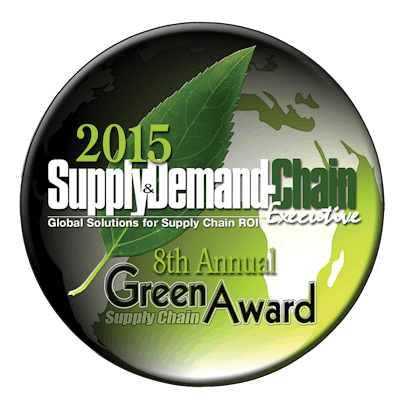
We’ve long taken the stance that being green and profitability are not mutually exclusive. What better way to illustrate that point, than with a forward-thinking bank that practices sustainability? Of the almost 200 entries we received in this year’s Supply & Demand Chain Executive Green Awards, we’ve selected Dallas-based Comerica Bank as the outstanding entrant.
In its submission, Comerica wrote that it “understands sustainability as an approach to conducting business that seeks to meet the needs of the present in ways that do not compromise the ability of future generations to meet their needs. We recognize that protecting and preserving the environment is important to the health, well-being, and prosperity of the people, businesses, and communities we serve. We are therefore committed to incorporating environmental stewardship considerations into the ways we do business, including our processes for procuring goods and services. Our approach to greener procurement is to introduce more sustainable practices into the ways we work with our supply chain to achieve improved economic and environmental performance.”
Over the last two years, Comerica compiled feedback from its suppliers and key stakeholders to develop its Sustainability Impact Analysis to help shape its sustainability program and reporting. The company initially focused its attention on better understanding the current environmental practices and performance of its most significant suppliers to establish a baseline to measure future progress and set targets for improvement. Other supply programs, such as its Supplier Diversity Program, address aspects of sustainability apart from environmental issues.
Based on the use of a company-developed environmental questionnaire and scoring tool, Comerica assesses and rates its most significant suppliers and sets goals for improving the performance of the group as a whole. Active engagement is preferentially targeted at those suppliers assigned to lower performance bands. During their regularly scheduled reviews, key suppliers are told how Comerica views their environmental sustainability performance and where it sees opportunities for improvement. Previously rated suppliers are rescored on a three-year cycle to evaluate whether progress is being made or maintained.
New potential suppliers of significant goods and services are evaluated and scored as part of the RFP process. Placement of the company’s business considers environmental performance in addition to quality, pricing, and delivery needs, consistent with good procurement practices.
“As we continue on our long-term sustainability journey,” the submission explained, “we have identified some environmental sustainability issues that are important to our stakeholders and relevant to our industry and company. We have therefore adopted an Environmental Policy Statement which contains a series of specific commitments. Some of those commitments have implications for the procurement function and helped shape our early efforts to improve our sourcing and supply chain practices.”
They include:
- Helping suppliers increase their awareness of both the risks and opportunities that may arise from climate change developments and the growing global imperative to conserve energy and natural resources, use them efficiently, and minimize waste.
- Implementing initiatives within the company to reduce, reuse, recycle, and re-think processes in ways that decrease overall use of natural resources and generation of wastes.
- Reduce paper consumption.
- Where practical, preference in the procurement processes will be given to products and suppliers that demonstrate superior environmental performance.
- Track and publicly report progress and periodically seek feedback from stakeholders on how we can improve our performance.
Led by the Comerica’s corporate executives—spearheaded by CFO Karen Parkhill—other programs include the Environmentally Preferred Procurement (EPP) Program and the Green Procurement Work Group. EPP is designed to promote and support the growth of a sustainable supply chain. The intent is to influence suppliers to adopt more environmentally responsible practices over time.
The Green Procurement Work Group oversees the work of the EPP. Chaired by senior procurement management, it meets monthly and consists of individuals from Corporate Procurement, Corporate Sustainability Office, Corporate Marketing, and two key supplier partners. Its objectives include ensuring corporate adherence to EPP practices, conducting periodic reviews of EPP practices and progress, emphasizing EPP objectives in the development of annual departmental purchasing/contracting plans, and conducing EPP training for those with procurement responsibilities.
The Green Procurement Work Group’s annual action plan to advance Comerica’s progress in this area is reviewed and approved by both the Sustainability Council and the company’s Management Executive Committee (MEC). The Council receives quarterly reports on the progress of the work group, and the MEC reviews performance in this area against expectations in the annual action plan once a year. External reporting to stakeholders is accomplished via the company’s biennial GRI-based sustainability reports and in the more limited environmental sustainability progress reports published between GRI reporting cycles. Training on sustainability has been provided for all procurement team members and is also provided to other Comerica colleagues with buying responsibilities.
“We are confident that that the adoption of environmentally responsible procurement practices will help us to become a stronger and more successful company over time and will enable us to create greater long-term value for our stakeholders, including our shareholders, customers, employees, suppliers, and host communities,” Comerica wrote.
And now, here’s a look at our other Green Supply Chain Award winners:
ALOM put place key sustainability metrics in place in 2014-15 that include development of a two-part strategic sustainability plan. Part 1 focuses on ALOM operations across its global facilities (electricity efficiency, recycling, enviro-friendly cleaning solvents, employee transportation, etc.). Part 2 focuses on specific ALOM client service offerings.
Basware’s solutions, allow companies to improve efficiency, visibility and control, and achieve significant environmental benefits. A large U.K.-based pharmaceutical chain, for example, processed many of its 1.2 million annual invoices. Moving to a completely electronic system, it is on target to save more than 419 trees and 3.5 million pieces of A4 paper each year.
B-Stock helped clients ditch traditional methods, including landfills, and replace them with a sustainable solution in the form of a B2B liquidation marketplace. This enabled the recycling, repurposing, reuse or resale of more than 24 million items. In the past 18 months alone, 21 million previously deemed excess items have been sold for reuse, resale or recycling.
CaseStack, by combining separate LTL deliveries heading to the same Retail DCs, stores, or regions into one full truckload, helps minimize dock congestion and reduces the number of trucks on the road. This, in turn, reduces greenhouse gas emissions. It helps streamline packaging, builds partnerships with efficient carriers and eliminates waste from the ordering and tracking process.
Cass Information Systems solutions help its customers meet green supply chain goals. The direct result is a significant reduction of paper transactions in the areas of shipping documents, billing (freight invoices), payment transactions, and information delivery. These are accomplished without sacrificing controls and accuracy.
Celestica reduced the need for 53 ocean containers, avoiding approximately 28.5 metric tons of CO2e for a single product for one customer. In another case, Celestica’s solution reduced the need for 44 ocean containers, avoiding 20 metric tons of CO2e. Not only did this represent significant carbon savings for customers, it also generated concrete financial savings.
DiCentral's solutions inherently help create and sustain green supply chains. This is achieved via streamlined processes, a massive reduction in paper and other durable goods use that results in millions, if not billions, of pounds of waste not being introduced into our already full landfills. Global consciousness is not only preached, but practiced.
DSC Logistics has been tracking sustainability on electricity, natural gas, water, propane, and recycling across 40-plus locations for four years. Its yearly goals include further waste stream reductions, implementation of LEAN initiatives focused on reducing process steps and waste in the supply chain, and utilization of strategic supply chain modeling to reduce logistics center footprints.
East Coast Warehouse & Distribution’s sustainability initiative is continually growing and evolving. It currently calls home the largest solar powered warehouse in the Northeast, which allows it to produce more than 810,000 kilowatts per hour of clean, renewable energy each year. Motion sensing technology reduces the time the fixtures are drawing electricity, as they turn off when there is no activity within 70 feet.
enVista works to promote green business practices with clients, but also has taken steps to ensure green practices within the workplace with its Going Green initiative. All enVista associates are reimbursed for purchasing energy-saving LED light bulbs, receive a partial reimbursement for purchasing a new hybrid car, and are reimbursed if they purchase and plant a tree at their home.
eZCom Software’s EDI (Electronic Data Interchange) solution, Lingo, has made supply chain management streamlined and more efficient, but also much more eco-friendly. It enables companies to move to electronic transactions, which reduces paper usage by thousands of tons yearly, and reduces carbon emissions. It also requires less energy and fewer resources.
Geodis Supply Chain’s EcoTransIT tool measures emissions of greenhouse gases and atmospheric pollutants for all means of transport. It is aligned with the European standard which defines a methodology for calculating greenhouse gas emissions in the transport sector. Geodis’ performance has improved continuously over the past five years and attained its best score in 2015.
Inmar’s efficiencies save clients millions of road miles per year, a significant carbon-footprint and cost reduction. One large Midwest grocer will save more than 10 million miles by implementing better transportation sourcing and networking for distribution; another client has the potential to save 3.7 million miles per year through optimizing returns optimization.
Kenco’s suppliers are required to incorporate minimum sustainability policy compliance. The company has invested in training and certification of its Leader of Sustainability and the program in as an Association of Energy Engineers Certified Energy Manager, Certified Energy Auditor and as a Six Sigma Black Belt to enable a synergistic execution of sustainability initiatives.
NeoGrid provides solutions which, by their very nature, contribute to the sustainability of the supply chain by virtually eliminating paper waste with its EDI solution. Recently, NeoGrid contributed to the savings of 350 tons of paper, which is the equivalent of about 4,000 trees. This is significant because it contributes to countless amounts of CO2 emission credit and landfill pollution.
Omnify Software’s database enables one customer to incorporate all supplier certifications. The customer can update all specific vendor items with one update per supplier and not have to update 31,000 records independently. It has realized an approximately 17 percent increase in efficiency for its environmental practices.
Satellite Logistics Group helps beverage companies dispose of out-of-date, damaged or recalled product in an environmentally friendly manner that complies with EPA requirements. The company’s EcoBev material recovery service is the only turnkey nationwide green solution for beverage disposal. SLG removes expired, mislabeled, excess, and damaged beverage goods from distributor and producer warehouses, and ships container and contents to be recycled.
Source One seeks to find not only sustainable alternatives for its customers, but also to identify affordable options helping to make the decision-making process easier and more enticing toward sustainable sourcing. Its analysts seek opportunities to implement green or sustainable sourcing options as a component of every sourcing engagement it takes on.
Transportation Insight performs LEAN supply chain assessments to determine where to cut waste such as eliminating expedited shipments, lowering energy usage, reducing packaging, optimizing transportation loads and modes, gaining control over inbound and outbound shipments and improving communication and collaboration with transportation partners, vendors and customers. It also is a SmartWay Transport Partner.
More Green Supply Chain Award Recipients
American Global Logistics
BizSlate
Bona
Chainalytics
Cisco Systems
Columbia Manufacturing
C.R. England
Crown Equipment
Elemica
ELynxx
GreenPrint
HighJump Software
IHS
Ingram Micro Mobility
Insight
International Asset Systems
Kane is Able
Lineage Logistics
Li Tong Group
LocusTraxx
Log-Net
Murphy Warehouse Systems
Paragon Software
Penske Logistics
PINC Solutions
RM2
Schenker
Spinnaker
Supply Chain Optimizers
Thomson Terminals
TPS Logistics
UNEX Manufacturing
W&H Systems
Westfalia Technologies