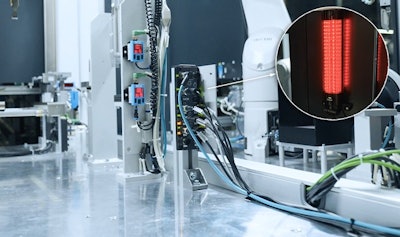
The new SIG300 IO-Link Master from SICK is designed for efficient automation tasks.
Special highlights include the integrated logic editor, which solves remote control tasks directly on the device, and the USB-C interface for intuitive configuration of the SIG300.
Key takeaways:
· Companies can integrate sensor and actuator data into IT and cloud platforms in real time via several interfaces, including JSON-REST API and MQTT. This is particularly relevant for applications such as condition monitoring, process control, and remote maintenance.
· Users of the SIG300 configure and parameterize connected IO-Link devices without additional software directly in the web interface of the SIG300 – thanks to the integrated IODD interpreter.
· Customers can also access SICK's Function Block Factory online and generate suitable manufacturer-independent function blocks. This makes it just as easy to integrate the SIG300 into fieldbuses and controllers from different manufacturers, and to seamlessly integrate it into the existing automation environment.
· Furthermore, the “Backup & Restore” function makes it easier to replace connected devices. As soon as a sensor or actuator is replaced, the SIG300 automatically transfers the previously saved device configuration to the new device, without any additional time or effort on the part of the user.
· SIG300’s integrated logic editor enables decentralized filtering and analysis of IO-Link device data. Thanks to this pre-processing, logic operations such as counting, averaging or limit value monitoring can be performed in the SIG300, and data can be bundled for data transfer.
· The SIG300 IO-Link Master seamlessly records, manages and integrates process and device data. This opens numerous application possibilities in the most diverse fields of process control.
· The SIG300 also offers decisive advantages in the condition monitoring of machines in demanding industries. It records critical changes in real time and displays them via multiple channels: A connected signal lamp immediately alerts employees at the operational level to a critical message, while the SIG300 concurrently forwards the data to monitoring applications at the IT level.
· In addition, the SIG300 continuously records the status of the sensors so that maintenance measures can be carried out as required.