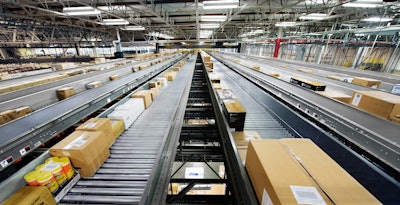
For e-commerce and traditional retailers alike, times of peak demand can be a challenge, pushing fulfillment operations to the limit in the rush to serve immense order volumes and meet promised service levels. The ultimate measure of success is getting product to the right place at the right time, leading to satisfied customers and repeat business.
Here are five strategies to help fulfillment operations accurately and cost-effectively handle peak demand.
1. Analyze Business Data to Build Order Profiles
Even if paper printouts and manual order entry still play a role, nearly every company uses some type of software to manage fulfillment operations. Collecting and analyzing order data from software systems to fuel informed management decisions on staffing allocation and system layout is an important step in preparing for peak demand.
Consult lessons learned from previous peaks to inform strategies to manage the current peak. Historical data can show order profiles, explain customer preferences, identify the most profitable stock-keeping units (SKUs), forecast labor needs, and categorize fast and slow movers. The empirical benefit of this information is obvious, but actually extracting it can be challenging, even for large companies with enterprise resource planning (ERP) solutions and warehouse management systems (WMS).
Order profiling and warehouse planning can be continuously optimized with the addition of a warehouse execution system (WES). This software uses historical performance data and real-time analysis of orders, labor, equipment and inventory to optimize wave planning, storage and retrieval, replenishment, restocking and slotting to minimize walk time and improve labor efficiency.
2. Choose the Right Order Fulfillment Solution to Manage Demand Cycles
The basic building block of a scalable automation solution is a system that not only drives a range of picking technologies to increase the efficiency of order fillers, but also manages automated equipment to keep fulfillment running at peak efficiency. As maturing operations make increased investments in automation, using software that can manage the entire fulfillment process, such as a WES, enables operations to get the most out of their automation investments.
A key benefit of implementing a WES is its support for automated and dynamic workflow adjustments, and the ability to quickly respond to velocity and profile changes. This synchronization is especially beneficial for an e-commerce distribution center (DC) that typically has more individual work zones than a traditional retail DC, with kitting, wrapping and other special services. Optimizing order batching and dynamic slotting allows operations to handle specials and flash sales, and keep pace with rapid changes in buying trends.
Temporary labor commonly plays an important role as companies adapt to the peak-demand rush. Available as an independent system or as part of an integrated software package, labor management software (LMS) can expedite the integration of temporary workers to handle peak demand. The most robust LMS systems store the historical performance of full-time and seasonal workers, and grades it against productivity standards to allow operations to make more informed staffing decisions.
3. Cross-Train Employees to Maximize Throughput
Fast movers and slow movers can change from day to day and week to week during times of peak demand, impacting order filler efficiency, pick density, walk times and replenishment cycles. While adherence to a well-defined, efficient production plan is important, peaks sometimes necessitate trading the efficiency and productivity of individual employees for maximum overall capacity.
Cross-training all able staff to fill orders can help meet throughput demand, and reduce the cost and impact of adding contract labor. While cross-trained staff may be less efficient than experienced order fillers, they can help increase overall throughput. As an added positive, cross-training helps to remove silos within an organization as employees learn to appreciate different facets of the business.
The right technology can help, too. Voice solutions can get new pickers up and running in less than half a day through clear, step-by-step verbal instruction. LMS also offers training curves to set realistic expectations for inexperienced order fillers and allow management to better gauge progress.
Pick planning and order batching enable operations to add order fillers without creating downstream bottlenecks. A fulfillment technique called mirroring, which involves duplicate slotting of high-demand SKUs in a forward pick area, becomes extremely important to spread out process volumes, and reduce congestion and unproductive competition. WES can distribute the pick volume across the mirrors so that labor and assets are more productive and better utilized.
Similarly, optimizing slotting of fast-moving SKUs and paying attention to order filler ergonomics is a cost-effective method to maximize throughput. Fast- and medium-moving items can be stocked on flow racks in the area between the order filler’s hip and shoulder, known as the golden zone, with slow movers in less convenient reach and bend areas.
4. Push the Delivery Window
Accommodating last-minute orders is a crucial competitive factor in time-sensitive order fulfillment. There are several strategies DC managers can use to extend daily order cut-off times. An initial step is to frontload the morning with replenishments, and pre-stage fast movers in order to free resources for afternoon or evening picking. As businesses mature, investment in an automated storage and retrieval system (AS/RS) offers quick access to cartons, totes and trays, an ideal solution for operations with high-turn inventory storage and short order cycle times.
Sending an order filler around the warehouse to fill just one order is an inefficient use of time. Apply the method of optimized batching to combine orders with similar SKUs into one postponed pick order, saving time and driving efficiency, while still meeting ship time windows. An advanced WES can automatically release orders at the best time to ensure maximum productivity while meeting service level requirements.
5. Maximize Order Accuracy with Automation
Fast-paced distribution operations can gain a competitive advantage over manual competitors with automated order fulfillment systems. Automated picking technologies like voice and light offer a proven, timely return on investment, and enable near 100 percent order accuracy and up to a 35 percent increase in productivity. In addition to accumulating reverse logistics costs, shipping the wrong product levies tremendous costs in the form of low customer satisfaction, greatly diminishing chances of repeat business.
Determining the impact of inaccuracy in a manual fulfillment operation requires calculating the ratio of error-free orders over the total orders shipped, including the number of shorts and returns. This creates a baseline and key performance metrics for productivity goal-setting. A real-time order fulfillment system provides accountability and visibility into order accuracy, alerting operators of errors before the shipment goes out the door. This is key to maximizing labor efficiency and preventing inaccurate shipments.
Whether replenishing stores or shipping direct to consumers, order fulfillment operations must be in high performance mode, ready to handle peak volumes. Follow these guidelines and consult with a system supplier to help win the race to deliver the right product to store shelves or the customer’s doorstep.