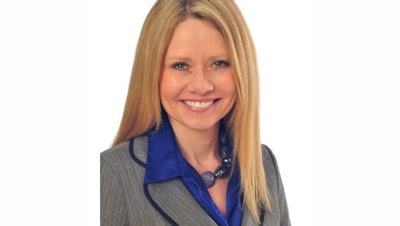
Supply chain used to be about transportation. Responsibility was looked at from a regional perspective. You were responsible for goods within your slice of the cycle. Once the goods left your hands they were out of your control. Today, supply chain has expanded and broadened—and companies have to know how they are moving things end to end. They are responsible for the full trip. Sometimes you’re responsible for goods that you didn’t ship or hold in your hands. There’s more responsibility and supply chains are a high priority, often reporting to the CEO. Smart manufacturing, or industry 4.0, is changing the way companies manage the supply chain and maintain responsibility for goods and deliveries. Here’s a look at some of the major factors behind the surge in interest in Smart Manufacturing.
-
Distributed Manufacturing. More and more companies are outsourcing their critical manufacturing processes—and their intellectual property—to third parties. Doing so means manufacturers lose control of production schedules. This results in inventory scattered throughout the supply chain that needs to be tracked down and validated. Depending on industry, this poses various challenges and risks ranging from quality, safety, counterfeiting and materials specifications. A Smart environment, with machines or factories plugged into a central hub to verify production, location and ingredients can deliver new levels of transparency that timestamps the manufacturing lifecycle.
- Virtual Manufacturing. Expansion into new markets and expanded growth overseas in places like Asia have driven manufacturers toward agile and virtual production, often closer to customers, to meet demand. In a smart supply chain, demand fluctuations in Asia can trigger demand signals to devices and parties all the way up to n-tier (multiple tiers in the supply chain) suppliers. In a true pull system, a signal of low inventory at a store in Beijing can ultimately trigger component production at a factory in Vietnam that has been identified by predefined data analytics as the best suited party and location to deliver the right component at the right time and cost.
- Thirst for Data & Visibility. A manufacturing executive recently shared a story of how his daughter could order a $20 product online and track it until it arrives at the front door. Yet the executive, who manufacturers multi-million dollar construction machinery, was unable to learn when an order for one of his company’s massive vehicles was due to arrive. We’re accustomed to real-time information in all aspects of our lives. In manufacturing, the days of manually piecing things together to know the status of an order are going away fast. No one needs an archeological project, piecing together old news to figure out where things went wrong. They need information on how things are running real time. Picture a network of machines, factories and parties sending signals and data back and forth at every step within a production lifecycle. The ability to store and use that data gets us closer to real-time business.
- Managing by Exception. It’s more important than ever to automate processes, flag issues and escalate as necessary. Straight-through processing, auto-compliance engines and analytics tools that trigger decisions are a few of the ways the managing by exception concept has been broadened. Machines and interconnectivity are leading the way. Smart manufacturing will have a huge impact. But keep in mind, when there are problems, humans still need to intervene. With so many moving parts, it’s impossible for anyone to look at the whole picture. Technology can be used to monitor and find the problems and supply chain experts can focus on problem solving.
- 3D Printing. There’s an immense amount of hype surrounding 3D printing and the technology will (eventually) completely change the industry. The entire design and development process for new products will be shortened. For example, the ability to create and print specific metal parts will reduce barriers. One of the biggest challenges in building traditional aerospace or auto parts out of metal is that it can only be cut into certain shapes. Digitally printed metal, however, can be molded into an infinite number of shapes. This is a game changer. An interesting shift already occurring today is around rapid prototyping. The ability to test new stuff and make it happen is sped up and enhanced. Consider design cycles of a car. Digitally printing a prototype of a part or component and testing it right away will change cycle times around designs. Looking at the big picture, 3D printing moves manufacturing further in the direction of capital intensive industry, versus labor. This means more automation, more data to feed the process, and more interconnectivity between facilities, machines, CAD systems and inventory sensors throughout the network.
Ultimately, everything we do today gets back to two things: customer service and profitability. Companies that can harness smart manufacturing, or industry 4.0, to better hit those targets will be exponentially ahead of their peers.
Machines talking to machines, and networks of ships, factories, shippers and suppliers—and all of their machines and sensors and gadgets talking to each other opens the door to having a better handle on the end-to-end supply chain. The challenge is harnessing all of that data, making sense of it and acting on that data. Global end-to-end supply chain visibility is more important than ever. It’s no longer OK to have data missing or late, and to try to piece things together like a jigsaw puzzle. Smart manufacturing brings us closer to this. But it’s not just the connections and signals: you have to have the network behind it to make use of the data.