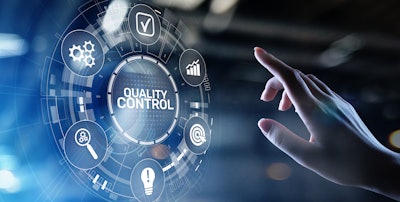
Quality control of the supply chain is paramount – not only for one industry but for all industries. While there have been improvements since the pandemic, there is still room for organizations to refine, enhance and strengthen their supply chains, particularly with more digitized processes and ERP solutions that ensure quality control. Without it, organizations will be faced with more recalls, slower production, inaccurate reporting and other problems that ultimately prevent them from providing safe products to their consumers.
For example, Peppercorn Collection pulled a gift set due to possible mold contamination, and Lidl US recalled one of its edible advent calendars because some of the items could be contaminated with Salmonella. But, while these recalls gain headlines for their broad risk to human health, a significant number of products are removed from store shelves due to undeclared allergens. From meatless burritos and breakfast sandwiches to ready-to-eat crispy chicken, undeclared allergens pose a huge risk to those who are allergic to any of the unlabeled ingredients. Impurities are another source of trouble – Lupin Pharmaceuticals recalled four lots of Quinapril Tablets due to the potential presence of N-Nitroso-Quinapril Impurity, which could increase the risk of cancer.
Without an effective data structure, organizations cannot reduce their risks to and frequency of recalls. In order to deliver the level of accountability, traceability and security that’s needed to maintain operations and keep consumers safe, businesses also need simple communication between all parties, including production, logistics and sales.
Streamline serialization data to prevent future problems
Businesses should start by coordinating all elements of their network, which will streamline their processes, as well as compliance, and bring complaints and reporting into a single view. This is an essential function when trying to determine the need for or cause of a recall. For example, bio/pharmaceutical companies can streamline their serialization data to guard their supply chain from counterfeit drugs and pinpoint the exact location of a particular ingredient. The alternative would leave both bio/pharmaceutical companies and their supply chains vulnerable to the potential recalls they are trying to avoid. They may inadvertently incorporate counterfeit components into their drugs, and food and beverage companies could end up doing the same with their products, if they mistakenly believe the ingredients came from legitimate sources.
To ensure this doesn’t happen, they need to know the source of everything that goes into their products before they ever make it to consumers. In order to do that, they must possess the ability to meticulously drill down and find where a crate or pallet is, or where the contents have come from, that the supplier they source the materials from has been approved – and that is only possible by streamlining serialization data.
Rely on a single system that houses data in one place
When using technology that optimizes data from the five levels of serialization, decision makers can gain insights across the supply chain to analyze product flows, understand logistics, transport processes and make the changes to remove inefficiencies. Consider the challenge of siloed data – it’s inefficient and ineffective, limiting access to a select few instead of providing it to all who could benefit from that information.
Data that’s separated in different systems may not be safe if those systems are bolted together and information is passed between them. The problem compounds if data is transferred between modules and databases. Doing so may inspire the use of Excel spreadsheets and other outside solutions, eliminating the ability to achieve a single source of truth. When relying on makeshift solutions, businesses unavoidably increase their risks – they may be more likely to enter an incorrect lot number, or someone may forget to delete a number after a lot was de-issued and re-issued.
It would be far safer, and much more efficient, to rely on a single system that can house data in one place. This will help organizations keep better track of their most important details, including expiration dates, which is vital for any food and beverage or pharmaceutical company producing products with a short shelf life.
Build a smarter supply chain
Bio/pharmaceutical companies, as well as food and beverage manufacturers, need quality control technology that prevents the wrong products from being picked, consumed or shipped. They need technology that includes checkpoints that prevent users from bypassing steps in the process and confirms that each product shipped meets that not just product specifications, label requirements, but also customer specifications.
When delivered through a modern ERP solution, QC technology can reduce the risk of liability and product recalls and ensure that accurate, real-time QC test results are accessible to all stakeholders. Most importantly, modern ERP makes it possible to track and trace every component to a batch or the smallest production unit, reducing the likelihood that contaminated, mislabeled or unlabeled products will be shipped. With this powerful technology in hand, supply chains can get smarter and recalls can be minimized.