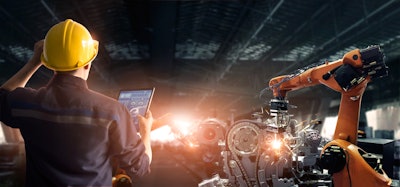
The Coronavirus disease (COVID-19) pandemic has brought to light many gaps in the supply chain, as it has been stretched increasingly thin. But, as the supply chain struggles to maintain business as usual, many companies turn to technology for help.
While the virus has stalled exploration and testing of emerging technology and innovation, it has also pushed supply chain companies to introduce technology where they would not have in the past to help keep their businesses moving during the pandemic.
“The supply chain is reeling from the effects of the COVID-19 pandemic, which has impacted the exploration of technology,” says Melanie Nuce, senior vice president of corporate development at GS1 US. “While a lot of innovation projects have been put on hold during these economically challenging times, we believe emerging technology will continue to be explored to solve persistent supply chain challenges. In many ways, the COVID-19 pandemic has brought existing visibility and data quality issues to the surface and many companies are more committed to finding a way to address them.”
Large-scale technology launches can take up to seven years. But, smaller scale activations are what companies look to launch quickly to help increase demand and keep employees safe. Some even say that those who have failed to implement large-scale technology deployments are already too late, since the transition period is so long.
“Many of the supply chain industry’s least desirable common practices are being replaced or circumvented with technology, but it’s almost too late for those that haven’t yet started planning for these transitions considering how long they can take,” says Ken Fleming, president of Logistyx. “With global retail holding companies mapping out 5- to 7year transition plans and some of the most established U.S. retailers requiring as much as three years or more each time they update their warehouse management system, it’s easy to understand why organizations that haven’t already launched these initiatives would hesitate to go to such lengths to embrace new technologies become more efficient and better serve customers.”
Most companies are having employees who can work from home do so, using remote tools to handle their work tasks. This has caused businesses to deploy a variety of paperless tools and software to handle processes outside of their offices or locations.
Some tech providers are even expanding their offerings to help companies operate remotely. For instance, Augury released new capabilities in its software that is already used to manage the health and operations of machinery, but now creates a more robust diagnosis with added feedback and remote views of history and health support from experts. The idea is to better manage the machines off-site.
Those who have automation and technological services already enabled throughout their businesses could have had a potentially easier time dealing with the pandemic crisis and social distancing between employees. Some larger warehouses are so advanced in terms of automation that areas are off limits to human personnel, which means during a pandemic, operations in that area of the warehouse can continue.
“Big warehouses are almost 100% robotic and automated,” continues Fleming. “People only intervene when problems happen, a box gets stuck, something gets jammed, etc. In these fully automated warehouses, nobody is picking products off shelves or packing boxes; on-site personnel manage maintenance, engineering and related tasks. We’ve even seen some warehouses where people cannot even enter the physical space. In cold food storage, for example, some have begun removing oxygen to reduce the energy requirements to refrigerate food by as much as 80%.
“On the other end of the spectrum, in smaller warehouses that still rely on a lot of manual human intervention, technologies that speed up these manual processes continue to gain steam and market share. Scanner gloves, for example, from a wide range of manufacturers help warehouse workers scan products while they pick them from the shelves to save time, and this is just one example. Across the board, these ‘human assist’ technologies keep getting better and more advanced,” adds Fleming.
Smart supply chain
The supply chain as a whole leans toward smart manufacturing, where most of the supply chain process is managed with systems embedded into the Internet of Things (IoT).
“Smart manufacturing is automating and optimizing the flow of production, procurement and logistics,” says Klas Orsvärn, founder of Tacton. “This makes it attractive to move production closer to the market. It also makes it possible to produce customized products efficiently, to compete on value and protect margins.”
Today, a variety of containers and pallets are now equipped with smart technology that can help increase visibility and reduce error during the logistics process. For instance, RM2 has launched a pallet design named BLOCKPal made of composite material with extreme durability and enabled for radio-frequency identification (RFID).
Impinj also features solutions that show real-time movement of goods in and out of the warehouse and dock doors, location tracking for individual items inside the warehouse and automated verification that makes sure each carton is packed with the correct item and is placed on the correct pallet.
However, while coffee makers, washing machines, vehicles and other consumer appliances and electronics have been a part of the IoT world for a while now, logistics products have only just begun to become “smart.”
“Some of the most exciting technologies emerging in the supply chain industry today are the sensors technologies that extend the Internet of Things (IoT) beyond devices to connect more things to the Internet,” says Gaylene Meyer, vice president of global marketing and communications at Impinj. “By ‘things’ I mean containers, pallets, boxes -- things that, until recently, were not included in IoT.”
But, as the supply chain gets smarter, many warehouse workers worry about job security and whether a robot will replace them. The debate in this area remains strong, as some emerging technologies help augment an employee’s job and make it easier, while others can replace the worker all together.
Those that are helping their employees see the benefits of these emerging technologies and use these processes in tandem with skilled staff members will see a more stable future. When these systems become integrated with IoT, companies can gain a significant amount of data to make their businesses better in the future in a multitude of ways, including predicting demand, reducing common pain points and projecting the best solution options. As the sensors on the IoT solutions pick up the data, artificial intelligence (AI) can process this data for better decision making.
For instance, Tacton’s Design Automation can configure optimal solutions in a company’s operation process based on sensor data to create a more streamlined operation.
AI makes sense of your data
One of the most talked about facets of emerging technologies is AI, which features a wide range of abilities.
“In the short term, AI has been more frequently used for telling software and computer systems what to look for and what to do,” says Fleming. “But, in the future, AI’s role will be to better make sense of data.
“In the near future, supply chain AI will begin to migrate to machine learning. Currently, supply chain AI consists of developers programming business rules, telling computers what to look for and what action to take when it encounters those situations, but as AI migrates to machine learning, it will begin to think for itself. As machine learning becomes more advanced, technologies will increasingly be able to make note of repetitive situations and past experiences to start learning and making recommendations on its own. Technology like this has already deployed on a wide scale in other industries, and it has the potential to rapidly automate and improve a wide range of supply chain processes,” says Fleming.
While other industries have learned to tap machine learning for decision making, the supply chain has only just begun to tap the surface. And, there is a major issue that can hinder the process. So much of the supply chain is managed by different companies working together, but each company uses their own preferred technology and not everything is compatible. Many companies even use a multitude of technologies within their own businesses that do not interact. This is a major flaw in the system and stops the ability to grab and make sense of useful data.
A few tech companies in the supply chain such as GS1 focus on the ability to work with many different solutions, but this is not the case throughout the entire supply chain .
“In a more general sense, the pain points associated with technology implementation largely hinge on a company’s data sharing capabilities,” says Nuce. “For example, Organization A is supplying carrots to Organization B’s store using blockchain platforms offered by their respective technology providers. Can the data from Organization A’s system be easily accepted by Organization B’s system? Globally unique item identification is the core basis for a common language for the exchange of information. The use of GS1 Standards for identification and data sharing ultimately breaks down the barriers created by proprietary data sharing, both within organizations and externally.”
The sharing of data and interaction between technology platforms is a significant problem plaguing the supply chain, but it is on its way to rectifying.
“There’s a lack of consistency,” says Albert Lee, chief technology officer at Odyssey Logistics & Technology Corporation. “EDI/APA connections, customization and system requirements vary across shippers, carriers and 3PLs, making it difficult to take advantage of all the available technology. Very few have the integrated connections to make everything run seamlessly. Fortunately, many are getting closer. Leaders have to ask themselves whether their current systems are too limited. Can they become more integrated? Can they connect with the available people and resources to handle customization?”
If partners can tap into that stream of data from the various points of business, AI will become even more useful.
“The near future will see a mad grab of data elements wherever they may be,” says Jeremy Hudson, director of consulting services at Open Sky Group. “Great AI requires significant data from multiple streams. I think we continue to see software companies look for opportunities to harvest and mine data to provide more advanced metrics and decision-making tools. I think that we’ll see more IoT devices assist in this effort, and ultimately contribute to better decision making throughout the supply chain. The supply chain’s biggest need now is not new solutions, it is tools to make better decisions. Many of the supply chain pain points we see are due to bad decisions and misguidance, which leads to downstream volume constraints and waste.”
Open Sky Group consults with supply chain and logistics companies to help find the best solution for that particular operation and better implement it into the company’s existing processes.
The potential of AI and data is significant for companies, as they learn to streamline their businesses and prepare for future unknowns. But, the usefulness of data is only as good as its quality.
“An AI system needs data in order to become smart,” says Meyer. “And, the more data it has, the smarter it gets. Both the quality and value of data inputs are critical to the effectiveness of an AI system. When we refer to the quality of data, we mean the accuracy, fidelity, and specificity of that data. You must be confident data reflects reality, metrics are repeatable, and the data is complete--reflecting all there is to measure. In addition, the data must provide value, not noise. It must be understandable and actionable.”
Following the shipment
One of the favored aspects of a smart supply chain is the ability to see real-time information on a shipment’s status and whereabouts. Visibility is a key factor in logistics, as companies have now become accustomed to knowing greater details about their shipments. Technologies such as RAIN RFID, GPS trackers and blockchain software have brought more visibility into the supply chain to help logistics partners better serve their customers.
For example, GS1’s RFID EPC technology fits a variety of logistics hardware such as rail-freight wagons with sensors that interact with fixed readers at various points in a shipment’s journey. This allows companies to track shipments as well as the condition of the mode of transportation like the health of the truck or rail.
“RAIN RFID, a battery-free wireless technology is providing accurate real-time data about the items and packages that move through the supply chain,” continues Meyer. “RAIN RFID’s unique capabilities – it can identify thousands of items in seconds at a distance and without line-of-sight, it requires no batteries to operate and can last indefinitely, and can identify each item uniquely with cryptographic item authentication – position RAIN to be the leading item-to-cloud connectivity technology for the IoT.”
These systems, sensors and data can significantly reduce the number of mistakes associated with human error that happen on site during the transportation of goods. Eliminating these errors can help logistics companies on their bottom line as well as keep customers happy. As these sensors such as RAIN RFID collect data from the individual boxes or pallets, it connects with the larger supply chain management systems to create a holistic view of the operation, monitoring to create the correct quantities at the correct location at the appropriate time. This also allows managers to see the more common pain points in an operation and eliminate them.
“Stand on a loading dock of a busy distribution center and you’ll see dozens of trucks pulling up to dozens of dock doors with thousands of boxes traversing the facility floor,” adds Meyer. “Even if this facility is running with 98% accuracy, the cost of errors adds up every hour, every day. And the hard cost of each error is only part of the problem. Disappointed customers will choose a different supplier they can rely on in this competitive world.
“According to a study by the University of Auburn, RAIN RFID raises inbound shipment accuracy from suppliers from 31% to 99.9%. This accuracy translates into better visibility, leading to a better customer experience,” says Meyer.
One example of a smart supply chain process is Odyssey’s warehouses, which are equipped with many of the emerging technologies in action such as barcodes, RFID, stock rotation and remote access to location inventory management. This allow its partners to have complete visibility into their products while Odyssey manages the distribution.
Another technology key in visibility is blockchain, which is on the rise in the supply chain. Blockchain can integrate with the IoT services that help move shipments and records it in a secure and understandable way. The healthcare sectorseems to be getting a leg up in this area.
“Blockchain, despite the hype surrounding it, can be revolutionary in supply chain because it has brought key stakeholders together to take a closer look at what’s not working from a data management perspective,” says Nuce. “Blockchain is reinvigorating the conversation around improved data sharing, and increasingly companies are engaging more broadly with their trading partners to share accountability for the visibility of products across supply chains. The food and healthcare industries have the highest concentration of pilot programs under way right now, as recall responsiveness and product traceability are key to meeting the requirements of FDA regulations.”
Robotic takeover
While sensors gain information from pallets and shipments and AI sorts the data, some technology even moves itself. One of the most futuristic aspects of the supply chain is robotics, of which many are equipped with AI themselves, allowing them to operate without a human worker.
Some of these systems are indeed replacing employees, as they can complete tasks faster and with less error. As mentioned before, robotics systems have been helpful to those who have implemented these technologies during the pandemic, as companies need less workers in close contact. But, these robotics systems can be costly, and time of deployment is significant.
Most of the robotics systems are used to streamline warehouse operations and remove strenuous and tedious assignments that workers dislike.
“Companies are using mobile robots to replace tedious, mindless jobs, while at the same time augmenting those jobs with roles that are more stimulating,” says Lior Elazary, co-founder and CEO, inVia Robotics. “There is work that is perfectly suited for robots, specifically repeatable tasks. And, there is work that is perfectly suited for people, specifically making decisions. What the proliferation of automation allows for is for people and robots to do what they do best.
“This is particularly important in the current COVID-19 environment. Businesses are focusing on keeping a core team intact and safe. They’re employing robots to help that core team be more efficient at making decisions and ensuring efficiency at an overall warehouse level. At the same time, they’re mitigating the risk of needing to hire a fluctuating, transient workforce to carry out rote fulfillment tasks,” Adds Elazary.
The ideal environment in which a person and a robot work in tandem is one where robotics handle repetitive tasks like continuously retrieving and moving items throughout the warehouse, specific jobs carrying out commands. Human workers are suited for assessing situations and making intelligent decisions on what commands to give the robots. Working together in this way can create an ideal and efficient workplace.
Some robotics in place operate the same way an autonomous vehicle does, with the ability to move around the warehouse with awareness to their environment, without having to be manually controlled. For example, inVia’s robotics system includes AI-enabled robots that move throughout a warehouse on their own and can be monitored through remote software. The idea here is tp reduce unnecessary travel throughout the facility, thus wasting time and energy of the workers. The robots are also fitted with pickers that can easily move items.
Autonomy offers such a range of opportunities in the supply chain that logistics companies are even flirting with the idea of adopting autonomous efforts outside the warehouse, completing shipping processes and last-mile deliveries through driverless vehicles and even drones to help offset the driver shortage.
Listen to our podcast on drones in the warehouse here:
But, the most current technology in place throughout the supply chain is automated guided vehicles (AGVs) that uses sensors and cameras to move around the warehouse just like driverless cars. Its ability to see the entire 360-degrees around itself can help with safety, allowing it to know if another object or person is nearby or is likely to come in contact and then react. AGVs can be especially helpful in areas of the supply chain where it is difficult to find workers.
“AGV technology is becoming more prevalent in operations where we’re seeing skilled worker scarcity,” says Hudson. “We see this as a solution for replacing the skills (and risks) of humans driving heavy equipment.”
In addition to AGVs in robotics, there are also automated storage and retrieval systems that can find, retrieve and put away items, goods-to-person (G2P) technologies that grab and deliver individual SKUs to human workers, autonomous mobile robots (AMRs) that can operate on their own and robotic arms that help with pack-and-pick.
However, with all this growing technology, right now it is unlikely for a fleet of robots to completely replace human workers since inconsistencies are rampant.
“Augmentation continues to be the resounding use of technology advancements in the supply chain,” continues Hudson. “Most supply chains are not self-contained and rely on a global network of suppliers and customers. By virtue of these interdependencies, we continue to see vast inconsistencies and a lack of standardization throughout all supply chain-related facets. Robotics are simply not to a point where these inconsistencies and variances can be handled at a rate and cost that is comparable to humans.”
There are some solutions that can aid in streamlining the warehouse process through augmented reality, where staff can wear accessories such as smart glasses to help guide them through their jobs in a faster and more precise manner.
For instance, Neovia Logistics has entered into an agreement with Picavi to introduce the latter’s smart glasses to Neovia locations worldwide. Employees improve outbound order accuracy through a hands-free visual guidance system, meaning the glasses direct users to the exact location of a needed item in a warehouse. The technology also significantly helps in onboarding new employees, allowing trainers to show the new employee the exact work steps. In addition, sensors help pinpoint common pain points in the work process, so managers can readjust strategy.
Other uses of AR can help with planning processes. Tracton features a visualization system through AR that helps partners create 3D images based on reality to better manage expectations and what the warehouse and shipping process will actually look like.
Emerging technologies like AR, AI, smart warehouses, robotics and sensors will help streamline businesses, reduce pain points and increase bottom lines. Cooperation from partners and staff will only modernize the supply chainAs innovation in these technologies continue, warehousing and logistics can become even smarter and modernized places of business.