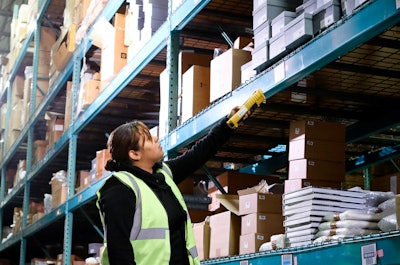
The rapid advance of cloud software in the last few years has allowed logistics and e-commerce managers to re-think their operations from the ground up, particularly when it comes to put-away. A best-of-breed warehouse management system (WMS) paired with handheld devices that tells employees exactly what to do and where to go provides complete certainty on how every item should be handled and stored – plus all-important instant visibility of inventory.
Smarter warehouses recognize that inventory management is continuous, rather than a process that ends the minute a shipment is received and put-away. Human error and manual/paper processes can both lead to inventory mishaps at multiple points, from goods-in to packing and shipping.
Without a keen focus on accuracy, inventory management mistakes result in lost productivity and reduced revenue. This means, customers receive the wrong item, generating unexpected returns, or you may not have the correct item in your warehouse to begin with, causing order processing delays.
The majority of inventory errors occur at two crucial checkpoints—receiving and put-away. Fulfillment centers face many potential pitfalls while receiving goods, but an agile and adaptable WMS will allow your labor to scan cases for failsafe identification and validation and support default units of measure for receiving. As an added benefit, tying receipts back to purchase orders will allow processes to be completed around over/under partial receiving.
Put-away errors can be even more of a headache, as they’re difficult to identify quickly, however barcode or RF scanner-driven WMS provides proper processes, greater visibility and validation to assist in locating inventory. It allows you to investigate what was put-away before and whether the inventory went to the same location of a previously put-away line.
Because your business needs to know what capital is tied up in inventory, an advanced WMS also includes cycle counting functionality, which will automatically generate the inventory counting tasks to be performed concurrently with other warehousing tasks, thus ensuring any auditing process takes place with maximum efficiency and minimum disruption to your operation.
As buying trends shift, the ability to alter inventory locations on the fly is critical for productivity too, while WMS productivity data will give a better idea of how to address labor and tracking inefficiencies. When you put away inventory without a verification scan, you’re more likely to make an error in data recording, which then must be rectified during the picking process.
Additionally, WMS software drives best practices for replenishment because an optimized system saves on costs and ultimately cuts down on the errors that can cause the entire inventory workflow to break down.
Whether it’s demand based, routine or top off, all three of these replenishment methods could be in use at the same time in the same facility, for example, supplying a retail outlet dealing with seasonal products. Without a robust method for planning, tracking and executing these strategies, there’s no telling how much productivity could be wasted.
The best solution is an easily implemented WMS with system-directed and scan-confirmed picking. This allows data on inventory levels and item destinations to be recorded in real time, and eliminates confusion when it comes to picking and packing for shipment. Using this reliable methodology, replenishment processes also become more efficient, as workers can more easily shift between lines to pick up slack if needed.
With a fit-for-purpose cloud WMS, you’ll gain a total solution that supports maximum inventory accuracy and visibility across the entire warehouse.
It also integrates seamlessly with other systems that might be in place like enterprise resource planning (ERP), delivering the capacity to manage dynamic locations and have a real-time handle on batch control.
Inventory management is the root of efficiency throughout your operation, and by prioritizing it across processes, you’ll find that errors will drop while productivity and revenue begin to rise.
Quality improvements present themselves in overall inventory validity; however where inventory attributes like receipt date, lot/batch code management and expiration date management drive warehousing requirements, an RF-directed WMS ensures dedicated and all-important management of the associated inventory.