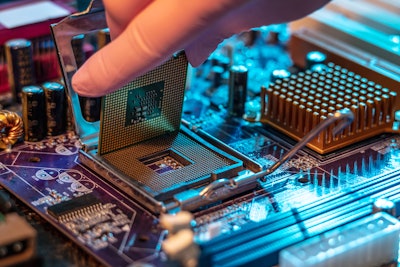
In many factories, you’ll see dashboards filled with colorful graphics and numbers that are rarely looked at. Field technicians will be supplied with apps on tablets that they are tasked with using but don’t necessarily understand how or why they are using it. Ultimately, the initiatives are thrown in the bin with some 70% of digital transformation projects that fail.
In such cases, it’s easy to blame the technology and say it’s not ready for real time. More often, though, the technology is fine; it’s the organizations themselves and business processes that aren’t ready. Digital transformation is a buzzword that people fixate on, without understanding the human and real-world implications of implementing new technologies, especially in an industrial space. Here are the five dirty little secrets of industrial digital transformation.
End users are often given the wrong technology. Industrial digital transformation must be actionable at the lowest levels of the organization. The key is for people throughout the organization to understand the WHY of how changes will impact their work and the goals of the business. The technician turning the wrench or climbing up on the roof to fix an issue must see how an artificial intelligence (AI)/machine learning (ML)-infused technology allows them to do their job better or faster or with a lower failure rate. Too often, though, projects are developed for personas without spending time with real individuals to truly understand how they do their job and what they need.
Think about the companies that have thrived in the digital era. Their competitive advantage is the customer experience. They take a customer-centric, design-centric approach. While the consumer and industrial settings have many differences, the need to create a compelling customer experience cuts across all sectors. However, the industrial space often gives little true thought to the end user/customer when implementing digital solutions.
Projects overpromise and under deliver. When predictive maintenance projects or other digital initiatives are proposed, they often make grandiose promises, which aren’t met because of issues like a poor user experience. The projected result might assume that a technician will use the technology to complete an action 100% of the time, when in reality he only uses it 25% of the time. That might result in a $25 million savings, which is still valuable, but everyone is slightly disappointed because the promised $100 million in savings wasn’t realized.
To get the biggest payoffs, you’ll endure lots of friction. A key difference between the industrial and consumer space is that industry tends to be more static. Manufacturing automation systems can be implemented and used for a decade or two. New data sources are added to processes infrequently. This stagnant approach can stymie creativity and innovation.
For example, consider the case of a large engine manufacturer who literally didn’t know what plant their turbines were built in. When it was suggested to track this information, to better monitor and analyze equipment failures, the response was that this extra step did not align with “the priority of getting the engines out the door quickly.”
Thus, the manufacturer was robbed of a key piece of data that could have been used to improve their product. This is like making a cake with only three ingredients. It might taste all right, but it will be dazzling if you take the time to add a fourth ingredient and let it bake just a little longer. Adding more data sources can increase friction in the short term, but the long-term payoff in improved results will be more than worth the effort.
Making it “great out of the gate” is a recipe for failure. By their nature, engineers like to build stuff. They don’t want to study a pile of Legos; they want to turn those Legos into something – fast. As a result, too many companies try to design projects out of the gate that have the perfect architecture that scales automatically while providing the full functionality that every user will need.
In their haste, engineers often don’t take the extra time to validate how the technology will be used and what data sources will be needed to accomplish actionable tasks. Instead, these projects need to be developed with an iterative approach of “get a quick win, demonstrate value, then scale.”
There is no finish line for digital transformation. People sometimes think starting fast means they’ll get to the finish line quicker. The digital transformation projects that fail are those that hire a consulting firm to come in for nine months, with the expectation that the company will be digitally transformed by the time they leave. Digital transformation is a never-ending journey. Expecting to have a completion date for digital transformation is like having a completion date for innovation or education. There is never a time when you stop learning or innovating.
The “dirty little secrets” of digital transformation aren’t meant to downplay the importance of digital technology. Just the contrary. Adopting digital technology is vital to any company that wants to remain competitive. However, you must approach digital transformation in a realistic way, understanding the human and operational issues you’ll confront. Acceptance of the new normal and how it impacts both day to day and long-term activities is vital to sustaining the progress and achieving the desired outcomes. Digital is a journey, and not an easy one. By understanding the dirty secrets, you can avoid or at least anticipate them and steer your digital transformation initiatives in a way that leads to success.