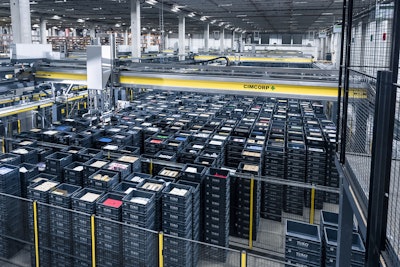
Automation is a must-have for today’s fast-paced warehousing and distribution operations. To scale effectively, companies are turning to flexible automation solutions that boost efficiency, increase throughput, and adapt to shifting demand. While automation technologies like automated storage and retrieval systems (AS/RS), automated guided vehicles (AGVs), and conveyors can significantly improve warehouse operations, true efficiency depends on how well they’re coordinated. That’s where a warehouse control system (WCS) plays a vital role.
Unlocking the value of warehouse automation
In an automated warehouse, a WCS acts as the “brain” behind the operation. While a warehouse management system (WMS) focuses on inventory tracking and strategic planning, the WCS brings those plans to life. It receives all relevant data on products, order lines, volumes, priorities, and dispatch deadlines from the WMS, and then translates that data into real-time commands for equipment on the warehouse floor.
Think of a WCS as the conductor of an orchestra, where each piece of automated equipment is an instrument. Without the WCS coordinating them, the result would be disjointed and ineffective. Instead, the WCS ensures all elements work together in harmony, directly managing everything from individual robot movements to overall material flow. By breaking down silos and coordinating all automated systems, the WCS prevents bottlenecks, speeds up fulfillment, and keeps operations flowing even during disruptions.
The WCS transforms a collection of machines into a synchronized, intelligent solution, giving companies greater operational visibility and responsiveness.
5 things to consider when choosing a WCS
Selecting the right WCS is essential for optimizing warehouse performance. A well-chosen WCS will improve efficiency, reduce disruptions, and support long-term growth. When evaluating WCS solutions, it’s important to consider the following key factors:
- Easy integration with existing systems
A WCS must work in harmony with the entire warehouse ecosystem, enabling seamless communication between robots, equipment, and higher-level management platforms. Companies can avoid integration challenges by selecting a flexible WCS designed to connect with virtually any WMS through APIs, file-based data exchange, or direct database access. This approach saves time, reduces costs, and prevents operational disruptions.
2. Scalability and adaptability
Since warehouse operations evolve over time, a WCS must be flexible and scalable to deliver value well into the future. The right software should be able to adapt to demand shifts and increasing order volumes, while maintaining performance and stability. Additionally, the WCS should support the addition of new equipment, workflows, and technologies. Ultimately,
3. Real-time data visibility
In the modern warehouse, real-time data is critical for making faster, smarter decisions. A great WCS offers advanced monitoring and analytics dashboards that empower warehouse staff with insights into equipment performance, KPIs, potential bottlenecks, and opportunities to improve processes. With this level of insight, warehouses can quickly respond to disruptions, reduce downtime, and ensure operations flow smoothly at all times.
4. Ease of use
Companies should select a WCS with ease-of-use in mind. A user-friendly WCS reduces training time and enables teams to quickly manage, troubleshoot, and optimize operations.
5. Vendor expertise
Experience matters. A WCS provider with deep automation expertise plus industry-specific experience can tailor solutions to meet unique operational and regulatory needs. This combination of specialized knowledge can significantly maximize the performance and value of automation investments.
The future of WCS: AI and machine learning
WCS technology is constantly evolving. Today, artificial intelligence (AI) and machine learning (ML) are bringing new levels of intelligence and adaptability to automated warehousing solutions. With AI and ML integration, WCS solutions are shifting from reactive to proactive control. They can use predictive analytics to spot issues before they cause problems and adjust workflows in real time to keep everything running smoothly. Combined with cloud-based architecture, these technologies are making it possible for companies to scale and optimize warehouse operations while monitoring performance from anywhere.
As automation providers incorporate AI-powered capabilities into their WCS offerings, warehouses will gain new ways to cut downtime, boost efficiency, and keep operations strong. Equipped with a WCS that integrates effortlessly with existing and emerging technologies, provides real-time insights, and scales with business needs, companies can maintain a competitive edge long into the future.