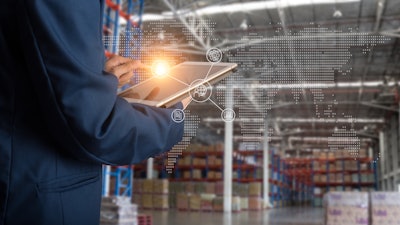
In 2019, warehouse management systems (WMS) vendors continued to make advancements in easy to navigate user interfaces (UIs). They also advanced the deployment of system capabilities on a plethora of mobile devices, and in the production of more cloud offerings that simplified deployment and system support for companies. This continued WMS cloudification made WMS investments and price points more attractive to customers.
WMS vendors also continued their focus on interoperability in the mobile and Internet of Things (IoT) worlds, aiming for as much “plug and play” compatibility as possible with smartphones, voice-activated systems like Alexis and Siri, robotics, barcoding/labeling, and track and trace IoT devices. As a complement to baseline WMS software, artificial intelligence (AI) and analytics were added to enhance informed decision-making for warehouse managers, and also to interact with increased amounts of warehouse automation. All of these WMS moves were needed as a response to the market pressures that warehouses were feeling.
Warehouse Market Pressures
Just what market pressures were warehouses feeling?
In 2019, some of the primary challenges for warehouse managers were time management, inventory tracking and accuracy, and supply chain communication, especially with logistics providers. Products (and SKU numbers) continued to multiply and diversify in warehouses, placing more pressure on inventory tracking and management systems, and also in meeting the expectations of customers.
On top of this, the market demands for increased warehouse capacity and space, and for the ability to rapidly juggle inventory allotments for online and in-store markets, complicated inventory management and workflow throughput processes.
The inventory shuffling between online and in-store product allotments, which was subjected to dynamic swings on a day-to-day basis, presented one of the most formidable challenges.
“In these cases, the order management systems that companies use don’t adequately segment sales by online and physical classifications,” said Kevin DeLine, senior solutions specialist in Netsuite’s Supply Chain Center of Excellence. “On any given day, the forecast can change. It can go from a 60/40 apportionment of inventory between online and in-store sales to a 70-30 mix because of an online promotion. This alters your picking plans, but you still need to control your labor and transportation costs.”
To meet the challenge, many warehouse operators began adopting wave picking, which shortens the order schedule to whatever is happening in a given day. This improves communications and accuracy in warehouse operations, and more closely aligns what is occurring in the warehouse with what’s happening in sales, production and deliveries to customers.
Mobile device deployments, robots and operational automation also continued to move forward in warehouses in 2019. The thinking behind these implementations is that they will deliver more flexibility and reduce errors in operation that are introduced by humans, because the operations the automation and robots perform is repetitive and amenable to processing by machine. The automation also speeds time to market for goods.
As a response to the growing fluidity and dynamism of warehouse schedules and workflows, and additionally the move of warehouses to more automated systems, WMS system vendors focused on delivering more APIs (application programming interfaces) for integration with warehouse robotics and automation.
The Move to a Smart WMS
In 2019, WMS providers also added more AI and analytics to their systems.
“WMS systems are working with AI to expedite the processing of orders which are routed to warehouse operations the moment they come in,” said DeLine.
The automation itself includes the incorporation of automated storage and retrieval systems (ASRS) that automatically place and retrieve products and pallets from one warehouse location to another. The ASRS automation gives the warehouse process repeatability, flexibility and better inventory accuracy. It can also operate on very heavy loads and in refrigerated environments that are unfriendly to humans.
“These systems are complemented with other automated technology such as robots that look like moving pizza pies, and that can traverse the warehouse floor to bring back pallets or racks of goods to human pickers who pick from the pallets and pack the goods,” DeLine said.
Planning for 2020
Key drivers of corporate investment in WMS systems are the need for automation to reduce costs and to keep up with a rapidly changing supply chain; a focus on improving (via automation) the order picking and material handling processes in the warehouse; continued interest in migrating in-house legacy WMS systems to the cloud; and the expansion of WMS capabilities to areas that have been historically neglected, such as yard management.
As warehouse operators consider how best to upgrade their WMS systems and warehouse operations, there are a few best practice recommendations.
Fit your WMS plans to your business. “It’s important to configure your WMS system for your business,” said DeLine. “In some cases, you may need to modify your WMS system to fit the business and, in other cases, you may need to alter business operations to take advantage of WMS system capabilities. If you’re going to a wave concept for your order planning, for example, your overall set of business rules may need to change.
“In other cases, integration with other systems and their ability to use AI can assist you with affinity analysis in the orders that you receive from your customers,” he explains. “For instance, if your warehouse history tells you that a blue medium-sized tee-shirt is the most popular item, you can place the tee-shirts in an easy-to-access location of the warehouse to facilitate rapid picking by using affinity analysis.”
Train your employees to handle the exceptions. “Too many companies, when they add new WMS capabilities or alter warehouse operations, spend time training their employees on the everyday processes,” said DeLine. “The knowledge of how to handle these exception situations prevents bottlenecks and keeps warehouse operations flowing.”
Listen to your employees. Employees in the warehouse are the ones on the front lines and are likely to have ideas on how to improve processes for greater efficiencies and effectiveness. It’s important to listen to them and to engage them in the process of workflow and system reformation. This generates buy-in and enthusiasm from the people “on the ground” in the warehouse. It’s’ one of the best “shots in the arm” a new WMS implementation can receive.