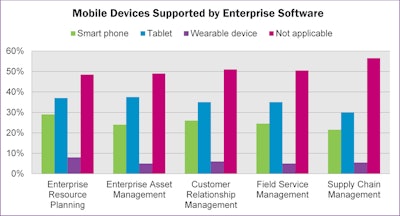
With the digitization of manufacturing offering potential cost savings of 3.4 percent p.a and $421 billion to the industry as a whole, digital transformation should now be on the minds of all decision makers—but manufacturers can find their path to digital transformation blocked by poor enterprise mobility.
Manufacturers are quickly realizing a digital transformation strategy can offer vast efficiency and cost improvements across the entire enterprise, but these strategies cannot be put in place without the right foundations. With digitized assets offering the potential for real-time data insights, paper-based processes are no longer sufficient enough to manage operations.
Mobile devices are entering the enterprise to help unlock the benefits of digital transformation. In a recent IFS study, “Enterprise Software Mobility and Digital Transformation,” of 200 industrial executives, mobility represented just as large of an opportunity for industrial organizations as it does for front-runners in other sectors such as Uber, Apple and Microsoft.
No Transformation Without Mobility
The study suggests that companies with employees accessing enterprise systems from mobile devices, such as enterprise resource planning (ERP), enterprise asset management (EAM) or field service management (FSM), were more prepared for digital transformation than their less-mobile peers.
Respondents who said their enterprise software prepared them well for digital transformation were more than twice as likely to access their software from a mobile device than those who said their software did a poor job of preparing them. These mobile-forward companies are in the minority though, as only 31 percent of respondents said they access enterprise software from a mobile device.
Knock-on Aftermarket Effects
According to IDC, by 2018, just 30 percent of manufacturers investing in digital transformation will be able to maximize its outcome; the rest will be held back by outdated business models and legacy technology.
Servitization of the manufacturing sector is heavily reliant on mobility. Servicing capital assets and durable goods needs a fleet of field service technicians requiring mobile enterprise systems to—at the very least—allow completion of work orders.
But delivering a successful customer experience and subsequently driving more revenue requires more than just work orders. Technicians and back office managers need access to data to ensure each dispatched truck is stocked with the right amount of inventory, and that projected demand for spares, repairs and consumables can be adequately met. All of this requires excellent integration with ERP and other back office systems.
Progressive service organization managers must also be able to automate scheduling and dispatch the correct equipment based on where the technician is located. Technician location should also automatically trigger notifications to the customer regarding their proximity and estimated time of arrival. These requirements mean enterprise software must leverage geolocation features of a mobile device.
Technicians also need to access detailed product specifications, video tutorials and other rich media to ensure they have the guidance to successfully complete each service task. This places a demand on mobile enterprise software and its ability to leverage features of a mobile handset.
The Power of Mobile
The transformative potential of enterprise mobility for industrial companies is real. Mobile access to software including ERP, EAM and FSM can bring many benefits. Here’s a snapshot:
- Improve the customer experience in the field.
- Provide real-time enterprise data, and deliver it into the hands of decision makers.
- Improve first-time-fix rates in field service environments, and create more reliable troubleshooting and less downtime in a plant environment by instantly providing information to technicians.
- Reduce the time engineers lose having to log paper-based processes or manually input data into separate systems.
- Enable in-field or plant floor workers and enterprise systems to leverage advanced geolocation and camera functions on mobile devices.
- Allow users to engage with software systems more frequently, increasing the return on investment for enterprise software.
The Lifeblood of Digital Transformation
According to Rick Veague, IFS’s chief technical officer in North America, increased engagement with enterprise systems may be the most significant transformative element of enterprise mobility.
“Mobile is the most obvious manifestation of digital transformation,” Veague says. “But when people use enterprise software from a mobile device, it indicates that the system is the lifeblood of the business. Your employees can connect into those core processes and participate even if they are not sitting at their desks. If you cannot do this, you will struggle with anything in digital transformation.”