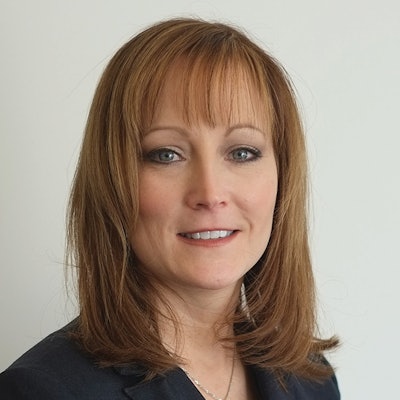
After experiencing quality issues that resulted in see-through yoga pants (yikes!), athletic apparel company, lululemon, named a new CIO to remedy supply chain issues that negatively impacted the company’s sales. Allan Smith was promoted from within, previously serving as the yoga-gear maker’s vice president of information technology (IT) engineering and operations. Smith chose to invest in customer relationship management (CRM) software to open up the lines of communication to clientele in order to receive positive, as well as negative, feedback in an effort to boost sales and shine the company’s tarnished reputation. Should other retailers follow suit? Maybe, but not without additional considerations and quality systems in place.
Customer retention and avoidance of potential product liability lawsuits are important objectives for all companies. An e?ective complaint and relationship management system is critical—but not necessarily paramount—to achieving these goals. In order to be successful, quality management software must provide the ability to log, respond to and investigate complaints. While CRM software could trigger a quality event in another system, such as an enterprise quality management system, it is not built for corrective and preventive action (CAPA), making it difficult for management to monitor and address developing trends through integrated reporting and tracking.
Recent trends in regulatory enforcement clearly demonstrate that technology, like CRM software, adapted on its own is no longer sufficient in maximizing and maintaining quality. Companies are increasingly being expected to close the disconnected points between key enterprise systems. Therefore, enterprise customers now expect any application they are planning to purchase to integrate seamlessly with other relevant applications in their technology landscape. Data must flow freely between applications and users. As such, it was established that best-in-class manufacturing companies often ensure real-time interoperability between their enterprise applications through the use of quality management software to streamline and tie systems together.
While it’s commendable that lululemon invested in CRM technology to help react to customer complaints, manufacturers should consider taking a more proactive approach to ensuring products are brought to market safely and up to brand standard, thus avoiding product quality complaints altogether. While CRM could help right the ship when it comes to supply chain errors, investing in preemptive technology, such as enterprise quality management software (EQMS), could be the tech investment CIOs industry-wide actually need.
EQMS helps manufacturers optimize quality, ensure compliance, reduce risk and lower costs by identifying, containing and addressing problems upstream. This preventive method is a lot cheaper than reacting to issues as they arise or are discovered by consumers in the marketplace. EQMS can also help connect suppliers to ensure that quality is upheld throughout a product’s entire lifecycle, again helping ensure faulty products never leave the manufacturing plant.
Extending the enterprise to include crucial stakeholders is critical and should be a part of a corporate mandate of quality. Folding additional technologies into your quality control processes, such as training management, product registration tracking and analytic tools, can also help ensure there is continuous improvement within the enterprise and value chain.
Increasingly globalized supply chains means supplier connectivity is more important than ever; however, multiple or inconsistent sources of information coming from your suppliers can easily create confusion and lack of unity. As such, manufacturers should look to implement a global audit process to ensure each supply chain partner is compliant and properly managing all quality-related processes.
Instead of just connecting suppliers, EQMS can go a step further, helping to streamline and automate audit processes to ensure quality is being upheld throughout the entire manufacturing process. The advantages of performing a successful, effective audit that confirms all participating parties are compliant is also reflected in the reduced costs faced by the company as production continues to move forward.
For example, if lululemon was able to pinpoint that Fabric Supplier X was providing fabric that did not meet quality standards, the company could instead choose a new fabric supplier before moving into production. Though this may halt production slightly, lululemon could guaranteed the quality of its final product, thus avoiding a costly recall and subsequent damage to the brand’s reputation.
Soon after its inception, lululemon’s target audience became devoted customers, believing in the company’s mantra: “Sweat once a day.” While it’s easy to assume that the company certainly was sweating once complaints about the see-through pants started rolling in, it’s great to see that lululemon’s new CIO is committed to vetting and responding to future complaints to help ensure the brand’s reputation reaches its previous heights. Other manufacturers, regardless of industry, should pay attention to another line in lululemon’s manifesto—“listen, listen, listen, then ask strategic questions” —to learn from the quality mistakes that the athletic brand made in order to invest in technology that helps ensure issues never make it to market.
Kelly Kuchinski , industry solution director at Sparta Systems, has 20 years of product management and marketing experience with a focus on consumer packaged goods, chemicals, life sciences and technology. Prior to joining Sparta Systems, Kelly focused on developing products and solutions to support companies across multiple industries to enhance functionality, increase efficiencies and reduce costs.