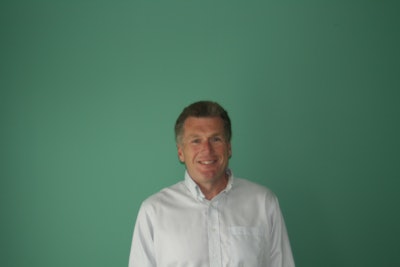
Despite the advances made in distribution center (DC) operations over the years, many are not fully automated. The DC has evolved to meet the faster pace of retail and to adapt to more flexible fulfillment options.
In fact, some areas of the DC are still labor intensive, and as a result, error prone. Below, we review three challenging tasks and how RFID can be a major part of the solution.
Pick to Light/Pick & Pack
While it’s true that some distribution centers have become highly automated, the reality is that most still continue to have manual processes. A prime example is picking orders. Years back, you printed out the order, ran down an aisle, found the goods, brought items back to your area, packed it up and shipped it out. Beyond this being time consuming, there are opportunities for errors to creep in at every point. Yet, many manual processes still remain.
Add to this the challenges imposed by rush shipments and an increasing number of omni-channel orders — which must be picked at the individual level and then shipped directly to customers. It’s easy to see why problems persist.
This situation exists despite the fact that pickers in DCs are evaluated on accuracy and speed. When they get it wrong, they hear about it from managers. At month’s end, they may be overwhelmed with more orders and many of them rush by. There may be pickers whose bleary eyes start to see all item numbers as the same. That’s when errors really start to creep up. It’s to their credit that they achieve the accuracies they do.
Solutions:
Managing shipment accuracy by exception isn’t much of a solution. By its very nature, shipping management can’t put a major dent in inaccuracies.
Even some automated solutions, such as lighting systems, don’t completely eliminate the scavenger hunt.
But RFID does. It enables DC staff to manage order variability with process automation. Using RFID, pickers can quickly find items, reserve and confirm them. They can even pick multiple orders at once. In instances where consumers are expecting a good fit and finish, RFID can help pickers automate shipping labels and even choose the right boxes for efficient packaging.
Inbound Receiving to DCs
While some errors are inherent in the picking process, others still originate at the factory. Any of those errors are likely to propagate downstream or end up in limbo if identified in the DC and put in quarantine.
Solutions:
To address this, new hardware systems can be connected with standard conveyor systems and verify that items within each bulk shipment are 100 percent accurate. Any errors can be instantly identified and triaged before the shipment leaves DCs. This allows DCs to make necessary corrections and avoid added cost and time. Valid shipments generate automatic advanced shipping notifications and are sent for delivery.
In addition, many retailers are ramping up their RFID tagging at the source. In this manner, they can verify the inbound ASN against the physical contents of the shipment to focus staff on exception handling versus ordinary day-to-day operations. If it’s not practical at the source, bulk encoding can take place at the DC, using tunnels described above or tables to ensure the correct inventory allocation for items.
Shipments to Stores
Stores are the last stop in the supply chain network and suffer the impact of all the errors that were made earlier. An Auburn University study found nearly six percent of ASNs are wrong, meaning there are inventory errors before merchandise reaches the store. This impacts on-shelf availability, omni-channel fulfillment and customer satisfaction.
Solutions
This is where automated verification of merchandise via technology such as RFID tunnels pays dividends. Whether pick and pack, or boxes simply passing through the DC, RFID can identify errors before they leave. When trucks unload at the backdoor, RFID allows store associates to know immediately upon its receipt what is in a box and compare it to the shipping notice.
Additional savings can be realized as well. A University of Arkansas study demonstrated that charge backs cost about one-half to one percent of sales. Increased accuracy of shipments reduces or eliminates those chargebacks.
A final benefit of RFID is that by tracking missing merchandise throughout the supply chain. Retailers can determine where in the process those items were lost or stolen, making theft less attractive and recovery more possible.
While DCs value accuracy and inventory management, they are often challenged by today’s retail trends. The good news is that RFID can drive many efficiencies, which can be measured outright. By driving down shrink and increasing productivity using RFID, our experience has shown that you can identify and measure KPIs as well. And as this technology becomes even more pervasive, we see the day when retailers demand the kind of accuracy that they know RFID already provides.