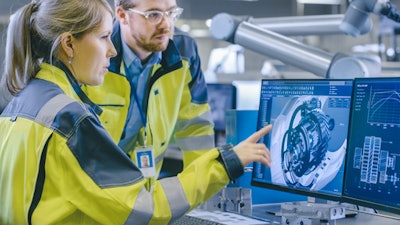
In March 2020, the U.S. unemployment rate spiked to 15% as the first wave of the Coronavirus disease (COVID-19) caused many businesses to take drastic measures — laying off workers while they temporarily or permanently closed — to survive the turbulent times ahead. According to the August 2021 jobs report, U.S. unemployment has fallen and is now hovering around 5.4%, but it is still higher than the 3.5% level pre-pandemic. Manufacturing jobs are still down 433,000 jobs from their February 2020 pre-pandemic peak level. Many people, particularly in regions of the United States where the Delta Variant is raging, are still nervous to return to work and be in close contact with other people.
This situation is exacerbating an already-challenging scenario for manufacturers -- skilled, available assembly line workers are, and have been for years, in short supply. Instead of employees looking for work, employers are looking for workers. These worker shortages play a major role in hampering a manufacturer’s ability to predictably produce quality goods against orders received. With more than two-thirds of assembly jobs still performed by humans, staffing problems — not to mention other situations that have been worsened by the coronavirus, like inadequate training and absenteeism — have a huge ripple effect up and down the supply chain. To address the deficits, companies are increasing their recruiting efforts and offering richer incentives to potential new hires, but in a small pool of available talent, even the most proactive of hiring companies will need technology to maintain a high level of productivity.
The common belief is that productivity and robustness against this type of fluctuation can be achieved by automation, but in several situations, automation is not an option due to the nature of the task. In this case, training and a different kind of automation — automation of data creation using artificial intelligence (AI) — will empower workers to make better and quicker decisions. Thereby improving the effectiveness of each person and compensating for the loss of people.
AI is the key to data in manufacturing
When considering AI’s role in any workplace, but especially in manufacturing, there is a pervasive idea that it will be used to displace people from the workforce (think robots replacing people.) But as with any tool, it depends on how it is meant to be used. And, when a tool is wielded correctly, it has the ability to raise a person’s abilities. As a tool, AI has the ability to augment and, therefore, engender greater productivity from existing workers.
Let’s consider the specific case of production data from manual assembly lines. Traditionally sparsely available because data capture techniques haven’t changed since the 20th century, this production data has the potential to be the lifeblood of any modern manufacturer. It can be used in multiple facets of the business, including training, quality, productivity and process improvements. After all, if you can’t measure, you can’t improve.
Today’s digital tools not only make continuous improvement easier, but they can also create entirely new possibilities of what can be measured, opening up a scale and speed of business improvement that has never been possible before. One such tool is the newest generation of AI and computer vision that uses video streams, not single images, to create this transformative data set.
Click here to hear more about machine learning in the supply chain:
AI in motion on the factory floor
Video-based AI and computer vision are now capable of discerning process steps being executed by line associates on the plant floor with a high degree of accuracy, despite various lighting conditions, working styles, etc. This tool creates massive amounts of manual assembly data from factories — more than has ever previously existed. Entirely new data sets can be created that manufacturing has never had the ability to perceive before. This data can be used to find bottlenecks, anomalies and other areas for attention that would be nearly impossible without the right tools and data integrations. User interfaces that highlight critical areas and video-backed data points make uncovering, understanding and acting on relevant data easy.
To illustrate, consider the problem identification, solution creation and the problem resolution process anchored, possibly by lean tools, including A3 reports and PDCA. When a manufacturer finds an escaped defect leaving the assembly line, data gathered through video analytics can be used within the A3 framework to better identify the root cause. As it often turns out, it is the process, not the person, who is most often the cause of issues. So, training the team is often a common solution. Here, the same AI tools can then be used to retrain that worker by providing them feedback even as they execute their jobs.
Not unlike reviewing video of your golf swing helping you improve your game, this process of using visual data to train the line associates to identify more efficient actions or processes can then be scaled up and shared across the entire company by updating the current version of standardized work. This data can be used to upskill other workers, which can be done through video analytics, making training easier, faster and broader. Who would not want to have a full-time and permanent takumi on staff?
Perhaps more importantly, by aggregating third-party data with data from this computer vision system, it becomes possible to eliminate the bias problem from the past and treat people more equitably.
Empowering employees for the factory of tomorrow
Interestingly and relatively uniquely, both the overall business and the individual worker benefit from the use of this type of system. The pandemic was a wakeup call not only for businesses, but also for employees to reevaluate their current roles and to examine what they wanted out of a job and a career. Employers need to anticipate those employee needs. Factories that have implemented AI and data analytics tools, particularly as a part of an employee’s everyday work, are appealing because they introduce a modern view of craftsmanship back into manufacturing.
In the end, it’s all about people. The No. 1 factor that will separate supply chain laggards from supply chain leaders is how well they are able to optimize their existing workforce, even in the face of challenges like COVID-19. Supply chain leaders know they are working in an inelastic labor market with an ever-shifting elastic demand, as customer wants and needs are amplified through digital buying practices, all sandwiched between the uncertain world that exists in the COVID-19 era. This makes a plant's ability to pivot in its manufacturing focus crucial to supply chain resilience. This can only be done by digitally transforming parts of the supply chain and manufacturing using AI to create this long absent data, and then, using it to draw the right insights, plan the solution and confirm execution against this plan.