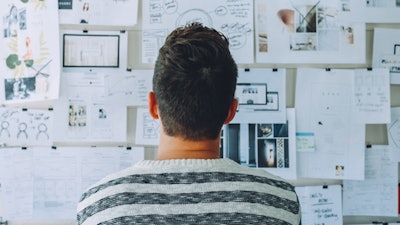
As manufacturing organizations navigate disruptions resulting from the global pandemic such as labor shortages and social distancing requirements, production is slowly ramping back up. It is more important than ever in this constrained environment to ensure that high-quality products emerge from the manufacturing process. Here’s how organizations can improve their finished-product first-pass quality yield for primary products—a quality measure that should be on every manufacturer’s radar—by focusing on four key areas.
Finished-product first-pass quality yield for primary products is a measure that calculates the percentage of finished primary (or high-level) products that meet all quality specifications at a final test point. It is part of a set of process efficiency measures that help organizations optimize the performance of their production processes by minimizing waste and refining resource consumption. Strong performance on this measure indicates that the organization’s processes and equipment are reliable with fewer defects, re-work or scrap.
Using data from APQC's Open Standards Benchmarking database in manufacturing, Figure 1 shows that top performers achieve almost 98% success in meeting quality standards on the first pass. Bottom performers are almost 8% lower, which leads to increased rework and/or scrap as well as higher costs and slower cycle times. Poor performance on this measure means wasted resources and potential revenue losses or delays.
Figure 1APQC
Unpacking the causes of low performance
The first step to improving finished-product first-pass quality yield is to determine the causes of lower performance. Four factors that can impact this measure are:
1. Incoming material quality
2. Timeliness
3. Process documentation and training and
4. Advanced analytics
Incoming material quality
The quality of supplier materials (or lack of it) can have a decisive impact on finished-product first-pass quality yield, especially if quality defects are not discovered until the end of the manufacturing process. Finished products cannot be sold until defective parts are replaced – costing time and money. Therefore, it is important to catch these potential problems as soon as possible, even as early as at the point of receipt.
Timeliness
In response to discovering defective output, a manufacturer could halt its production process to replace the defective parts, address the issue, and ensure that components are inspected intensively before production. But, part quality is not the only factor that manufacturers need to consider—timeliness is often critical as well. For example, if an organization has seasonality to its sales (e.g., holiday-specific products) or is facing suppliers with longer lead times due to the Coronavirus disease (COVID-19) or port congestion, suppliers may not be able to provide replacement parts in time for production ramp-up. If inventory levels are too low and defective parts cannot be replaced in a timely manner, the company stands to lose potential revenue.
To get the parts in a hurry and avoid long transit times, a manufacturer could turn to alternate suppliers located closer, but the costs of expedited orders can be much higher and eat into profit margins. Keeping an eye on multiple timeliness measures in manufacturing ensures that products are flowing through appropriately and getting to market when they are needed. Timeliness measures include takt time (the average time interval between the start of production of one unit and the start of production of the next unit when items are produced sequentially) and cycle time (the time it takes to complete the production of one unit from start to finish). Looking at a balanced set of measures, including quality, cost and cycle time, helps organizations make informed tradeoff decisions.
Process documentation and training
Even with the highest-quality components, a company can still end up with lower finished-product first-pass quality yield if it doesn’t practice good process management. For example, if the process steps for assembly are not documented and accessible, then replacement or less-experienced employees (perhaps filling in due of absenteeism related to COVID-19) can and likely will end up making mistakes that result in a higher number of defects. Skills, training and documentation for processes are just as critical as the quality and timeliness of raw materials.
Advanced analytics
Ensuring equipment up-time and regular maintenance is vital in manufacturing. Leading companies are investing in predictive analytics and Internet of Things (IoT) sensors that provide real-time data about systems and equipment across the enterprise. This data not only provides deeper insight for better decision-making but can alert the company when machines are not operating as they should. These technologies enable organizations to avoid unplanned machine downtime that can negatively affect cycle time, cost and even quality.
Key takeaways
Achieving top-tier performance for finished-product first-pass quality yield for primary products takes careful planning, good supplier relationship management, well-documented processes and investments in the right technology. Gaps in any of these areas will only not put a dent in first-pass quality yield but may also force organizations to make tradeoffs between cost, quality, timeliness or process excellence.