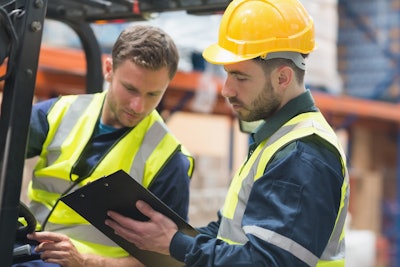
The labor challenge is a consistent, growing problem. While warehousing is characterized by growing overall competitive intensity and a whole host of rising customer demands, labor challenges reign supreme as the most profound challenge dogging the industry. According to the MHI Annual Industry Report, more than half of companies surveyed rated hiring and retaining qualified workers as “extremely or very challenging.”
While the issue is not a new one, it is growing. The U.S. Bureau of Labor Statistics reports turnover in warehousing has grown from 40% to nearly 60% over a five-year period. These difficulties are not showing signs of abating in the near future either. Due to broad demographic shifts, the U.S. workforce is actually shrinking. The civilian labor force participation rate, a measure of the workforce, has been sliding downwards for the last 20 years, according to the BLS, due in part to lower participation for workers in their prime years, between the ages of 25-54. Add to that the fact that Baby Boomers, the second largest age group, are reaching retirement age at a rate of about 10,000 per day, and that by 2030, all will be at least age 65.
Adapting to persistent labor challenges
In recent years, and even more so with the pandemic, warehouses have been increasingly reliant on temporary and temp-to-hire workers to maintain business continuity. Operations are using higher wages or incentives to attract more workers to meet short-term demands quickly while maintaining flexibility in headcount and costs. But, as the name would suggest, relying on temporary and temp-to-hire workers is not a sustainable strategy for long-term success. Warehousing Education and Research Council’ (WERC's) annual DC Measures Report indicates that best-in-class operations have 0% of their workforce as part-time employees.
Automation is a solution to help warehouses bridge the gap between productivity targets and a limited labor pool and even goes a step further. By delegating repetitive tasks to automation, operations not only plug gaps in their workforce, but can concentrate their employees on higher-value tasks, keeping them more engaged and less likely to look for work elsewhere.
But, as competition for a more limited, turnover-prone labor pool persists, warehouse managers must take action, equipping employees with tools to maximize productivity and bolster retention.
Step 1: Identifying the best tasks for operators
While average turnover in the industry sits at nearly 60%, turnover can fluctuate wildly between operations. The WERC DC measures survey identifies “best-in-class” warehouses as having less than 4.7% annual turnover, while operations with turnover greater than 40% have a “major opportunity.” That opportunity has significant ramifications for an operation’s bottom line due to the cost of turnover – hiring and training just one replacement can cost thousands.
Robotics can automate repetitive tasks, like load transportation and even retrieving or depositing loads from elevated conveyor lines and storage locations. Augmenting a workforce with automation relieves employees of mundane, repetitive tasks, freeing them to focus on more engaging responsibilities. That shift is meaningful for retaining top talent; according to a Gallup study, organizations with better employee engagement achieve higher performance, including substantially better retention and productivity.
Step 2: Addressing operator priorities
Both to minimize the threat of turnover and encourage high performance, it is crucial that managers listen to what employees have to say and address what is important to them. At a general level, the Society for Human Resource Management identifies several factors that can help retain quality employees, including:
- Opportunities to use skills and abilities at work
- Trust and clear communication between employees and management
- Compensation/pay
However, other factors can also drive employees away:
- Lack of feedback about performance
- Unclear expectations
- Failure to set employees up for success and provide a framework in which they can succeed
What do these insights mean for warehouse workers? Telemetry, another warehouse technology, can help operations cultivate employee trust, clear expectations and a framework for success.
Telemetry systems offer a broad range of insights about lift truck usage and performance, some of which can be leveraged as effective tools for data-driven performance tracking. By assigning utilization and impact data to individual operators, warehouses add an extra layer of accountability for ineffective operators, while incentivizing high-performing employees, yielding more informed labor management decisions. Employees can feel more confident that their performance-based incentives are just that – performance-based – not swayed by individual opinions or perceived favoritism.
Step 3: The importance of ergonomics
The level of concern among industry leaders about today’s labor challenges goes to show just how acutely labor influences overall warehouse performance. Businesses depend on the speed, efficiency and accuracy of their operators to keep mission-critical workflows moving on target.
Because warehouse labor is subject to such intense churn, businesses must make the best of available labor by setting operators up for high performance. Empowering operators to thrive at work can also give them reason to stay with a particular employer, helping to counter poaching efforts.
Ergonomics and other equipment characteristics have a meaningful impact not only on operator comfort, but productivity, too. Fatigued workers can lose 5.6 hours of productive time per week due to reduced cognitive performance and difficulty concentrating, leading to more time necessary to complete tasks. Ergonomic, operator-centric equipment can help fight fatigue with:
- Cushions and suspended floor systems can significantly reduce shocks and vibrations transmitted to the operator.
- Generous space and intuitive controls can allow operators to move about and find the most comfortable operating position.
- Designs that prioritize visibility, which can help prevent operators from craning their necks and assuming uncomfortable postures.
Keeping operators fresher and more focused, combined with subtle features designed to boost performance can lead to productivity gains that might seem small at first, but add up quickly, especially in today’s high-velocity warehouses. For example, faster lift and lower speeds on a reach truck can shave seconds off each cycle. Over time, just one additional pallet move per hour can produce 7% greater productivity, or the equivalent of 17 free days of labor over the course of a year. Similarly, one-touch controls on motorized pallet trucks can help operators expedite movement and precise truck placement between pick locations to help shave seconds off of each pick.
Setting new labor performance standards
Achieving best-in-class warehouse performance requires operations to understand labor as an important part of their total warehouse strategy. Just as managers might re-rack a facility to achieve a more efficient storage process or greater capacity, operations must consider what conditions can be optimized to improve labor performance. The solution may involve a combination of strategies, whether that’s moving cumbersome, time-consuming tasks away from operators, using technology to manage performance or equipping employees with tools that better support comfort and productivity. Actively incorporating operator input will help warehouses determine the best-fit set of tools and frameworks to maximize labor productivity and retention, while controlling costs.