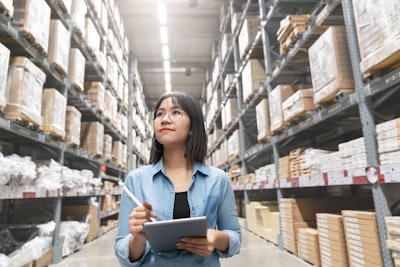
Businesses with excellent inventory management processes can fulfill orders faster, more accurately and more efficiently. With accurate inventory, companies don’t have to carry overstocks to handle shortages and backorders and out of stocks don’t exist. Inventory management practices that are exceptional reduce waste while creating satisfied customers.
Companies with poor inventory management processes have too much stock of the wrong items and too little of the fast movers, so out of stocks are rampant. They have low visibility into what is going on within their operation. For example, recently I ordered three appliances in a package deal from a home improvement chain. I received confirmation that all three items were in stock and would be delivered to my home on a specific date. The date arrived, and two of the items were delivered, but not the third.
In checking with the store, the item I’d ordered was out of stock at the location near my house but was available across town. The store would make sure that the appliance was delivered in a day or two. To make a long story short, the item was not in stock in the store across town, or any store nearby, because the company didn’t have a good handle on its inventory. I finally got the third item—weeks later—but I was not a happy customer.
Improving Inventory Management Processes
Companies need visibility into their inventory—a centralized view of all of their stock at each location—so that orders can be filled quickly. Inventory management and order management software exist that meet these criteria. But often this software is expensive. However, here are other things a company can do to improve its inventory management processes.
Some businesses think that increasing inventory turns will improve their inventory management processes. While this may generate more free cash flow, it often comes at a price (e.g., increased transaction costs, and more receiving, inspecting, put-away and the like.). The solution is to have the proper equipment and processes in place to turn inventory quicker and fulfill orders faster while reducing operational costs.
Accurate Inventory Counts
It is essential to have an accurate count of all your inventory and to know the location of that inventory. Receiving areas need to have an accurate count of inventory coming into the warehouse. The inventory then needs to be moved to the appropriate storage. Placing inventory is not guesswork. It needs to be correctly positioned for orders to be fulfilled properly and to eliminate out of stocks. If you need to increase order picking rates and improve space utilization, analyzing the movement of your inventory and slotting the position of inventory is a must.
Slotting is the process of allocating products (SKUs) to locations in a warehouse according to business rules and product characteristics. Effective slotting requires an understanding of a company’s business and goals, taking into account the physical size and aspects of the warehouse, current and future material handling equipment, SKU makeup, seasonal capacity changes, worker skill sets and customer service levels.
Slotting supports the movement of SKUs, whether fast or slow moving. It also improves throughput so that customer orders can be delivered on time. Effective slotting can also reduce product damage, improve worker productivity and speed fulfillment. Proper slotting not only provides much-needed space, but appropriately locates the fastest-moving items in the right location to speed fulfillment.
Proper Equipment for Better Inventory Management
To improve management of inventory, you need to look at the equipment you have in your warehouse. Large, massive warehouses often use expensive automation to move inventory from receiving to storage, and from storage through fulfillment. But other solutions exist that are less expensive and work just as well. These include carton flow, pallet flow, tilted shelving and the like.
Carton flow racks have a high order-picking rate of up to 150 picks an hour, but combined with a pick-to-light system that uses lights to show workers what items and how many to pick, you can increase pick rates by three-fold. Flow racks allow warehouses to store a mix of fast-moving and slow-moving items in the same rack—allowing pickers to quickly pick a variety of items from the same area. Tilted shelves help speed order picking too. With tilted trays or knuckled tracks that present products to pickers, allowing them to see what they are picking, you can improve order fulfillment times and eliminate errors.
Using a first in, first out (FIFO) system, you can improve your bottom line by cutting down on lost product due to spoilage or missed expiration dates. FIFO means newer products are stocked behind older merchandise. This system improves storage and picking because both operations can take place at the same time with loading occurring in the back and picking from the front.
Reduce Waste with Lean Processes
Excellent inventory management practices reduce waste while creating satisfied customers. These wastes include waste of time, space and travel. Look holistically at your entire operation to understand where the location of inventory for customers and suppliers resides. Drive waste out by optimizing inventory at every point in the supply chain.
Keep track of lead times and lead-time variability and look for ways to reduce them. For example, putting popular products close to the ends of aisles helps order pickers get to and pick those items much faster. Bringing products to workers reduces travel times and searching for products to complete an order.
Inventory management is a complex operation that is not to be taken lightly. Various methodologies exist to manage inventory, from FIFO for perishable items to just in time and more. Whatever methods you use in your operation depends on what your inventory consists of and how fast your customers want their orders. Regardless of the inventory methodology you select, it is important to gain visibility of your entire operation to uncover wastes that can slow processes, to use the best solution for the job, and to slot your inventory optimally. If you do all this, you can assure your customers will be happy and your business will grow.