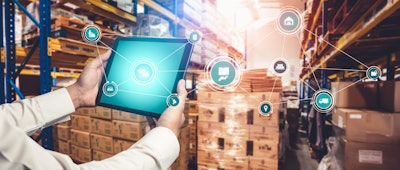
There’s a perfect storm brewing in the evolution of warehouses and DC businesses – and the optimization solution lies in creating a recipe in which technology is a main ingredient.
The industry faces a number of challenges. Increased customer expectations and the growth of ecommerce - magnified by labor issues - have put more pressure on financial performance and corporate transformation.
After the pandemic made distribution excellence even more essential to obtaining necessary goods and services, the warehouse function has been elevated to a central strategy for many companies. Companies have changed their thinking from viewing distribution as a cost center to thinking about distribution as a competitive advantage. There is an urgency to act on these changing market conditions, but some changes take a long time to implement.
So, what’s the answer? In my eyes, it’s a marriage of the old and new. If you use data science-led innovative software products as the platform and infrastructure for growth, you can apply them to the basic tasks in the DC – picking, batching, travel. To tie things together – it’s a collaboration between workers and technology that enables workers to be more efficient and effective at their jobs.
A Lucas Systems survey found that nearly 3 out of 4 (74%) on-floor workers will consider a pay cut at another company for an opportunity to use technology if it helps them in their job. Workers also said they are physically spent, spending over a third of their day walking and would welcome tech’s help in the form of robots or other tech tools. This tells me that workers are eager to use technology in new beneficial ways.
Seizing the Opportunities in Your Warehouse
From constant enhancements focused on incremental process changes to continuous optimization and operational transformation, DCs need tools that can help them manage the week-to-week, day-to-day and even the hour-to-hour changes that occur. It’s about finding the real problems, not the symptoms of the problems. It also is about prioritizing solutions which optimize DC operations and processes and allow frontline workers to work to the top of their ability level.
The opportunity lies mainly in three areas:
- travel optimization
- intelligent batching
- worker productivity/engagement
There have generally been only slight gains in picker productivity or in slotting programs to reduce travel, with pickers in most facilities still spending more than 30% of their day traveling throughout the warehouse rather than picking product. But there are ways to optimize and reduce travel and generate immediate productivity gains without changing overall systems. That’s where AI, software and technology come in.
Software’s Power
Let’s look at how applying technology could transform your operation. In batching work, there are quite a number of variables to consider, including:
- Proximity
- Shipping time
- Order priority
- Product locations
- Product dimensions
- Potential travel path
Software can dynamically apply real-time optimization algorithms, putting work into priority sequence, based on rules that you can configure and adjust, and run millions of possible combinations in a split -second, so that users are never waiting for work. For example, maybe you concentrate pick density early in the day, when there is time before the first orders are due at the dock. As the day progresses, the software can automatically transition to optimize for priority, as route cut-off times are approaching, based on the schedule for that day or week. The software then determines an optimized path for the user to take through the warehouse to complete their work, taking into account a number of factors such as:
- Travel distance
- Zone sequencing
- User start/end points
- Cost of moves (e.g., turning around)
- Directional aisle restrictions
Incremental Change Can Bring Dramatic Productivity Gains
What’s important to understand is that you can generally achieve excellent results without completely changing and updating systems, like a brand-new WMS or ERP. The behind-the-scenes parts of the process, and how you get to the answers is incredibly complex and best handled by software technology, ideally using artificial intelligence and machine learning to continually iterate and enhance the process.
Using AI to optimize DC processes has proven to be powerful in ecommerce pick-to-cart operations, where customers report doubling productivity without any fundamental changes to their picking processes. Although the biggest productivity gains are seen in each picking, the AI-based software tools have proven equally applicable to case picking, replenishment and other activities where workers are visiting many locations per work assignment. In grocery and food DCs, AI-based optimization has demonstrated travel savings of 15%-30% in case pick to pallet applications.
The right software optimizes hands-on work and streamlines manual processes, thus making the work easier, faster and more accurate for workers. For managers, machine learning-based applications provide new insights and recommendations, empowering them rather than taking control out of their hands. Ultimately, that’s better for all, and for the overall business.