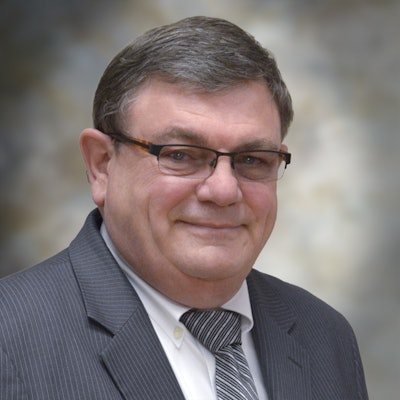
The predictions for 2015 are optimistic for manufacturing. The International Monetary Fund (IMF) expects global economic growth of 3.3 to 3.8 percent and U.S. economic growth of 2.2 to 3.1percent and anticipates the manufacturing sector will grow by 3 to 4 percent. So why is manufacturing management losing sleep?
While the outlook is good for the economy, it is not a promising outlook for manufacturers looking to staff up for the anticipated increase in manufacturing. This is not a new issue. Many CEOs have reported that they are unable to find and recruit the talent that they need to keep operations running, especially if they grow. When I met with a CEO and a president in the packaging industry recently, they were experiencing significant business growth, which was now taxing the capacity of the plant.
The company president said, “Our customers are promising more growth and volume and they expect the company to invest in a new facility” in a different region of the country. In the conversation, he indicated an unwillingness to invest in a new facility because he fears there is limited talent to run the facility. Another CEO in the printing industry located in a remote area of the Midwest simply could not find the right skills locally and found it extremely difficult to recruit the right people at any price, since there is reluctance to relocate to a remote location. There is no doubt the skillset shortage in the manufacturing sector can compromise the future competitiveness of manufacturers in the United States.
Deloitte and the Manufacturing Institute conducted a skills gap study, The skills gap in U.S. manufacturing 2015 and beyond, and the findings are astonishing. They report that the skills gap is widening. “Nearly 3.5 million jobs need to be filled and the skills gap is expected to result in 2 million of those jobs going unfilled.” This is a talent crisis. As the Baby Boomers leave the workforce, replacement workers do not find the manufacturing sector attractive and manufacturing plants are typically not located in the hot spots that attract the Millennials. As we look at the jobs to be filled, they have changed significantly and manufacturing facilities become more automated and move to lights-out factories. Due to advances in technology, manufacturers are looking for blue collar tech workers who can run computers, robotics, and automated machines. The new jobs pay 3 to 4 times the minimum wage, according to a Deloitte analysis based on data from the U.S. Bureau of Labor Statistics and a Gallop Survey. It is a well-known fact that every job in manufacturing creates 2.5 jobs in local goods and services. For every $1 invested in manufacturing, another $1.37 in additional value is created in other sectors.
The Manufacturing Institute reports that the hardest jobs to fill are those that have the biggest impact on performance. “Shortages in skilled production jobs-machinists, operators, craft workers, distributors, technicians and more are taking a toll on the manufacturers ability to expand operations, drive innovation and improve productivity.”
While the manufacturing segment of the market recognizes the need for talent, it is relying on word of mouth, personal recommendations and other outdated methods of recruitment. The five keys to success for talent management in manufacturing are:
- Document the talent needs now and in the future. Identify the key players and create active succession plans.
- Work with local community colleges to create programs that can train, motivate and build specific talent for your company.
- Participate in high school career days to motivate people to make manufacturing a rewarding career choice.
- Develop a college intern recruiting program to connect with engineering and technical students, offering them the opportunity to have real life experience in manufacturing—sort of a two-way try-and-buy.
- Build career path plans and make your company a fun and attractive place to work with incentives for productivity, innovation and stability for years to come.
Jay Timmons, President of the National Association of Manufacturers, explains “Growing a talented workforce helps ensure manufacturing will continue to be the bedrock of our economy and competitiveness.” What this all means to Supply Chain Professionals is, since we have experienced a series of natural disasters causing supply chain risk over the past several years, our strategy has changed to a model where we achieve best-landed cost. With slow steaming ships, increased fuel costs, and other mitigating factors, we have been moving from low cost country sourcing to reshoring and manufacturing close to the point of use. This means a supply chain talent strategy must also be implemented to assure business success.
To remain an industrial leader, U.S. manufacturers must find a solution to the manufacturing talent crisis.