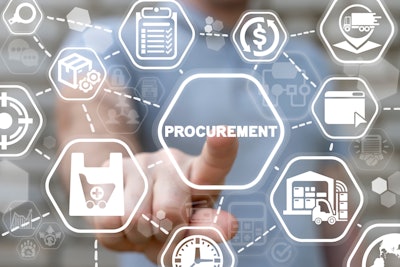
Technology product designers often have little or no insight into the supply chain factors or end-of-life issues related to key components they embed within their products. This “design disconnect” from product lifecycle realities has a significant impact—not only on the balance sheet and reputation of their company, but also on the health and welfare of end-users; particularly in industries such as medical device manufacturing.
Traditionally, designers create specifications for new products before procurement sends out materials requests to suppliers for competitive bids and little or no communication occurs between these two groups. However, this communication gap between design and supply chain sourcing can cause serious problems for complex products, particularly when supply chains are stretched thin and essential components are difficult to obtain in a timely manner.
To overcome this design disconnect, company leadership must redefine the role of technology product designer to include responsibility for supply chain risk management. In other words, it’s time for companies to adopt a design-led risk management approach.
Merging product design and sourcing capabilities
To eliminate this current disconnect, technology product designers need to adopt a supply chain risk management methodology that requires greater cross-team collaboration with supply chain sourcing managers at the earliest development phase. Inviting sourcing staff to participate in the design process helps identify and address questions related to required materials, available suppliers, supplier strategy, anticipated procurement challenges, end-of-life issues and estimated costs—long before anything goes into production.
Because the type, number and origin of components for a given product can have a significant impact on supply chain costs, this level of collaboration between design and sourcing teams can often result in improved cost efficiencies. In fact, a Bain & Company research study on product design showed that cross-functional teams reduce costs by 38% more than single-function teams.
With the input of sourcing teams, designers can take many practical steps to mitigate supply chain risk early in the process. For example, reducing the use of proprietary or customized components in a product’s design can help maintain an uninterrupted supply of parts, and any suppliers that can’t deliver orders can be more easily replaced before a product goes too far down the development path.
With a sourcing manager’s guidance, product designers can also create specifications for non-critical components that enable substitutions when needed. They can also consider adoption of standard parts across multiple products to simplify management of inventory and production lines, and to standardize the manufacturing processes.
Additionally, design and sourcing teams can diversify the supplier portfolio by agreeing to incorporate components into a product design that are provided by multiple suppliers in different locations. Teams can also explore the use of parts made in the U.S. or other countries that are less vulnerable to supply chain disruptions, if they haven’t already done so in response to the pandemic.
Collaboration at the design stage can also help address sustainability concerns by proactively researching how the selection of specific materials might impact energy consumption and emissions during production of a new technology under development. Teams can work together to optimize their processes for identifying component materials for new items while decreasing waste.
Ensuring product supplier engagement
Cross-functional design and sourcing teams should also actively engage with their suppliers to involve them in their supply chain risk management efforts. From suppliers, teams can gain insights about potential risks for each component, including end-of-life plans and issues specific to the countries that components are sourced from. Suppliers should also be expected to share details about the relationships they have with their own manufacturers and how they are managing risk within their supply chains.
Sourcing managers and suppliers should also work together to head off cybersecurity issues by creating an assessment process that verifies components and software prior to adoption.
Whether during the initial design stage or later stages of a product’s lifecycle, sourcing teams should be routinely communicating with suppliers to identify existing and emerging software vulnerabilities, and to make recommendations on which components best meet their regulatory requirements. Addressing cybersecurity vulnerabilities for components at any stage of their lifecycle helps reduce both financial and supply chain risk, as well as potential harm to end-users.
Many supply chain managers only learn about a new product once design has been completed, and are asked to order components for it. But companies can no longer afford to leave procurement professionals out of the product design phase. Only by prioritizing internal collaboration can companies ensure that external product lifecycle problems will be minimized.