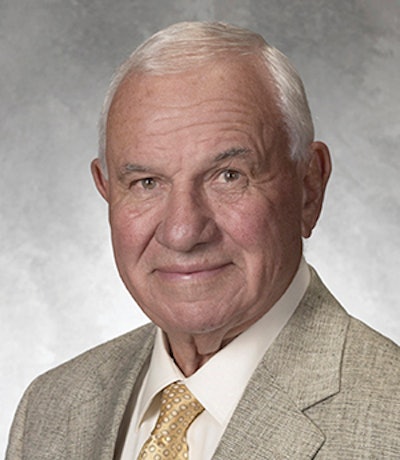
Tornados, hurricanes and typhoons are acts of nature to be endured; they exist and devastate. The standing opinion is that very little can be done about the effects they have on those affected. They are endured and the beat goes on.
It is reminiscent of a company’s maintenance, repair and operations (MRO) storeroom which, at times, is a real “Storm Room.” Acts of nature constitute unreliable, unpredictable situations rather than a calm, serene and productive weather pattern, or in the world of lean maintenance, a reliable, world-class MRO storeroom.
As in weather disasters, the typical “Storm Room” is viewed as a situation to be endured and tolerated since nothing can be (or will be) done to improve it to protect those in need.
Well, unlike storm patterns and force majeure, there is a solution available that can correct the devastation caused by MRO stores. The functions that are performed in the day-to-day operation of a manufacturing factory can be classified into two areas: Those actions that directly relate to the production of the products manufactured and assembled, which go into finished goods inventory, and those actions that support the manufacturing mission.
These support activities consist of:
- The cafeteria.
- Security.
- Landscaping and ground maintenance.
- Legal.
- The MRO storeroom.
With the exception of the MRO storeroom, all of the above-mentioned support activities are outsourced to companies who employ experts in the functions they perform. Companies do not cook and are not the purveyors of foodstuffs. Security is left to those who employ state-of-the-art controls to keep the facility safe and out of harm’s way. Landscaping companies are charged with providing beauty to the facility and a pleasant work environment. There is always outside legal advice because companies need lawyers who studied law.
Why do companies continue to operate their own MRO storerooms when they are not in the hardware store business? They are not a Home Depot or even an Ace Hardware; they are not cooks, not gardeners, nor lawyers. Any function within the manufacturing process that does not contribute to the profit structure of the product produced is improved, corrected or eliminated. This is not the case with MRO stores where the profit drain is endured, ignored and allowed to exist.
Why does the condition continue to exist? The answer is complex with a myriad of factors contributing to that complexity. The major barriers to change are:
- Lack of management focus and many disciplines influencing decisions.
- A clouded and undefined MRO mission.
- Job protection and the fear of loss of importance.
- Supplier preference and resistance to change.
- Anticipated high opportunity costs.
- No time to consider change, as in “my plate is overflowing now.”
- Little recognition that value can be released from MRO change, meaning that opportunity cost vs. return on investment (ROI) is not defined or even considered.
- Lack of knowledge to determine the optimum change scenario (how will it work?), how to implement the change, how to sustain the change and how to report the value (justify the value).
- Fear of failure.
There are two considerations to stop enduring the “Storm Room” situation and effect change to a lean, maintenance-connected, world-class MRO stores operation.
- Do it yourself. If you can accomplish it yourself, then consider cooking for the cafeteria and securing the grounds yourself … It makes no sense. You can’t do it yourself or you would have, or you can’t do it yourself because of your position in the MRO supply chain.
- Outsource it to a third-party MRO (3PMRO) provider.
3PMRO companies must provide proof of:
- Total corporate dedication to on-site MRO management.
- An extensive history of on-site success.
- Purchasing power and willingness to share costs.
- Dedicated implementation teams.
- Associates who are trained in world-class MRO management, as well as knowledge of lean maintenance reliability requirements.
- Willingness to guarantee performance vs. key performance indicator (KPI) measurements.
- Dedicated operational support for sustaining the functions of the 3PMRO agreement.
- Financial stability and support for on-site agreements.
By requiring your selected 3PMRO provider to comply with the above tenants, there is no need to assume the unnecessary cost of conducting a “market basket” request for quotation (RFQ) or any other of the costly functions companies go through to select a supplier. Define what you want from the provider you select, establish the price structure you can support and agree to the guarantees necessary to sustain the agreement.
You can now realize the world-class, reliable, connected stores operation can contribute to plant profitability. It is no longer necessary for companies to endure the profit drain and unreliability affected by the traditional MRO stores operation. You can and should get out of the “Storm Room” business.
George Krauter currently serves as the vice president for Storeroom Solutions Inc., Radnor Pa. He is a recognized authority on the role of the MRO storeroom in supply chain management and reliable maintenance. He has published his experiences in Uptime, Modern Distribution Management, My Purchasing Center, and Supply & Demand Chain Executive. He is a frequent speaker at industry conferences, including Reliability 2.0, ISM Indirect Conference, International Maintenance Conference, The Conference Board, and events for APICS, SMRP and ISM professional chapters. He holds a B.A. and M.B.A.A. from Temple University.