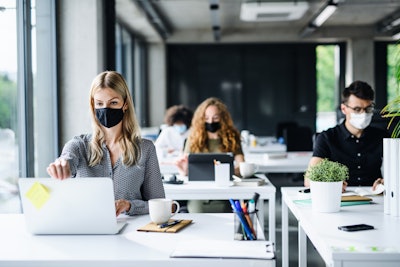
Twenty straight months of economic growth. That’s according to the latest manufacturing PMI from the Institute for Supply Management (ISM).
Let that sink in and think about how far we’ve come. As we approach the two-year anniversary of the Coronavirus disease (COVID-19) outbreak in the United States, it’s a great reminder of how many businesses have emerged and rallied from the bleak and dark days of spring 2020. But how?
The ISM report says “The U.S. manufacturing sector remains in a demand-driven, supply chain-constrained environment, but January was the third straight month with indications of improvements in labor resources and supplier delivery performance. Still, there were shortages of critical intermediate materials, difficulties in transporting products and lack of direct labor on factory floors due to the COVID-19 omicron variant.”
Industrial parks are lined with hiring banners and starting wages are like watching a stock market ticker, and despite unprecedented recruiting efforts, management conversations have turned to growth without talent.
Manufacturers and distributers are looking to COVID-19-decimated industries with high unemployment such as hospitality. Starting wages of most manufacturers are multiples of hospitality and the days of dark, dirty and dangerous manufacturing are well behind us. Manufacturers are recruiting on the platform of stability, wages and countless opportunities to make meaningful differences every day.
Companies have increased internal referral bonuses because new hires are probably gainfully employed and need to be lured away. After all, someone is more likely to make an employment switch if a friend or relative is employed with the company and speaks praises. The winners in this strategy are offering referral bonuses 2-3 times the rate of the signing bonus. Everyone wins and retention is firm.
Making every minute count is a familiar phase heard across the country. Maximizing throughput with understaffed crews seems like insurmountable expectations, and yet somehow, the hearty manufacturers continue to forge ahead. They make every minute count with the use of machine sensors that tally where unplanned downtime minutes leak away. These same technologies provide watch dog platforms sending under performance alerts, predict when it will occur again and leverage artificial intelligence (AI) to pair people and machines to maximize their full potential. And, in the back office, automated workflows are forecasting materials and placing orders based on inventory levels, suppliers are replenishing based on automated alerts they receive and accounts payable, augmented reality (AR) and banking transactions are taking place with less need for human intervention.
Wipfli recently surveyed nearly 200 manufacturing executives to analyze how they’re managing challenging business conditions. It turns out a majority are not planning to pursue growth avenues over the next 3-5 years, including efforts in existing markets, new markets and stunted M&A.
Quality control, energy management, maintenance, etc. have failed to take advantage of Industry 4.0 technologies. A majority of survey respondents are running at less than 80% of production capacity. This is due to a high percentage of firms having only some – or no application – of Industry 4.0 for these work tasks. This is where current efforts are focused and what will help in recruiting and retention in the long run, and why growth avenues have taken a back seat.
Taking it a step further, about two-thirds of manufacturers require upgrades to their network infrastructures to enable digital communications (e.g. machine to machine, machines to the enterprise, machines to suppliers, machines to customers). This oftentimes requires major network upgrades or overhauls of an enterprise resource planning (ERP) system.
Technology, machines, data — they can only go so far without putting critical thinking behind them. While manufacturers rely on machines to operate seamlessly on their own, that’s not going to change, and companies are finding greater value in implementing technology and the necessary management system at the same time. In turn they’re becoming more resilient as an organization and better able to grow. Resilient manufacturers are more than digital supply chains and intelligent lots; they use knowledgeable management to turn average workers into advanced workers.
Manufacturers have become technology companies first. The dependency on automation, robotic processes and AI has emerged as the price of entry for the next manufacturer.
In today’s digital age, it’s easy for manufacturers to hear Industry 4.0 and get caught up in everything that can accompany it, from AI to the cloud to the Internet of Things (IoT). We’ve seen clear winners emerge two years after the onset of the COVID-19 pandemic. The common ground? A top-down embracement and commitment to Industry 4.0.