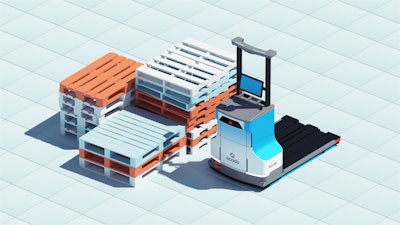
In the past, advanced autonomous mobile robots (AMRs) were only used to navigate static environments and only capable of supporting one task or workflow. Today, AMRs are true cobots, collaborating with other robotic, automated solutions and people.
When AMRs are paired with automated packaging solutions, such as custom-cut box technologies, pack stations, and depalletizer arms, warehouses can reduce order fulfillment costs and increase overall warehouse efficiency. E-commerce and retail warehouses can lower overall costs and increase order fulfillment capacity to remain competitive.
Pairing AMRs with custom-cut box technology increases fulfillment capacity by 20%
E-commerce warehouses fulfill orders that combine a variety of goods such as beauty products, apparel, footwear, or electronics, with each order requiring a different sized box. Right-sized packaging solutions help operations save money at many points in the supply chain, improve quality and customer service, and reduce environmental impact.
There are more than 15 companies that support right-sized packaging applications. Some offer vision and software technology to inform the box size each order needs. Others provide equipment that cuts custom boxes. Whichever the approach, the box is right-sized for each order cut in real time, providing many benefits:
●Custom boxes lower material expenses, write-offs, and transportation fees. Warehouses use them to reduce costs and the environmental impact of excess packaging materials.
●Right-size packaging reduces damage during transit, lowering external failure costs and the risk of disappointed customers. Each product is tightly packed, allowing no room for items to move inside the box and break.
●Because the boxes are customized to remove air space, more boxes fit onto delivery vehicles, increasing truck capacity and lowering shipping costs calculated on volumetric weight.
Right-sized packaging also creates opportunities for warehouses to combine efficient packaging with flexible AMRs. Pairing both technologies increases pick rates and establishes smooth flows between packaging and picking.
Integrating these two approaches starts with cubing, during which the warehouse management system (WMS), the order fulfillment platform (OFP) built into the AMR, or the custom-cut box software calculates the space an item (or group of items) needs inside a box. Regardless of which software calculates the cubing, the box size measurements are sent to the AMR, which saves them until it has acquired the box sizes for all the orders. When the AMR is ready to start picking, it sends a message to the custom-cut box software to start cutting. Within seconds, the boxes are being prepared as the AMR travels to the packing station to collect them. Because the boxes are custom cut, more fit onto the mobile robot. The AMR groups orders to maximize capacity based on picking strategies and box sizes. This results in more order completions on a picking route. Customers can add 20% more orders to picking AMRs when boxes are custom cut, reducing the cost per unit pick and labor by 50%.
Auto baggers and AMRs collaborate to reduce packing time by 50%
Auto baggers can also partner with AMRs to increase warehouse throughput. Auto baggers pack orders with little or no human labor. They come in many different configurations, including semi-automatic or fully automated, and orientations, such as tabletop, vertical or horizontal. Some have attached peripherals like scanners and labelers. Auto baggers reduce the manual labor required to place and pack items in boxes, a repetitive and arduous task previously done by warehouse associates. When warehouses connect AMRs with auto baggers, the technology takes over the handoff between the picking and bagging operations, generating higher throughput and reducing packing errors.
This integration starts with the self-directed AMRs. As they travel the warehouse floor performing single-line-single-unit batch picking, the fulfillment execution system (FES) that orchestrates the AMR fleet captures relevant information: the number of items picked (batches) and totes where the batches are placed. Once the batch picking is complete, the AMRs tell the auto bagger the totes are on their way, the items in each tote and the orders to prepare, all ahead of time. As the AMRs arrive at the packaging station with all the items, the scanners on the auto bagger read the labels to correctly identify each tote. Then, the auto bagger automatically sorts batches into individual orders and packs the products. The touch-free, real-time synchronization between AMRs, for picking, and auto baggers, for packing and dispatch, lowers shipping costs and can reduce packing time by more than half.
Synchronizing depalletizing arms with AMRs improves case handling
Pallet loading and unloading is one of the most labor-intensive and costly processes in fulfillment. Warehouses and distribution centers are turning to robotic arms to automate these injury-prone, repetitive tasks and reduce labor costs associated with case handling. Dimension Market Research forecasts that the global robot palletizer market will be valued at $2.8 billion by 2033.
Modern robotic arms incorporate cameras and sensors to identify, pick, and carefully handle different types of boxes, materials, and weights. High and mid-throughput e-commerce and retail warehouses use them to move inventory off pallets and quickly replenish warehouse stock. These arms can also build multi-SKU pallets in minutes, using optimal layer patterns to prevent product damage. When palletizer and depalletizer robotic arms collaborate with these AMRs, warehouses reduce the workforce needed to handle cases, as well as their dependency on certified forklift drivers and manual labor to transport pallets to and from the robotic arm zone.
Within the large spectrum of AMRs, some automate heavy pallet movement, directed by a fulfillment execution or WMS, to pick, transport, and place pallets. In a depalletizing workflow, the warehouse execution system instructs the case-handling AMR to bring a pallet to the robotic arm to unload cases for warehouse replenishment. The WMS sends to the AMR the pallet’s location on the warehouse floor and its destination. The AMR autonomously travels to find the pallet. Once the robot picks up the pallet, it sends a message to the robotic arm and drops the pallet in the designated area for deconstruction. The depalletizer unloads the cases onto a conveyor, a tote, or another pallet. Once the mission is completed, the WMS commands the AMR to remove the empty pallet. By then, the next AMR, with a fully loaded pallet, will be ready to drop off its cargo.
This thorough orchestration of robotic arms and AMRs enhances fulfillment productivity and warehouse efficiency. Also, warehouse associates are removed from arduous environments, increasing workplace safety. Auto packing helps warehouses maintain profitability and streamline fulfillment. When these solutions work hand-in-hand with AMRs, the hand-off between picking and packing is seamless, translating into time, cost, and labor savings.
With robotic collaboration, one plus one equals three.