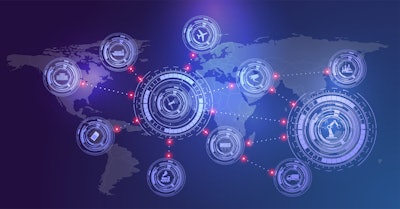
The supply chain and logistics industry is experiencing a significant season of change within the processing sphere, undergoing a general shift from manual to automation. With any major change anywhere, debate and discussion is an inevitability… and the logistics industry is no exception. Much of the discourse has examined both the benefits and the pitfalls of manual and automated processes. There has also been a rise in the discussion of an amalgamated approach, using both manual and automated processes within the supply chain world. Manual planning, implementation, and control of the movement and storage of goods and materials is a tried, trusted and traditional form of approaching supply chain processing.
This subject-reliant approach uses human labor in all aspects - from packing and shipping, to decision-making and planning. Traditionalists in the industry, apprehensive about the changeover from manual to automation, seem to be approaching the situation with a, ‘If it ain’t broke, don’t fix it,’ mind-set. Moreover, the technological boom within the supply chain industry is also creating fear around the necessity of human labor, and thus, the security of jobs. However, a refusal to digitize and grow with the automated ways of the future might see an amplified risk of these supply chain and logistics companies being left behind.
Manual or automation...or both
There are many benefits to manual processes in the supply chain industry that would be regretful to overlook. One of the most significant benefits of manual processes is the level of flexibility that can be provided. Human workers are able to make quick decisions and adapt to unexpected changes, whereas automation does not always account for the unforeseen. Last-minute order changes and changes to delivery schedules only scratch the surface when dealing with short-notice issues, which, at times, cannot be instantly amended within the coding of automated processes. Cost benefits of manual processes include less expenditure on technology and equipment that would, otherwise, be necessary for automated processes. It, additionally, serves as a great opportunity for job creation for individuals who may not have the skills or education required for more technical roles within the logistics industry. Ultimately, manual processes provide a level of personalization and customization that in some cases cannot be replicated by machines and computers.
The counterarguments to manual processes, however, highlight the limitations surrounding manpower. Manual processes do not always have the same accuracy and precision that can be achieved through automation, which can sometimes result in issues linked to quality control, as well as possible safety concerns. Additionally, decision-making processes, most often spear-headed by manual labor efforts, usually rely on the capability to analyze data and detect patterns and trends. A notable example of this is demand forecasting. Manual labor, therefore, presents a constraint when referring to the amount of data that can be analyzed and the insights generated thereof. Furthermore, manual processes do not always lend themselves to a scalable model, as physical labor can often result in a struggle to keep up with demands during periods of growth or high-volume operations.
Automation, as an alternative, provides a solution to many of the potential costs and drawbacks of relying solely on manual processes in the logistics industry. A large expectation of the implementation of automation is the initial, big-budget investment it calls for. Some other deterrents may include stifled flexibility during high-pressure and unforeseen circumstances, as well as a lack of personalization and customization. While the above may seem daunting for such a risk-averse industry, the prospective advantages automated technology can bring vastly outweigh the negatives. Improving upon situations that are susceptible to human-error, automation can refine speed, accuracy and productivity. Automation allows for increased levels of consistency and quality within the supply chain and logistics processes by lessening the time it takes to process and fulfil orders. The culmination of these factors, in effect, can result in huge savings that would initially have been spent on unexpected mistakes brought about by manual processes.
The advantages of implementing automation into a supply chain and logistics company can be summarized into one, significant point: the saving of time and money. In the supply chain industry, one of the most important tasks of planning and management is demand forecasting. Automation, state-of-the-art technology, and artificial intelligence combined together have revolutionized demand forecasting routines, reducing up to 80% of prediction errors within its first 9-12 months of implementation.
Algorithmic technology provides stronger accuracy in its readings, especially when dealing with larger datasets. It can, thus, detect patterns and correlations from complex scenarios. Additionally, automated technology completes tasks such as budgeting and sales forecasting in mere minutes, instead of the usual – days, or even weeks. Smart, automated forecasting can simply be described in a few words, ‘Better, and more often.’ Decision-making, again, is made more efficient with automation through order management and purchasing routines. Automation technology is able to speed up the order management workflow by a factor of 6, sifting through thousands of items to be considered for purchasing, from many different suppliers. Speed is not the only advantage when dealing with automated order planning, as real-time visibility provided by automated inventory optimization offers itself as a driving-force behind the decision-making of product replenishment investment. Not only does an automated PO management system increase workflow at a rate that is 6 times faster than before, it can also reduce overstock up to 15%.
Misconceptions and the truth
A common misconception facing automation is that once it is introduced, the company faces significant job loss. Historically, this has occurred, however, there has not always been a great enough focus placed on the benefits automation brings to the workforce and their workplace. Through observation and experience with SMEs, automation can be firmly concluded as a business need, as well as a mandatory step towards achieving better cost management and optimisation. The ease-of-work results linked to automation implementation for supply chain and logistics workers are impressive and lengthy. With increased effectiveness of processes brought about through the implementation of automated technology, work is made more enjoyable for employees involved in manual tasks run by automated processes. The workforce’s jobs, in turn, are also made more necessary within their company. Benefits that can be experienced as a result of automation implementation include, but are not limited to: sustainable company growth, increased job satisfaction, and increased quality of work. In such a scenario, where automation improves processes as well as worker satisfaction, a third option comes into play: the hybrid or amalgamated approach of both options.
Manual and automated processes in supply chain and logistics are not mutually exclusive. On the contrary, automation of processes achieved with decision support tools (automatically generating predictions, inventory status reports and purchasing suggestions) can be leveraged best when included in collaborative processes. Examples of these include forecasting and budgeting – where human contributions are necessary in order to offer supervision and last-minute refinements, and the flow of standard operations is not only maintained, but exceeded and made more efficient by the new technology.
Automated technology also lends itself as an opportunity to improve already-existing manual processes, without removing the reliance upon human labor. Barcoding and RFID tagging is an example of this. Automated systems use barcode scanners and RFID readers to quickly and accurately capture data, and human workers remain necessary for the implementation and maintenance of these systems. Additionally, if any issues and errors should arise, manual labor offers the benefits of timely resolution that cannot always be brought about through automation. Automated technology reduces the risk of human-error and allows for large volumes of data to be analyzed at an incredible pace.
The benefits of implementing both automation and manual processes into supply chain and logistics include more informed decision-making, timeous error-resolution and accurate operations. Ultimately, the individual needs and goals of each business will inform the decision to use manual, automated or manual and automated processes. Important considerations include cost, flexibility, customization, efficiency and accuracy. Making this decision can seem like a daunting feat with no concrete point of execution— choose the option that is characterized most by the afore-mentioned values that fit your company.