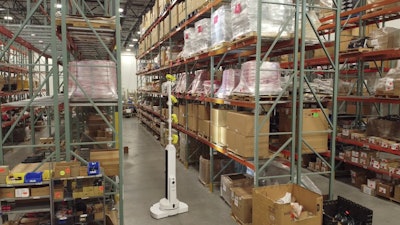
Warehouses are seemingly always in catchup mode. Orders keep piling up, customer expectations keep climbing, and every day feels like a race against time—with the same number, or in some cases, fewer people to run it. Turnover is nearly one in three, skilled labor is harder to come by, and the old ways of managing operations—like manual cycle counting and paper-based processes—just aren’t cutting it anymore. Teams are burning out. Mistakes are costing more. And the gap between what's expected and what’s realistically possible keeps widening. The pressure isn’t just uncomfortable—it’s unsustainable. To break out of this cycle, warehouses need more than extra hands. They need smarter, scalable tools that can shoulder the load. That’s where autonomous mobile robots (AMRs) come in.
A new era in warehouse operations
Powered by advanced sensors and intelligent machine learning, today’s AMRs can perform a wide range of tasks. While capabilities vary across different models, AMRs are designed to navigate autonomously through dynamic spaces and work on their own so their human teammates can focus on other tasks, making them a versatile tool for improving workflows.
In the short term, AMRs provide a rapid solution for businesses to meet rising demand—especially during times when speed and scalability are non-negotiable. Imagine a warehouse preparing for the holiday rush or an unexpected surge in online orders following a product launch. Instead of scrambling to hire and train temporary staff, AMRs can be deployed instantly to support core operations.
With typically minimal onboarding time required, these robots can begin working right away—picking, sorting, or doing inventory checks around the clock. Because AMRs can adapt to changing workflows and move freely within dynamic environments, warehouses can respond to shifting order volumes without overhauling infrastructure or disrupting operations. This flexibility is critical during peak seasons, when the ability to scale quickly can make or break fulfillment timelines.
The long-term solution
Beyond their immediate impact, AMRs deliver substantial long-term value. While their short-term advantages are widely recognized, their broader influence on warehouse operations and employee experience continues to grow. Businesses that have integrated AMRs report significant improvements in employee satisfaction and retention, contributing to a sustainable warehouse environment. In fact, 88% of employees say they experience higher job satisfaction when working alongside AMRs.
AMRs play a pivotal role in reducing the physical demands placed on employees by automating repetitive tasks. This allows workers to focus on more meaningful and strategic roles, such as problem-solving and overseeing robotic operations. With less physical strain and fewer repetitive motions, AMRs also help lower the risk of workplace injuries, contributing to a safer environment overall. As a result, employees are more likely to feel valued and supported, which drives higher job satisfaction and long-term retention.
In addition to supporting a healthier and more motivated workforce, AMRs can help reduce labor-related expenses over time. Automation in warehousing has been shown to cut labor costs by 60%, with projections indicating up to 40% reduction across broader warehouse and supply chain operations over the next five years. These long-term savings, combined with improved employee morale and enhanced safety, make AMRs a strategic investment that benefits both operational efficiency and workplace culture.
AMRs vs. legacy systems
While traditional warehouse processes like manual cycle-counting have long been used in operations, they now present significant limitations in keeping up with the pace and complexity of modern fulfillment demands. Manual checks are not only time-consuming, but also prone to human error, which can lead to inventory inaccuracies, stock delays, and workflow disruptions.
AMRs, in contrast, are highly adaptable and capable of navigating through complex warehouse environments with ease. They integrate into various layouts and conditions, adjusting to the existing infrastructure. Designed to operate autonomously, AMRs remove the need for manual supervision, minimize errors, and ensure consistent execution. This flexibility allows for warehouses to scale quickly and respond to demand surges or seasonal fluctuations without compromising efficiency.
Enhancing efficiency with AI
As the demand for faster order fulfillment continues to rise, AMRs are evolving just as quickly. A new level of intelligence allows AMRs to not only react to changes in real time but also anticipate them, optimizing routes, prioritizing tasks, and collaborating with other systems to streamline operations across the warehouse. Rather than functioning as isolated tools, AMRs are becoming fully integrated components of a smart warehouse ecosystem. According to PwC research, artificial intelligence has the potential to supercharge productivity by 40% by 2035; illustrating how the integration of AI-driven systems like AMRs can significantly boost warehouse capabilities.
The future of warehouse automation
The mobile robotics market is projected to grow by 30% by 2030, solidifying the value of automation as a central force in its potential to drive speed, accuracy, and efficiency across warehouse operations. AMRs provide a strategic advantage in an increasingly competitive logistics landscape, enabling businesses to meet the challenges of rising demand, labor shortages, and evolving customer expectations. More than a trend, AMRs are an indispensable tool for warehouse logistics.