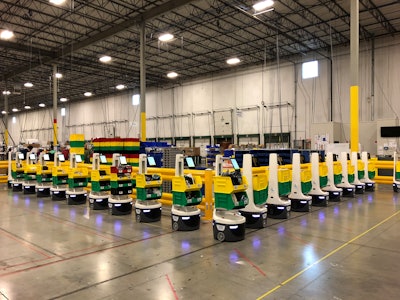
Now more than ever, it is crucial to have automated solutions within the warehouse, as supply chain disruptions can occur within a blink of an eye.
The Coronavirus disease (COVID-19) pandemic, which has already laid off 18% of the U.S. workforce, as of March 18, and displaced several workers from in plant to working from home, is one example.
Locus Robotics' machines ease strain on employees by guiding them to a certain item in the warehouse.Locus Robotics
That’s why embracing automation is critical to any organization’s survival in today’s environment.
“Robotics are helping in various ways such as reducing walk time for our employees, assisting in repetitive motion processes so our employees can do more valuable tasks and reducing the need for moving product long distances across a warehouse,” says Kevin Stock, senior vice president of engineering at GEODIS, Americas. “Retaining our employees and making them more productive is key to being successful.”
Automation and robotics have improved many tasks typically assigned to warehouse staff. For example, robotics and automated equipment perform assignments at a quicker pace and with less effort—potentially making the workplace even safer. This allows warehouses to shift human capital to more valuable functions and gain greater efficiencies.
“In order to do more, [warehouse operations] have to do something differently. They also want to do things better, which means doing things more safely,” says Jeff Christensen, vice president of product at Seegrid, Pittsburgh. “If you think about the core competencies of human beings, if you’re driving a truck in a loop all day, you’re going to get bored by Day 2. And, when people get bored, they improvise. When they improvise, they make mistakes. If they’re moving 5-10,000 pounds of material when they make a mistake, somebody is going to get hurt.”
Technology improvements such as artificial intelligence (AI) and visual detection systems also automate warehouse forklifts, pushcarts and small-vehicle fleets.
Automated guided vehicles (AGVs) use sensors and cameras to guide the machine up and down the aisles, acting as the machine’s “eyes.” Because of the technology embedded within, AGVs can sense where objects are going to pick up and drop off, moving at a slower rate than the average human.
Locus Robotics
Safety and utilization of the equipment oftentimes makes up for the difference of picking times, Stock says.
“Since AGVs rely on cameras and sensors to detect obstacles, they are constantly surveying their environment in 360 degrees,” Stock says. “This allows the AGVs to detect not only static objects that they are approaching, but [also] other moving objects that may be approaching them. Anytime an AGV observes movement in its ‘safety halo,’ it will slow down or stop and not move again until the area is clear.”
In fact, AGVs may be the easiest to implement because the motorized cart can reduce strain on humans as it eliminates walking long distances, according to a white paper from Kindred, Louisville, Ky.
However, high investment costs and limited flexibility have halted the implementation of the vehicle in warehouses.
“I think some of it is just sort of old-fashioned inertia, the technology adoption lifecycle and sort of what level of risk different companies are willing to take,” Christensen says. “In the near term, you will see the whole spectrum of risk acceptance vs. risk aversion in the market.”
It is still imperative though to be flexible when implementing robotics, as there are several factors that affect automation.
For example, layout of the operation, temperature of the warehouse and number of aisles and racks can play a factor into how much time it takes to fulfill an order.
Warehouse managers need to ensure that employees understand how AGVs operate. By understanding and measuring return on investment, multiple shift operations can gain the fastest payback.
The following technologies are also projected to help fill gaps in the warehouse:
Automated storage and retrieval systems (AS/RS). Designed to retrieve and put away goods, warehouses choose an AS/RS based on their needs and software to manage a majority of their operations. This machine also allows employees to work more efficiently while reducing physical activity.
Goods-to-person (G2P as applied AS/RS). Created to deliver a desired product, package or SKU to a fixed pick station to help staff fulfill orders, some devices may return goods to their slots if no longer needed.
Autonomous mobile robots (AMRs). With these robots, carts and trucks move independently without needing direct intervention or assistance from a human. Solutions are integrated with fixed-location robots to bring goods and materials from shelves to the final station.
Piece-picking solutions. Often referred to as robotic arms, piece-picking solutions focus on the movement and protection of goods within a certain location. Currently, they are used to help warehouses with product receiving and storage, and support pick-and-pack for goods that move at high volumes.