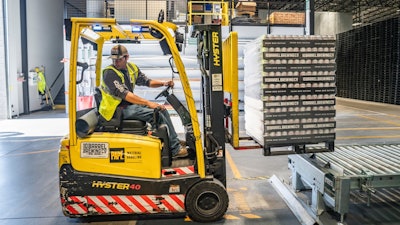
Every link of the U.S. supply chain is under significant strain from rebounding consumer demand and record imports into the country. These shocks are being felt all over. Disrupted operations from supply chain shortages have led to a spike in prices for customers. The demand for commercial space has never been higher, with nationwide industrial vacancy rates at an all-time low of 3.6% in the third quarter. It is estimated that the United States will need to add 330 million square feet of warehouse space by 2025 to keep pace with the expected uptick of e-commerce.
Now more than ever, it is essential that warehouse operations run as smoothly and efficiently as possible to keep up with rising demands and lowered vacancy rates. Industrial vehicles are the lynchpins of warehouse operations, and the right energy source powering them can have a serious impact on performance. Choosing the right battery affects efficiency, maintenance, costs and crucially the length of time that vehicles can operate at full functionality on any given workday.
Lithium-ion batteries are 30% more efficient than less advanced counterparts, which translates into better use of energy and greater output for lithium-powered vehicles. These batteries have a wide window of operation allowing almost 100% of the energy stored to be used with the power output remaining unaffected. In contrast, the power output of other types of batteries can suffer as the cells are run down, directly affecting the operability of the connected vehicles.
For lithium-ion, high performance can also be maintained in colder environments. Batteries from trusted manufacturers are able to maintain higher capacity in low temperatures, such as inside industrial freezers, and can even be fast charged in such environments. Modern developments like state of charge displays and low battery warning signals mean they are easily monitored and maintained, preventing vehicles from running out of charge during a busy shift. This efficiency, dependability and high density reduces idle time for industrial vehicles powered by lithium batteries, so they spend less time charging and more time in action.
Click here to hear more about different forms of energies in the supply chain:
Of course, even the best batteries need charging, and here lithium-ion also prevails, as lithium batteries charge considerably faster; cutting-edge batteries can reach full charge in under 90 minutes, much faster when compared to the usual overnight charges of other technologies, and don’t require constant watering, cleaning or equalizing to function. The ability to charge vehicles during a breaktime allows for three shift operations without the need for a battery change in the middle of the day. This, in turn, means that no spares are required, which greatly reduces costs, warehouse space and valuable time spent replacing batteries.
Depending on user profile, advanced lithium-ion batteries offer around 4,500 charging cycles. Their superior longevity means less time spent on maintenance and replacements and more time powering warehouse operations. Even during the functional lifetime of lithium batteries, several modern features assist with keeping them operational for the longest possible time, such as battery management systems (BMS):
BMS provide temperature control and monitoring against overcharging, deep discharging and short circuiting. Active balancing modes support equal flow and receipt of energy between lithium-ion cells. This means cells maintain a consistent voltage level with each other, so no cell degrades quicker than the rest and the life of the whole battery is prolonged. Features like these optimize the performance and lifecycle of lithium-ion batteries, so repair and maintenance requirements are considerably reduced.
Credible lithium-ion manufacturers stay at the vanguard of innovative battery technology and offer state-of-the-art features like cloud access and multi-directional communication as a standard. This allows remote access to batteries via Wi-Fi and 5G in order to perform essential tasks like shutting down a damaged module or increasing charge to reduce unnecessary time wastage. Through warehouse management systems (WMS), maintenance diagnostics alerts can also be sent via email to engineers and warehouse managers, so key personnel can stay on top of battery and vehicle performance and substantially reduce vehicle downtime.
Lead acid has a valid place in the industrial supply chain. On average, up to 95% of lead acid batteries are recyclable, so the circular economy potential of lead acid is high. Lead acid also allows for lower upfront costs and the capacity of one battery charge is usually sufficient for a normal workday. However, multi-shift operations in times of high demand are a different ballgame. The greater efficiency, output and uptime of modern lithium-ion powered vehicles along with reduced space requirements put the technology in another league.
Whether powered by lead acid or lithium-ion batteries, warehouse managers have plenty of options when it comes to choosing the right option from the right manufacturer to fulfill their long-term operational needs, given contemporary demands and challenges.