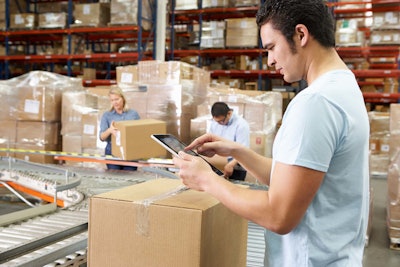
Slotting is the process of determining the best storage location for each stock-keeping unit (SKU) in a distribution center (DC) or warehouse, or in layperson’s terms, pinning down the items that are used most often,, not the total quantity that is picked, and making them as accessible as possible. In theory, the SKUs that must be physically touched most frequently get the best seats in the house. In order to optimize the order picking in warehouse or DC operations, slotting is considered low-hanging fruit. Since the more time an employee spends locating or picking a product, the more money that drains from the bottom line, it’s a boon when it comes to cutting costs.
“More than half the labor in a DC is focused on order selection, so employing smart racking and slotting techniques is a way to target a high-cost activity as a means for reducing costs by increasing efficiencies,” according to Dan Basmajian, CEO of Optricity. “Technologies that optimize rack layouts (that is, profiling), and then sequence and group product can create a beneficial impact by cutting the cost of the selection operation.
“Furthermore, nobody wants to waste space inside a slot, so it’s important to try to fill the slot to capacity every time, according to the rules and targeted number of days of product. By employing good slotting techniques, an operation can reduce travel distance by sequencing items based on velocities and reduce the time to build stable outbound pallets by sequencing based on case density (which also cuts down on product damage in transit). These are just a couple of examples; if an operation pays the most attention to the biggest expense (usually selection), then the result is the biggest opportunity to cut the most dollars.”
Profiling
Profiling is the other side to the slotting coin and another facet to use when optimizing warehouse and DC picking operations. Basmanjian notes, “Profiling considers the expected SKU mix, dimensional information (including TI HI values), outbound movement and volumes, and the target amount of product to keep in the pick location.” TI HI means the number of boxes stored on a layer or tier (TI) and the number of layers high that these are going to be stacked on the pallet (HI).
While profiling may appear relatively simple, putting all of the criteria together and assessing it can be daunting. Fortunately, software exists to process the data and ranges in simplicity from Excel spreadsheets to advanced applications. Basmanjian warns, however, that warehouses and DCs must evaluate the software to ensure that it can achieve the necessary complexity that is sought. “As an example, consider the ergonomics of heavy items and where they are placed—ideally at chest height—or breakable items for which a tool must be able to handle exceptions like putting glass at chest height for safety and prevention of product breakage. The optimal solution is subject to a certain set of goals and constraints related to product characteristics (like weight and fragility). It’s challenging for spreadsheets to handle this problem because they only consider two dimensions. Specialized software can handle any number of goals and constraints, which allows a useful and usable solution. Slotting is the implementation process that goes with the specialized software.”
Slotting and Sequencing
“Once the profiling piece is complete, it’s time to consider all the goals and constraints associated with the pick line, such as groupings—for example, groupings based on flammable items that require sprinklers, groupings based on store-friendly deliveries, groupings that are required to have separate temperature control or explosive safe rooms, etc.—and sequencing, for efficiency and ergonomic picking,” Basmajian continues. “Specialized profiling and slotting software handles all the side conditions or constraints that the real world imposes on this problem; a simple solution doesn’t fit the real-world requirements.”
“Pick line balancing, family grouping and like item separation are some of the components necessary to arrive at the most sensible organization,” concurs Peter Schnorbach, senior director of product management at Manhattan Associates. “Slotting technology considers these factors and delivers the most efficient arrangement,” thereby decreasing strain on travel and replenishment.
Different companies have distinct slotting strategies based on their line balancing needs, and product alignments and segregations. The reason that slotting is so successful is that it manages all possible scenarios of how a DC could be structured. According to Schnorbach, one scenario is, “with the ability to look at the historical movement of inventory, slotting can assess the optimal location to put the products in the warehouse. This location is determined through slotting’s intricate algorithms, which place inventory based on reducing travel time and replenishment cost. Putting it simply, slotting doesn’t just allow you to place products anywhere you want. It takes a look at the greater picture and decides the best location.”
Trending
Where is slotting processes and software going? “In the last few years, there has been a very dramatic shift in the way companies do business,” laments Schnorbach. “Warehouses and DCs need to be organized in terms of how people buy. New products are being introduced constantly, with new inventory being brought in throughout the month, meaning DCs are slotted four or five times a month. In addition, a company may have multiple warehouse locations, in which case they need a robust solution in all locations to best determine single-item slotting and real-time slotting. If a retailer has hundreds of thousands of items and SKUs, it takes a huge amount of processing power to optimize that.”
Basmajian thinks that dynamic slotting, a process by which the system can set up new or temporary slots for SKUs, and simulation are both going to affect the DC and warehouse market in a big way. “Dynamic slotting allows an operation more control for understanding the requirements for a particular day; that is, dynamic slotting allows one to forecast how many temporary locations make sense for a period of time in order to reduce stock-outs. Furthermore, simulation is critical to making changes to slotting or racking. Re-racking is very expensive, and simulation allows one to test the impact and understand the return on investment before investing the labor or capital expense. Simulation cuts the risk and provides solution alternatives for evaluation.”
What Optimized Slotting Can Achieve in a Warehouse or DC
- Minimized travel, picking and replenishment costs.
- Increased productivity.
- Less operating and capital expenditure costs.
- Improved pick line efficiency.
- Reduced inventory damage.
- Better overall order quality.
- Optimized storage and retrieval.
- Increased SKU capacity.
- Improved warehouse throughput capacity (lines per hour).
- Less employee picking injuries.
- Better employee safety, inventory storage and store-friendly pallets.