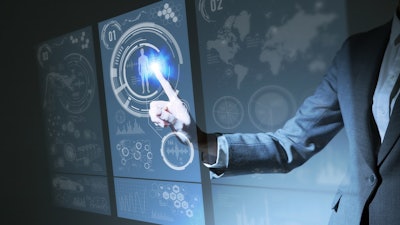
Consumers demand perfect supply chain performance, but industry leaders know that’s not realistic right now. They would just be happy if supply chains became more dependable. That’s why they are looking for solutions that can take efficiency to the next level, particularly within their own warehouses. Keeping up with shifting regulations, managing tight order turnarounds and maintaining low execution costs while optimizing every piece of the logistics puzzle are becoming more challenging with each new quarter, but they are all things that must be achieved. In fact, 79% of organizations with high-performing supply chains see greater revenue growth than the average growth within their industries. If a warehouse operator wants to reach above-average profitability, it must embrace technologies that make it easier to move faster and process more orders without making mistakes. In most cases, the solution lies in automation.
There are several ways to automate warehouse operations. Many industry leaders are increasingly considering intelligent automation solutions, such as collaborative robots (cobots), alongside prescriptive analytics and workforce management solutions powered by artificial intelligence (AI) and machine learning. However, there’s also a growing business case for industrial automation solutions – once considered too complex to be worthwhile in warehouses – now that machine vision systems and fixed industrial scanners have been reimagined and simplified.
Making the most of every minute
Time is precious, especially as more retailers offer more rapid delivery options.
That’s why industrial automation should be strongly considered by warehouse and distribution center operators right now. Whether achieved via machine vision or fixed industrial scanning technology, industrial automation solutions improve the accuracy and speed of both fulfillment and reverse logistics operations like no other technology available today. Every package must go through a visual inspection process for quality control purposes and each has a barcode automatically applied during the production or labeling process.
Rather than have workers manually scan the barcode of every item coming and going, warehouse operators can strategically place fixed 1D/2D scanners or smart cameras at dock doors, packing stations or along conveyance belts to automatically – and accurately – confirm their condition and location.
Fixed industrial scanners can verify a label was applied to the correct package and the barcode is readable, while the machine vision system can check the print quality and positioning of product and package labels to ensure compliance with shipping mandates. In fact, it’s the extreme discernment and simple pass/fail alerting capabilities of today’s intelligent scanning platforms that enable warehouse operators to reap multiple benefits from industrial automation.
Humans are subjective beings, so there’s potential for a lack of consistency when judging the quality of an item, package, or label. There’s also potential for delayed judgement, as it can take time for workers to compare back-end data against items in front of them. So, warehouse operators struggling to achieve consistency in quality control processes may find it easiest to automate inspections via industrial automation. If a package is sealed incorrectly or the label has a typo, they can feel confident it won’t get past the highly intelligent image-analysis system. Even better, they can sleep easy knowing industrial automation systems will be on the lookout for both isolated issues and patterns that can be easily overlooked by the human eye, especially in time-sensitive situations. When human intervention is needed, workers will know instantaneously so they can quickly resolve issues and processes can keep rolling.
Plus, the time, energy and resources saved through automated quality checking can be delegated to more valuable warehouse tasks. Automating the inspection process also enables warehouse operators to automate other processes upstream and downstream, including the label’s application and track and trace of work-in-process and goods on the move.
Recognizing the real payoff
Warehouse operators who may be concerned with the financial burden of integrating industrial automation technology into their workflows will be relieved to know that it can deliver substantial cost-saving benefits – sometimes quite quickly. When workers aren’t having to constantly stop the line to inspect – or reinspect – items, and when the status of items is automatically loaded into a digital record as it passes by a machine vision camera or fixed scanner, everything can move faster -- order fulfillments, inventory counts, even returns and replenishment. There are also fewer human errors and better decisions being made, which help improve the overall execution of supply chains day-to-day. Industrial automation technologies can scan a package or pallet and be able to determine where it needs to be staged or diverted to next to be delivered to the right place at the right time. If something is reported missing, there’s a trustworthy record of its last known whereabouts so it can be quickly recovered and moved along to the customer.
In fact, much of industrial automation’s value is derived from the widespread, real-time visibility it provides – visibility not necessarily possible with other intelligent automation or track-and-trace technologies.
For example, locationing is a major part of a warehouse worker’s job, and it can be a very tedious task at times, especially during times of high demand and wavering inventory quantities. But, industrial automation technology enables them to cut down the time spent searching for the right package, misplaced items, or even misprinted labels. It also reduces the need for workers to manually count anything: individual items, packages, or pallets. The cameras and scanners will track everything that passes by so workers can stay focused on keeping item movements on schedule without compromising quality – the real key to keeping customers happy and loyal.
In fact, automated barcode scans improve loading and unloading by helping teams see exactly what must go on the truck or what needs to be put away when planning their strategies. And, machine vision can reduce liabilities and improve accountability when damaged goods are reported. If a customer reports a damaged item upon arrival, warehouse operators can be certain they weren’t that way when packed – the proof is in the pictures.
No more hide and seek complexities – just simple solutions
Technology must be simple to deploy, manage and use in order to benefit warehouse operators. That’s why some have been hesitant to introduce industrial automation into the mix. There may be fewer perceived risks – or perhaps less of a presumed burden – by having people apply and inspect labels, check the quality of products and packages, and manually update inventory and order management systems. But, unlike the machine vision technologies used in production environments the past several decades, today’s industrial automation systems don’t require a lot of human management or even someone with an engineering skillset to use them. A warehouse worker could, hypothetically, be assigned to operate a machine vision system on day one and be a pro within hours.
In other words, automation can serve as a game-changing avenue for warehouse operators to save time and money while avoiding headaches and frustrated employees and customers. It can easily optimize accuracy, performance, and throughput like never before. When warehouse workers are supported by technology that allows them to bring their best efforts to other valuable tasks within the four walls, real results can unfold, and the high demands, tight deadlines and rapid fulfillments or returns won’t feel so overwhelming anymore. Customers can authentically enjoy their experience with businesses because the supply chain is being empowered by warehouse automation.