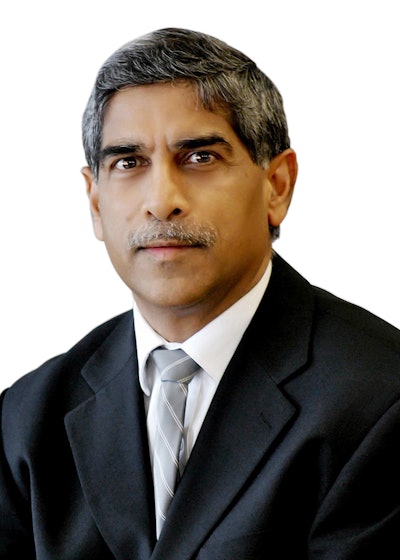
How do you top an experience like setting foot on the moon, especially when you’re one of the first to do it?
According to astronaut Buzz Aldrin, you don’t—which is why he famously struggled with a condition he called “the melancholy of all things done” after his return to earth in 1969.
In many ways, it’s the antithesis of the situation that logistics professionals face, because no matter how many successful missions, projects or assignments we complete, we are never fully done finding meaningful ways to do our jobs.
As evidence, consider the subject of supply chain packaging. Almost every company employs this external layer in some form or fashion, because it plays a key role in securing, preserving and protecting items during transit. However few are engaging in it as proficiently or sustainably as they could, which means they’re probably paying far more than they should for everything from their freight and warehousing to their waste management—and that we still have a prime opportunity to help them make significant changes for the better in this frequently neglected space.
Stage 1: Observe Your Supply Chain Packaging in Context
Fortunately, it doesn’t require the skills of a rocket scientist to recognize a supply chain packaging configuration that’s a fitting candidate for improvement. In fact, many of the most common packaging drawbacks or symptoms are easily detected by the naked eye. These include:
- A marked contrast between the size of a product and its exterior packaging.
- The appearance of significant extra air space when a box or crate is opened.
- Larger than average amounts of interior stuffing in a box or crate.
- Items stored in single/double rows or layers at a distribution center (DC).
- Significant amounts of empty space at the top of incoming trailers or containers.
- Boxes, pallets or crates that can’t easily be picked up by a forklift or other standard piece of industrial equipment.
- Excessive amounts of cardboard boxes, plastic containers or filler materials that need to be hauled away from DCs or loading docks.
- Frequently damaged or deformed boxes and/or products.
While the presence of one or more of these conditions in your company’s operations may not guarantee that the packaging in question absolutely needs an overhaul, it does at least suggest the need for further examination.
Stage 2: Examine Your Suppliers’ Contracts with Packaging Efficiency in Mind
If you prefer to explore your packaging efficiency from another, more administrative angle, take a closer look at your company’s supplier contracts to see if they contain any of the following potential packaging pitfalls:
- Supplier responsibility for preparing products for long-distance shipping.
- Supplier penalties/liabilities that are levied only (or predominantly) in cases of product damage.
- Limited provisions for reviewing package efficiency and performance.
Although such contractual terms are typical, they essentially give your suppliers carte blanche to choose packaging materials and configurations based on their priorities rather than yours. Just as important, they lay the groundwork for frequent over-packaging because they focus solely on product protection with few, if any, consequences for what these excessive materials may cost your company in terms of extra supplies, freight, storage, waste disposal or carbon offsets. And neither scenario bodes well for streamlined packaging performance.
Stage 3: Shoot for the Moon by Pursuing Some of the Following Packaging Improvements
By now it should be apparent that there are plenty of ways to spot supply chain packaging inefficiency or the conditions that contribute to it. But thankfully, there are numerous ways to significantly improve your packaging performance, too.
These include:
- Introducing reusable packaging options to reduce your dunnage and cost for packaging materials.
- Considering a change from cardboard to metallic or plastic materials to improve boxes’ stackability and durability.
- Switching to collapsible packaging for any returnable boxes or crates you’re already using to reduce the transit space they require during their return journeys.
- Revisiting how items are being packaged to see if it’s possible to get more products into each box or crate, and use less filler.
- Revisiting how boxes or crates are being loaded onto containers and trucks to see if a dimensional change can improve their cubability.
- Building and testing package prototypes to see which ideas really hold up well in the real world and which are best left on the cutting-room floor.
- Revisiting your supplier contracts with an eye toward adding terms that encourage greater amounts of packaging optimization.
So if you’re looking for new and different ways to make dramatic supply chain improvements, and feel like you’ve already been there and done that in most parts of your logistics operations, maybe it’s time to stop thinking outside of the box for just a bit and start thinking about the box instead. Chances are good you discover a lot of untapped opportunities—and plenty of ways to keep aiming high.