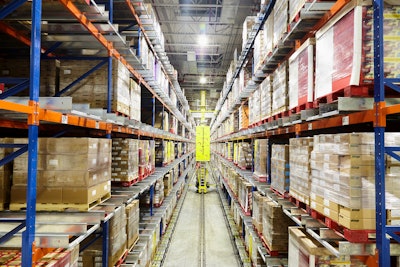
After an unpredictable year, no company or industry is a stranger to disruption. Whether it’s a global pandemic, a ship blocking a major trade route or a shortage of drivers, we’ve all grown accustomed to this unpredictability. But, when it comes to warehousing, logistics and the supply chain, a volatile environment can uproot even the most established organizations.
The many disruptions experienced over the past year highlighted the need for companies to flatten the ebbs and flows of their supply chain. The unexpected should be a part of any fulfillment strategy. Whatever that disruption might be, having the ability to quickly react and proactively adapt to move that product through the network is key for today’s companies.
Additionally, according to Business Insider, “2022 is expected to be the first trillion-dollar year for online sales.” And, consumers are demanding faster and more accurate deliveries than ever before. Scaling order fulfillment is a critical piece in adapting to these changing consumer demands and evolving market conditions.
How can your company go about implementing order fulfillment strategies to scale for business growth or lower than average volumes? A successful order fulfillment strategy begins with warehouse design. Utilizing warehouse automation and automated storage/retrieval systems (AS/RS) is at the center of increasing inventory accuracy, scaling for growth and meeting customer and consumer demands.
But first, what is AS/RS? AS/RS comprises five essential components:
1. A rack system to store product.
2. A crane/SRM (storage retrieval machine) that transports product to a storage location.
3. A load handling device/shuttle to move product from the crane to the rack location.
4. A conveyor system to move goods to and from the AS/RS and dock areas.
5. Warehouse management and material flow control software (WMS, WCS) to control, track and optimize all product movements.
These technologies all work together to automate the entire warehouse, which in turn, helps scale order fulfillment. AS/RS can do this in several ways:
1. Increasing inventory accuracy
When it comes to maintaining an accurate record of inventory, there’s no better way than to use the technology behind today’s leading automated warehouses. The conveyor system works to deliver product to the right pick-up location, from which the S/RM accurately and safely picks the product and places it in the designated storage location.
Automating this storage and retrieval process reduces the need for excess material handling, and therefore mitigates human error or damage to product. Not only does this improve productivity, but it also allows for greater accuracy throughout the order fulfillment journey—in product volume, location within the warehouse and timely distribution to the customer.
2. Optimizing warehouse efficiency
A one-size-fits-all solution to order fulfillment is simply not an efficient way to manage the storage and retrieval of products in and out of the warehouse. High-density AS/RS allows warehouses to hold more product in the same location, instead of products being spread out across a network of several warehouses. Whether you’re scaling for high or low order volumes, holding inventory within a single location gives you the ability to combine or customize processes as these changes occur. For example, a manufacturer’s product demand might increase dramatically during the holiday season but slow down heavily in the summertime. With a high-density, automated warehouse, they can stay within the same warehouse throughout the year, using only the space required, without needing to coordinate extra warehouse space or reconfigure manual storage and retrieval processes.
Plus, inventory consolidation allows quicker access to inventory, thus requiring less time to retrieve and deliver it when needed. Simply put, AS/RS allows for a more flexible, consistent and efficient warehouse.
3. Improving space utilization
Whether you’re looking to retrofit an AS/RS in an existing facility or install in a new building, an AS/RS is designed to save space. Most systems can go as high as 130 feet or as low as 20 feet, with leading AS/RS providers offering up to 20 pallets deep per rack. This means facilities with AS/RS can store 40% more pallets in the same building footprint as a conventional racked warehouse.
If you’re looking at building a new warehouse, implementing an AS/RS reduces the square footage needed for the facility, meaning lower building costs up front. For instance, if you own a frozen storage facility, this smaller footprint is a game changer for long-term energy use and cost, too. For those with an existing facility, an AS/RS is ideally suited to scale order fulfillment and growth because it can fit nearly double the amount of inventory in the same square footage, meaning no need to expand to another warehouse when conventional warehouse space runs out.
Click here to hear more about innovative warehousing ideas like micro-fulfillment:
4. Using data to transform order fulfillment
Today’s modern warehouses can have up to tens of thousands of SKUs, millions of delivery locations and a complex supply chain that can be nearly impossible to manage effectively without the right system to back it up.
With a plethora of warehouse software to choose from, the two typically considered are warehouse management systems (WMS) and warehouse control systems (WCS). Usually, the WMS manages the warehouse operations, including inventory tracking and lot management, while the WCS manages the operation of the automation.
A warehouse execution system (WES) marries the WCS and WMS functionality together—bringing order fulfillment into a single system. From pick path and order planning, to receiving and inventory tracking, WES is key in managing this complex information accurately and efficiently. Additionally, a WES has built-in order planning capabilities, which helps warehouse personnel determine inventory, logistics availability and order demand. A WES provides all of the tools needed to track your product and manage your inventory, manage and direct your equipment, and manage staff workload within a single application.
A state-of-the-art WES can create a more efficient, accurate and flexible warehouse. Coupled with AS/RS technology, businesses can have a competitive edge to accommodate customer needs and supply chain demands.
Staying proactive amid disruption
Scalability and order fulfillment really come down to the robustness and flexibility of software and technology within the warehouse. To manage the many unknown disruptions ahead, a high-density AS/RS and WES system are critical in maintaining a proactive business model. From labor shortages to fluctuating demand, there are many challenges ahead that will force companies to think differently. As we emerge and learn from the pandemic, it’s critical for businesses to implement efficient and creatives ways to scale order fulfillment before the next disruption hits.