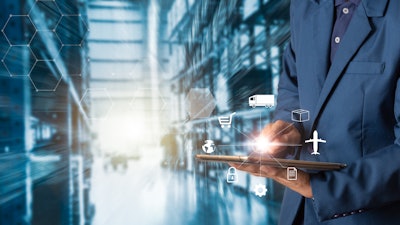
Aera Technology’s Kaushal Dave, global vice president, solutions development and customer engagement, notes that no matter the size of the company, “the problem always starts with inventory.”
The approach to solving the inventory enigma is changing though, he says.
“Up until now, a mathematical approach was always used. In other words, a mathematical approach as in an optimizer, which includes linear programming and quadratic programming—basically, very complex mathematical heuristics,” says Dave.
Human Thinking
Aera Technology began experimenting with a cognitive automation and augmentation approach, and began asking a few simple questions: How does a human look at inventory? What’s your intuition telling you? How many things do you need to look at before making a decision on changing inventory variables?
Dave explains that, “The human mind, from a cognition standpoint, looks at a few things and says, ‘Here’s a shortage; here’s an excess. I’d like to move inventory from here to there, but I need to know how much it’s going to cost to do it.’”
Read Next: Technology, Innovation Drive Warehouse Safety
There are also questions about if it’s best to move the inventory, or produce more and ship it from the factory. Alternatively, would it be best not to do anything and let the replenishment cycle go through? Therefore, when the minimum ordering quantity or the reorder points kick in, it will be automatically replenished.
“The human mind thinks this way,” says Dave. “So, we set out to mimic the human mind in order to solve the inventory optimization problem.”
While the human mind can look at three of four things concurrently, and then make evaluations and decisions, “The machine can look at unlimited things,” he says.
These include such variables as order volatility, demand volatility, production frequency, current safety stock levels, daily ending balance of inventory, warehouse capacity and so on, combined with the agility of the supply chain. The goal is to arrive at a specific production location combination.
“The human mind… looks at a few things and says, ‘Here’s a shortage; here’s an excess. I’d like to move inventory from here to there, but I need to know how much it’s going to cost to do it.’” — Kaushal Dave
Fundamental Shift in Optimization
Aera Technology worked with three separate companies, in particular, to demonstrate the effectiveness of their inventory optimization technology: one of the world’s largest CPG companies, the biggest tobacco company, and one of the largest alcoholic beverage companies in the world.
In each pilot, Aera was able to reduce safety stock and free up working capital.
For the CPG company, “We looked at approximately 10,000-plus recommendations, and delivered substantial cost savings on these inventory reduction opportunities,” says Dave.
At the same time, “We are also recommending inventory increases in some locations, because it’s not always inventory reductions that are needed.”
This is “a very different and fundamental shift in how we see inventory and how we approach the problem,” he says. “We allow the machine to do its job and digitize the human approach. And of course, do it 100 times better by looking at 100 different things, which is not possible with the human mind.”
Disruptions, either internal or external, also pose challenges to inventory optimization. Some examples include port strikes or weather events, or even huge sales promotions.
“Supply chains are more volatile and complex than ever, and they’re more non-linear than ever,” Dave notes. “There are always going to be disruptions, but reacting with the best decision—or even better, being able to be proactive—is what the technology provides,” that a human cannot.
Ongoing Digitization
The value of Aera Technology’s solution is evident for large multinationals with multiple, complex systems and supply chains.
One company currently working with Aera has 57 ERP systems alone. Another, a CPG company, has a number of separate systems.
“They evaluate 100 start-up vendors every year, so they have many systems. There’s a real benefit for them to accumulate data from all those different systems, harmonize and then monitor all those data sets concurrently, and then have the solution provide recommendations,” he says.
Read Next: Why Innovation is the Name of the Distribution Game in 2019
According to Dave, the future trend is the ongoing digitization of supply chain processes and bringing more autonomy to the process as well.
“We are seeing a tremendous amount of interest from C-level executives because they understand the value of this,” he says. “While supply chain planners or managers may think they’re always making the best decisions, senior-level executives know otherwise.”
There is simply too much information and data to evaluate. Not to mention, “If a planner leaves the company tomorrow, they take their knowledge with them,” says Dave. “So, it’s imperative that the best planning and the best planner’s experience is digitized within a system, and that it’s augmented with other systems’ capabilities.”