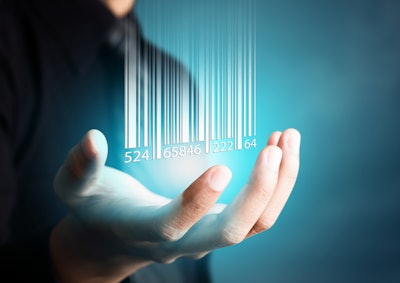
In 2018, commercial real-estate firm CBRE reported that for every $1 billion increase in e-commerce sales, an estimated 1.25 million square feet of warehouse space was needed to keep pace with demand. CBRE predicted that e-commerce-generated warehouse demand could grow by an additional 191.2 million square feet from 2018 to 2020.
However, it is not e-commerce alone that is generating increases in warehouse space and operations. So, too, are increases in product diversity and SKUs that warehouses must track. These SKU numbers are unique to each store, or customer, of the warehouse—and they are exponentially multiplying as new product lines and product variations come online to satisfy the demands of a market where customers want more product differentiation and variety.
In this highly dynamic environment, warehouse systems and managers must be able to track inventory from time of arrival to time of disbursement. This includes every move of inventory that occurs on the warehouse floor—and can extend to track and trace visibility of merchandise that is being transported from the warehouse to final destinations.
To monitor these variegated product and warehouse demands, new developments in barcoding, packaging and tracking have gained traction in 2019 and will be critical to the success of warehouses as we head into 2020.
Here are the key technology innovations that have occurred in barcoding, packaging and transportation, and that have the ability to take warehouse efficiency and performance to new levels.
Barcoding and Scanning
There is a plethora of barcoding, QR (quick response) coding and RFID (radio frequency identification) solutions available today that can be adopted in warehouses, depending on the types of food and beverage goods a warehouse stores and processes.
A single barcode strip can be read by a scanner, while also being fairly secure and less expensive to implement. However, the more robust, two-dimensional QR codes can contain more information and are popular with consumers because they can carry product information such as where a head of lettuce was grown, or what the specific ingredients in a frozen entree are. The drawback with QR codes is that they also have security risks. There is the potential to embed malicious website addresses.
At the other end of the spectrum is more expensive, highly secure radio technology like RFID, which has its advantages in some warehouse environments because it doesn’t require line-of-sight scanning like barcodes and QR codes. The downside of RFID is that RFID radio signals can be disrupted in the warehouse by forklifts, smartphones and other warehouse activities.
Warehouses use RFID when line-of-sight scanning is difficult, but a growing number are migrating to the optical scanning abilities of QR labeling, which can work with smartphones and not the more expensive RFID readers.
The other element of coding and scanning is the printed labels themselves that are affixed to warehouse racks, pallets, containers and boxes of foods and beverages.
The dynamism of e-commerce is forcing warehouses to continuously shift racks of products around, and to relabel racks as product mixes change. Peeling off labels and continuously replacing them is a time-consuming activity, so new label technology that uses better and more flexible adhesives is more efficient.
Warehouses are also moving to multicolor labels because these labels can be used with tiered racking systems to improve processes for slotting, picking and overall inventory management.
“In a warehouse environment, the right use of color makes a label stand out so it’s easier for workers to see from a distance,” said Kurt Wagner, a production design engineer for ID Label, a producer of custom labels.
Packaging and Robotics
To facilitate efficient warehouse operations, packaging must be light but able to protect food and beverage from damage. Packages must also be trackable and traceable, and amenable to automation.
In this area, 3D-printing technology has been a transformative influence.
With 3D printing, packagers can test new designs by creating them with computer-aided design (CAD) software that is capable of producing physical package prototypes. 3D printing is not yet at cost points that make it available for widespread use, but it’s beginning to transform packaging for food and beverage in cost effective ways that improve warehouse operations.
Packagers have also worked on “smart packages” that embed tracking sensors for food and beverage as they travel through the supply chain, including the warehouse. In some cases, packages are equipped with RFID technology that sends out constant signals on product location in order to prevent theft.
Collectively, these technologies are contributing to improved supply chain visibility for warehouse operators. Sensors can also monitor food and beverage in the warehouse to ensure that they are being kept at proper temperature and humidity levels to prevent spoilage.
Improved packaging also lends itself to new warehouse workflow concepts that involve robotics and automation.
One approach, known as palletization, consists of placing bulk or packaged goods on pallets for storage and handling. The pallets can be equipped with sensors for tracking and tracing, and also for purposes of inventory management. They also work well with automated robotic systems, which more warehouses are adopting.
The conversion to pallets for goods that historically weren’t palletized, has made it easier for autonomous robots on the warehouse floor to move goods from area to area, and even to sort smaller items into boxes for delivery. These robots can move freely throughout the warehouse without manual intervention, and can easily be taught new routes as warehouse locations and routes change.
Logistics and Tracking Sensors
There are warehouses that opt to run their own logistics, while others employ 3PL providers to handle the transport of goods to and from the warehouse.
In either case, warehouse managers want to know the status of products as they enter and leave the warehouse and, in some cases, what happens to products along other points of the supply chain.
This is an area where sensors reporting location and condition of goods come into play. They provide visibility to everyone along the supply chain, including the warehouse manager.
“This technology is especially helpful to warehouse managers who work with multiple 3PLs and must make the decision as to which 3PL to employ for a particular shipment route,” said Ajay Rane, vice president of global business development for Sigfox, an IoT network provider. “By installing a tracker inside a container at the warehouse, a manager can tell which routes trucks take, and determine which 3PLs are most efficient on which routes. This reduces transportation costs and speeds time to market.”
“We’re seeing a lot more transitions of scanning on and off the truck,” added Jay Steinmetz, CEO of Bar Coding, Inc, which develops barcode, RFID and mobile solutions. … “Cubing of pallets and image systems are validating that the appropriate equipment is being delivered to the appropriate location or appropriate truck.
“In addition, technology using RFID is allowing customers to collect all the appropriate route keys for the delivery of goods at night when there’s nobody at the customer site to receive them.”
Modernizing Warehouse Operations
Warehouses have and are adopting new technologies in barcoding, packaging and logistics—ever mindful of the demand for quick and accurate service as volume and space demands climb with e-commerce sales.
The key is investing in the right types of technologies that fit each warehouse’s operational situation.
“Prioritize your warehouse practices by optimizing for return on investment,” said Steinmetz. “Make sure the systems you’re putting in place are well documented and will be supported. Validate that the equipment and technology being deployed has a long life cycle and is being backed by a company that can be there in the long-haul.”
The value of vendor support cannot be overestimated. Most warehouses lack deep knowledge of new systems and technology hardware. Vendors can assist in proofs of concept and in establishing ROI formulas for the goals the warehouse sets for itself. Vendors can also take charge of configuring their solutions for the needs of a particular warehouse, and in supporting the migration to a new technology.
“Advanced technology comes at a price,” said Steinmetz. “You need to have the ability to not just understand the technology but to maintain the technology and have the intellectual support to manage the implementation over the long term.”
For most warehouses, it makes sense to take the modernization process step by step—and to never consider the addition of a new technology or solution without a specific business goal in mind, with metrics to measure achievement of that goal. Common goal target areas include efficiency, cost reductions, optimization of workflows and space, error reduction, reduced warehouse workflow times and inventory control.
“Make sure you have the resources to manage and monitor the operations of the equipment and solution you deploy,” said Steinmetz. “Also, utilize the latest algorithms for reducing deadheading and optimization of merchandise throughout the warehouse.”
Finally, work for greater mobility and agility in your warehouse operations.
SKU numbers from many different suppliers will continue to multiply. E-commerce will continue to fuel warehouse space demands. Product demands will become more fluid and will require frequent relocation of warehouse bins and racks.
In this environment, techniques like dynamic slotting, where product locations within the warehouse are allowed to change and bins are refilled with any random product that can fit into the bin, might be employed. Along with this, there should be a means of tracking inventory with automation and sensor-based technologies.
“We see the use of artificial intelligence, robotics and dynamic slotting increasing the efficiencies of everyday warehouses,” said Steinmetz. “However, for technologies to work like AI, robotics, barcodes, RFID and packaging advances, the warehouse’s human staff must be prepared and trained to use the new technologies.”
This is one reason why it makes sense for warehouse managers to proceed methodically by making changes in an orderly way that gives staff time to get comfortable with new work processes. If this doesn’t happen, staff will find “workarounds” to these processes that will erode some of the areas of gain that the technology was designed to deliver.
At the end of the day, any new technology must be able to integrate with existing systems, whether the new technology is in barcoding, packaging, robotics or logistics. The integration pertains to the systems in your warehouse and your company, and may also require compatibility with the systems that business partners such as 3PLs are using—in other words, any organization that is integral to the success of your own warehouse operation.