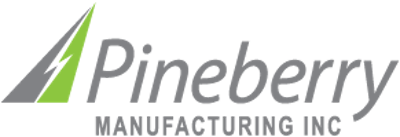
A large international pharmaceutical company contacted Pineberry Manufacturing Inc. Toronto, Ontario, Canada. The Pharmaceutical company desperately needed to serialize its products, support traceability throughout its supply chain and aggregate erect cartons, all to comply with the USA FDA Drug Supply Chain Security Act (DSCSA), the EU Falsified Medicines Directive (FMD), and other market requirements worldwide. The problem: Limited space necessitated a compact system to print and verify traceability serialized codes on erect cartons and aggregate them into batches of 12.
Aggregation impacts serialization projects on the packaging lines throughout manufacturers operations and the overall supply chain. Aggregation provides any company involved in pharmaceutical packing with the ability to serialize, which will lend itself to ease-of-mind for pharmaceutical companies. The biggest reason for companies to possess proper serialization is to prevent the influx of counterfeit drugs into the legitimate community.
A few weeks later, the CartonTrac Serialization and Aggregation System was introduced to the pharmaceutical industry and packing supply chain markets. As erect cartons come down the customer’s conveyor line and onto the Pineberry CartonTrac Serialization and Aggregation System high-quality print serialization is applied to each of the pharmaceutical cartons. A camera vision system scans each carton to verify all the required printed data has been placed, applied correctly, and is easily readable. If there’s a print issue, the pneumatic reject system blows any poorly packed cartons off the production line.
Once individual serialization is achieved, the individual cartons move to the front of a gantry robot that gently grabs cartons with its EOAT (end-of-arm-tool) gripper and stacks them creating tidy bundles, three rows of four. The high-speed gantry system can move at speeds of up to eight meters per second. The servo motors help the robotic system not only be very fast, but steady and very accurate, with the flexibility to modify the stacking patterns as required. After the cartons have been stacked, the bundle of serialized products is transferred through an automatic banding system which swiftly bundles the cartons into a single batch bound by a breadth of clear plastic wrap. A second camera vision system takes a picture of the batch, recording all individual serialization pack codes applied previously. The newly-formed pack then has an additional label blown onto the clear plastic banding wrap with the label containing a single QR code that combines all of the data from each of the individual packs of product. The pack then exits the Pineberry CartonTrac Serialization and Aggregation System to await further packing into a master carton where another label is added containing data of all its contents. Further downstream, when the master carton is palletized with other such cartons, another label can be added for complete identification of what it contains.
“As the cartons are combined, the serial number of the aggregated unit (parent) is associated with the multiple serial numbers of the individual cartons (child) contained within it, thus builds a parent-child relationship as products move through the packaging stages of the pharmaceutical supply chain. It’s a full track-and-trace solution that leverages aggregation and helps to improve the customer’s inventory management performance,” states Mr. McCharles. “For example, if you need to determine a batches contents but do not want to open the case, you can now scan the QR code on the outside of the case to get the serial number, and then using the aggregation parent-child relationship, you can determine the identity of all the contents. This is one of the reasons that aggregation can ease the material handling aspects of serialized projects in a warehouse environment, while maintaining the safety of consumers and ease-of-mind for pharmaceutical companies,” continues Mr. McCharles.
Manufacturers, wholesale distributors, repackagers and pharmaceutical supply chains inherit the most benefits facing significant packaging line upgrades to meet the current and emerging regulations compliant with the USA FDA Drug Supply Chain Security Act (DSCSA) and the EU Falsified Medicines Directive (FMD). Putting aggregation in place offers operational benefits, like inventory management, and prevents the invasion of counterfeit drugs into many global communities. With serialization, wholesalers are able to identify inventory down to a specific unit and track it internally. With aggregation, they could do that for both opened and sealed cases as well. It greatly simplifies cycle counting, which wholesalers periodically do to check their physical inventory against what their system thinks they have. Aggregation allows them to scan just the sealed case and instantly know the identities of all the individual units. The CartonTrac Serialization and Aggregation System provides a practical and cost-effective way for pharmaceutical companies to ensure their products conform to current and upcoming global track and trace efforts.