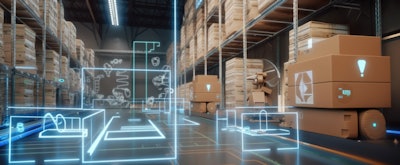
As consumers and retailers continue to navigate the challenges associated with an uncertain economy, distribution centers must still find personnel to fill labor gaps. Inventory still needs to be shipped, and fast, but without proper staffing and limited knowledge of package quality as they pass through warehouses, companies are stuck between a rock and a hard place. Additionally, logistics organizations must grapple with package volume increases and faster shipping times for customers who expect next or same-day delivery.
While automation technologies have gained momentum over the past several years, including the rise of robotic systems that are capable of moving and sorting inventory, warehouse visibility has been largely excluded from the conversation.
Immense amounts of data are going unutilized in distribution centers. As a result, warehouse operators are in the dark when it comes to the condition of products and the health of sorting equipment. This is a major problem, as failure to meet product quality assurance requirements can negatively affect the bottom lines of logistics companies, resulting in costly chargebacks. Not only that, but shipping times suffer when warehouse personnel need to troubleshoot issues with packages, since valuable time is expended trying to locate the source of a problem.
Thankfully, there are technologies available to the market that enable warehouse visibility, allowing logistics companies to understand the location and condition of packages at all times.
By harnessing the power of artificial intelligence (AI), image recognition and additional technologies, distribution centers can gain full package visibility to achieve greater automation.
1. Real-Time Location Systems
One method for enhancing warehouse visibility is to employ the use of a real-time location system (RTLS) or radio-frequency identification (RFID). Both options have the ability to track packages throughout their distribution lifecycles, although they are nuanced in their operations.
It should be noted that RTLS is not a designated technology, as it refers to any system that can determine the location of an item. This method is often used within the healthcare industry, but can also be applied to provide greater warehouse visibility.
Every RTLS system is composed of the same parts: a transponder, a receiver and data interpretation software. In order to track packages, a transponder is attached to an item and information about its location is read by hardware receivers placed throughout distribution centers. From there, software interprets the data that has been collected.
The range that RTLS systems are able to read depends on the technology being used. While some make use of GPS to track products globally, others simply share package locations within a specified zone.
2. Radio-Frequency Identification
As its name implies, RFID makes use of radio waves to share data about a package's location between a tag and a reader. These tags, frequently made up of an antenna and a chip, are attached to a package to track its movements. While the antenna receives data, the chip stores it, providing warehouse operators with a product's journey history.
Similar to RTLS technology, RFID shares information when it encounters reader technology that activates the tag attached to a package. The data transfer happens in real-time, providing warehouse personnel with important information that can potentially improve overall supply chain efficiency. Additionally, RFID technology can be easily integrated with enterprise resource planning or warehouse management systems.
Despite its usefulness, the technology does have its drawbacks. RFID technology captures immense amounts of data, but it lacks the ability to interpret it. As a result, warehouse operators are left with an overwhelming amount of information that can be difficult to organize in a meaningful way. Additionally, the accuracy of RFID technology can vary, as tags must be attached carefully to be read correctly. Metal or dirt can hinder its ability to perform, making it a challenge to use across an entire supply chain operation.
3. AI and Image Recognition
It's no secret that logistics companies must ensure products meet specific quality assurance standards. Everything from a smudged barcode to damaged packaging could result in chargebacks that can impact financial returns. Problems with inventory must be identified at the source, but in order to do so, warehouse visibility tools are necessary.
Logistics organizations have used cameras at the tunnel and facility levels for many years to store pictures of packages and barcodes. The intent was to keep a record in the event of a dispute over accountability for packages that were damaged or delivered to the wrong recipient. But sorting through thousands upon thousands of pictures to identify problem packages can be challenging.
AI and image recognition software can mine photos of packages as they move through automated lines for evidence of potential damage to the product or to identify whether a large, non-standard product is a tire or a spool of wire cable. This information can be used to tighten up procedures within distribution centers or can be shared with vendors to help them comply with shipping policies to keep automated systems running smoothly. Rather than monetize mistakes through chargebacks, logistics companies can use AI and analytics to avoid mistakes in the first place. It is more cost-efficient to help merchandise vendors perform optimally than to seek maximum compliance penalties.
4. AI-Powered Supply Chain Analytics
A scalable vendor-agnostic software allows businesses to extract more meaning from data, effectively turning previously unusable or superfluous information into actionable insights. It represents the cutting edge of supply chain analytics, and promises to let companies scale the intelligence, experience and judgment of employees. While the technology will never fully replace human expertise, it will undoubtedly assist large supply chain operations in making better decisions.
End-to-end horizontal integration of data is increasingly important in the logistics realm as a way to continually improve automation within distribution centers. The job of these warehouse facilities is to make sure products reach their final destination as quickly as possible, whether it’s a home on the other side of the country, a store across town or a shelf in the warehouse next door. To do this in an automated way, hundreds of elements must work according to standardized processes, this includes conveyors, cameras, sensors, data capture software and the hardware it runs on, and the underlying networks and hardware. Additionally, the policies and procedures followed by distribution center personnel cannot be forgotten. When automated systems break down, diagnostic analytics can quickly identify the root cause and suggest fixes, whether the problem is a sorter in need of maintenance, a broken sensor or a worker who is not following procedures for how to correctly place products on a conveyor.
As automation technology becomes more prevalent in supply chain operations, it is important for logistics companies to consider how they will enhance product visibility in warehouses. Fortune favors the bold, and it will be those who implement visibility technologies, such as AI and image recognition, who will reap the benefits in years to come.