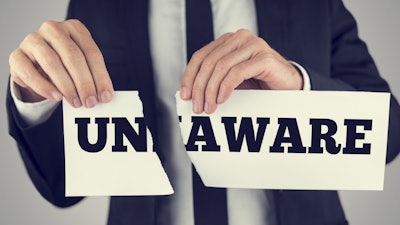
Slug: industry focus overcoming disruption
What is impacting the bottom line of every major retailer and manufacturer in the world? Supply chain disruptions, which are inherently resulting in the operational “blind side” across industries. Among publicly traded companies, this challenge negatively affects shareholder value in excess of 7 percent annually, and requires months to rebound to original levels (Building Resilience in Supply Chains—World Economic Forum, January 2013). The threat of disruption in the theater of global operations is growing more volatile and less forgiving year over year.
For supply chain leaders, the need to analyze and respond to these detrimental occurrences has been replaced with a predict-plan-monitor-and-execute discipline in advance of critical events. It’s an attempt to eliminate blind side disruptions by getting “left” of them on the event timeline to mitigate or eliminate risk or expose opportunities requires a non-traditional approach.
Running Blind: The Missing Supply Chain Answers
Today’s systems of record and execution in the supply chain arena have been oriented to the enterprise and optimized for basic processes. I often use a sports analogy when referring to these systems of record/execution as operational blocking and tackling. To win in the future, supply chain executives will need to ask themselves, “Will the fundamentals of blocking and tackling ensure my growth aspirations, or will I need to do more?”
According to Gartner, “Revolutionary changes are happening…as industries move from a product focus to services and solutions. The winners will manage an entire value chain ecosystem that provides complete solutions to customers.” (Innovation Insight: Original Solution Orchestrators Extend Innovation in the Demand-Driven Supply Chain—Gartner, November, 2012).
In short, Gartner asserts that over time, companies will fall into three categories: survivors who will innovate and manage their own processes, winners who will innovate and servitize their best in-class capabilities, and losers who will continue to block and tackle.
To do a quick assessment of where your organization is on this scale today, ask these four simple questions of your team. Measure how long it takes to answer, and the accuracy of the information provided:
- Where is this particular shipment?
- When will it actually arrive?
- How certain are you?
- Could it have been delivered more quickly without an increase in cost?
If questions 1-3 cannot be executed in less than 10 seconds and No. 4 in less than 60 seconds, there is work to be done. Winning companies are attempting to understand how to remove the inefficiencies and harvest the real-time value locked in their supply chain. Many are seeking help from technology organizations to support these efforts.
According to The Smarter Supply Chain of the Future study published by IBM, 70 percent of supply chain leaders and managers report that lack of visibility is their biggest challenge. From not really knowing where cargo actually is in-transit to accurately predicting production and port turnaround cycles, the blind spots in supply chains are bigger than most would ever understand.
The Inconvenient Truth: Traditional Technology Approaches Fall Short
Traditional technologies in the supply chain space often rely on the data and information of their extended networks to deliver the “end-to-end” picture and the transactional insights along the way at a drudgingly slow, industry-driven velocity. The unfortunate truth is, most organizations have found themselves at the mercy of a tangled, latent and inaccurate data network, where service providers self-report information and industry service-level agreements have allowed them to do so 24-36 hours after each event in the process occurs.
A recent study produced by TransVoyant for a Fortune 500 hi-tech OEM revealed that a best in class EDI-based network slowed the end-to-end order lifecycle for finished goods shipped globally via airfreight an average of 5 days. This was due to insufficient data velocity and quality, which delayed downstream process triggers.
In this model, even if you are best in class, you will obtain 70 percent of the information needed to drive efficient decisions at a velocity that is at minimum 50 percent slower than advanced alternative approaches–falling far short of what is needed to unlock the value held hostage in the supply chain.
The Silver Lining: There Is A Better Way
A small but growing list of supply chain executives have begun to challenge the status quo of traditional supply chain technologies and press organizations large and small to develop and innovate the solutions of tomorrow. The members of this elite list are often referred to as visionaries. These visionary players are not focused on better blocking and tackling but determined to force the industry to look past optimized processes and deliver competitive advantages.
I have had the opportunity to sit in on visionary discussions within multiple verticals–from hi-tech to pharmaceuticals to retailers–and found that leaders from each have a common interest…time. Every hour, day or week of delay is extremely expensive. Even more costly to these organizations is the “fluff” that is built into cycle times due to low quality, self-reported and latent information that drastically inhibits efficiency.
Delivering time, which reduces decision windows and fluff, is more readily available than many realize. The challenge, however, is that it takes a very non-traditional approach to do so.
The Live Information Model: Retiring EDI and Removing Latency
We could talk all day about 850s, 856s, 214s, 315s or rated 810s, but we would certainly not teach an astute logistics or supply chain executive anything. I also understand that not all EDI signals that power most global organizations can be retired, but I will argue those that attempt to provide answers to questions stated in the “Running Blind” section of this article can be.
What many shippers (e.g., beneficial cargo owners or BCOs) do not realize is that it does not take EDI signals to communicate these precious events and it certainly does not require BCOs to wait 24-36 hours to receive them. I liken this to reading yesterday’s news–not very helpful.
BCOs should know that it does not require EDI signals to:
- share shipping notifications,
- monitor origin terrestrial milestones,
- confirm booking processes,
- track departure notifications,
- track in-transit performance to plan,
- provide notifications to customs brokers,
- track arrival notifications,
- track progress with customs entities,
- provide turnovers to truckers/on-forwarders,
- track terrestrial hub or final mile deliveries, or
- provide forward visibility.
To do this requires technology that is geospatially oriented and optimized for speed. Additionally, the technology must be capable of colliding static enterprise data, live risk data, and predictive analytics, and correlating these elements in real time to deliver complete transparency and actionable intelligence.
The good news is, if you don’t want to waste tens of millions of dollars attempting to build this on your own, analytics as a service and web-based applications have been built to do this very thing–giving you insights into your blind side and delivering time back to forward-thinking companies.
Tyson Leal is the Director of Industry Markets of TransVoyant, bringing more than 15 years of supply chain management leadership and expertise to the company. Using his predictive logistics experience, Tyson has helped shape and deliver TransVoyant’s “Live Supply Chain” solution to the hands of supply chain decision makers around the world.