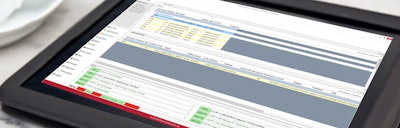
Over the past year, the shortage of truck drivers not only made headlines, but is also forcing warehouses to rethink their order fulfillment processes. This shortage—which could rise to 175,000 by 2024, according to the American Transportation Associations (ATA)—is compromising the reliability of fleets. This means that, if a truck does not arrive on schedule, warehouses that stage orders hours in advance often find those goods sitting, taking up valuable space and preventing their entire operation from flowing smoothly.
As a result, many warehouses are beginning to implement just-in-time (JIT) order fulfillment strategies, in which they begin the order fulfillment process as the truck arrives at their facility for order pickup. While warehouse automation technology in the form of automated storage and retrieval systems (AS/RS) is helping to enable these strategies, it is the software applications behind the automation that are often the driving force.
Traditionally, warehousing organizations used two separate applications within their operations—a warehouse management system (WMS) and a warehouse control system (WCS). The WMS manages the workflow of the operation, while the WCS executes the workflow utilizing the automation. However, using both systems effectively can require complex integrations. And, if they are not properly integrated, companies run the risk of inventory inaccuracies, misrouted products and confusing workflows, all which hinder the order fulfillment process.
In order to best optimize the order fulfillment process and easily implement JIT strategies, warehouses should consider a warehouse execution system (WES), which combines the functionality of both a WMS and WCS in a single application. Within one system, a WES can direct inventory management, order management, billing, workflow, and the direction of material handling equipment and personnel throughout a facility.
Enabling JIT Order Fulfillment with a WES
The combination of a WES and automation allows warehouses to quickly and efficiently retrieve products right when they are needed. Staging orders well ahead of time becomes a practice of the past. Using the software, organizations can more easily identify the product that is necessary to fulfill a particular order and then direct the workflow needed to fulfill the order in a timely fashion.
How does it work? With a WES, the order fulfillment process really starts when the truck appointment is made or when the truck arrives. When users check in the truck, they assign the order and a specific loading location for that vehicle using the WES software. Once the truck pulls into the loading position—regardless of arrival time—operators use the WES system to initiate the order fulfillment process. Here, the software directs the material handling equipment (e.g. a storage/retrieval machine) and/or material handling personnel to pick and dynamically deliver the product for the order to the appropriate area for loading. When manual picking processes are also involved, a WES can marry these portions of the orders with those picked by automation and direct them to the appropriate dock for loading. This cuts down on the number of wasted steps in the manual materials handling process.
From a quality standpoint, WES software plays a key role in verifying that the product ordered is the product that is actually loaded and shipped. As the vehicle is loaded, the software automatically performs real-time verification checks to ensure that the correct product, and quantity of that product, is placed onto the correct vehicle. This is especially useful when there are many operators handling a high volume or wide variety of orders. Using barcode or radio frequency identification (RFID) scanning systems interfaced with the WES, the operator can simply scan a tag indicating the loading location, then scan a tag on the product or pallet, and automatically validate that the correct goods are going onto the correct truck.
Operators can later perform pre-shipment activities, such as generating a bill of lading, manifests and other necessary paperwork with a WES. Also, the WES can interact with transportation systems so that carriers can track the loads in their systems, as well as loading times. This helps warehouses uphold service-level agreements with their carriers, thereby preventing retaining the trucks too long, while also allowing companies to prioritize tasks so they can fill loads in the least amount of time possible.
It is important to note that a WES is also effective in a non-automated or slightly modified facility—an AS/RS is not required to utilize a WES. When manual picking processes are involved, a WES helps users to more efficiently manage the order fulfillment process by allowing them to perform pre-allocation checks, thus allowing them to determine if enough of the right product is available to fulfill the requested order quantities, and aids the user in the management of their appointments and vehicle-scheduling activities. Once the truck arrives for loading, the WES still allows operators to prioritize and manage orders, optimizing the entire process.
As the trucking shortage continues to escalate over the next several years, warehousing organizations may find some solace in a WES. Whether or not it is coupled with automation technology, a WES ensures that products keep flowing throughout the facility, frees up space and supports JIT order fulfillment strategies.