity and the very fabric of safety protocol in the warehouse for workers.
The Rise of Autonomous Mobile Robots: A Safety — and Productivity — Revolution
By automating mundane and hazardous tasks, AMRs can free up warehouse workers’ time to focus on higher-value initiatives while relieving physical burdens. With their advanced sensors and intelligent navigation systems, AMRs can detect and respond to potential hazards in real time – making them a safer and more efficient option for troubling tasks. For instance, they can react if a heavy pallet is off-balance while in motion, dodge a forklift and never herniate a disc after years of overuse.
That’s not to say these machines are more valuable than human workers. With the current state of AMR technology, they’re truly better together. Any mention of warehouse automation will likely elicit concerns over human job security. While it’s true that AMRs address specific tasks, the machines can be thought of as job enhancers rather than job replacers. AMRs can significantly enhance workers’ productivity – allowing them to complete their objectives faster, easier and with fewer injury risks.
A fundamental shift is occurring in how workers navigate warehouse aisles. By eliminating the need for repetitive trips and the associated heavy lifting, AMRs liberate workers from a common barrier to functionality — physical capacity. Accidents happen even in warehouses where stringent safety protocols are followed closely. AMRs aren’t a cure-all, but they’re a significant step forward.
Empowering Workers with Wearable Technology
The link between warehouse workers and AMR technology: wearables. Wearable devices are emerging as the linchpin of this safety revolution. These devices empower workers by enabling direct communication with AMRs. Wearables offer valuable, real-time insights that facilitate better decision-making. Human workers can direct and validate the AMR’s work, and the AMR can help reduce human errors, burnout and exposure to safety hazards.
This symbiotic relationship is a key point. While AMRs bring a new era of efficiency and safety, they are not infallible. Human oversight remains an important component. Even if or when dark warehouses become the default, people will still need to be part of the picture — to design, program, train, validate, optimize and remediate AMRs and their future evolutions.
But we’re getting ahead of ourselves. Right now, partnering warehouse workers with AMRs is smart for safety and competitive advantage. There’s a learning curve — and, of course, a financial investment — but given the labor market, tight competition and the unparalleled importance of workplace safety — the ROI is hard to ignore.
Welcome to the Warehouse Industry — There’s Space for you Here
A recent survey of supply chain workers shares that labor shortages were the most often cited problem facing respondents right now (57%), and respondents expect the problem to get worse instead of better. Amid lingering concerns over AMRs disrupting job security, a flip side warrants attention: AMRs could be the answer to labor shortages. And not because they replace people – rather they invite more people in.
Fatigue, injuries and even fatalities are realities of the supply chain industry – workers may age out earlier than in other industries or are forced to quit due to injury. AMRs can make warehouses safer and far more inclusive, paving the way for a significantly expanded talent pool of people who may otherwise have avoided the industry because of the physical, potentially risky nature of available roles.
An AMR, quite literally, can do the heavy lifting and not lose steam going up and down the aisles. Additionally, AMRs can be built to withstand harsh conditions such as extreme heat or freezing temperatures that would prove exceptionally challenging or dangerous for human workers.
As previously mentioned, AMRs can allow warehouse workers to focus on tasks that demand human ingenuity. That, too, creates the opportunity to expand the potential talent pool dramatically. As warehouses adopt advanced technology, there will be more jobs where strategic thinking and technological literacy are essential qualifications.
The Path Forward: Safer, More Efficient Warehouses
The integration of AMRs into warehouse operations signifies a compelling shift. Safety is no longer a standalone concern but integral to a broader strategy for enhanced efficiency and productivity.
The warehouse landscape will continue to evolve, and AMRs in their current iteration are just the beginning. Change is inevitable, but we can’t return to lower safety standards or lower standards for the employee experience. These must remain at the core of operational focus. The new standard for warehouses is a place where cutting-edge technology, human ingenuity and safety converge. AMRs are a crucial part of achieving that standard. What’s stopping you?