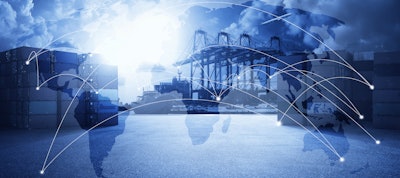
Many factors have converged to create an unusually high-risk environment for companies doing business on a global scale. Most recently, the conflict between Israel and Hamas threatens to have a destabilizing impact and create economic volatility in the region and beyond. This conflict adds to the long list of ongoing or potential new risks for global firms; the ongoing war between Russia and Ukraine, new international ESG regulations, reports of forced labor in China’s Xinjiang region and resulting regulation changes, and a slow logistical recovery from a multi-year pandemic have left supply chains highly disrupted.
As a result, as companies look to adjust their supply chains to increase efficiency and reliability, the math on what geographies are considered too risky or not has changed. Sourcing teams are looking to assess where risk lies in our current moment and shift away from suppliers in those regions; in many cases, that means reshoring.
What is Reshoring?
“Reshoring” is the term we use when a company moves production back to its home country. This helps companies to keep a close eye on their supply chain and steer clear of the risks involved in areas of the world that have become more geopolitically or economically risky in recent years. Even some countries that have long been go-to outsource locations are being reassessed thanks to high levels of volatility.
There’s also “friend-shoring,” which involves moving production from a potentially unstable country to a different, more friendly country or region, but not necessarily back to the company’s home nation. Naturally, this comes with a lesser degree of visibility and flexibility when working with suppliers (since there’s a geographic distance as well as additional country- or region-specific laws and regulations to follow), but in some situations moving to a place of lesser risk could be enough for the time being.
How Reshoring Helps Supply Chain Resiliency
With the last few years characterized by supply chain disruptions and increased political and logistical instability worldwide, the calculus has changed for risk managers and supply chain departments. The emphasis has been shifting from the lowest cost to the lowest risk and ensuring that operations can proceed as reliably as possible.
It’s hard to overstate the negative impact of not being able to make a deadline due to supplies getting tied up in production. Partners and resellers will need to adapt and could drop a business that they no longer feel like they can rely on, and customers whose expectations aren’t met will be similarly quick to find a replacement brand. That’s why reshoring is being looked at closely by so many businesses right now; with physically closer suppliers, there’s less likelihood that products or materials will be caught up in a dispute half a world away or caught up behind a blockage of trade routes like we saw with the 2021 incident in the Suez Canal.
It also means more control over the output (it’s easier to send a representative to regularly check in on production when it’s a few states away as opposed to half the world away) and fewer regulations to manage. With many countries introducing more regulations, in particular those intended to encourage more sustainable activity, compliance has been tougher than ever, and companies are relying on third-party partners to ensure they’re staying on the right side of all current and upcoming regulations.
Reshoring is being used to make it easier for companies to keep up with changing consumer demands and meet deadlines; resilient supply chains are a cornerstone of a company’s success. This strategy is picking up momentum—take China, for example. Long an incredibly popular option for cheap overseas manufacturing, many companies have either moved some of their manufacturing from China back to the US or plan to do so in the next few years. While individual company stability is a major driver here, national security and the US’ overall economic health also play a part, with tensions around trade between the two major countries at a high point in recent years.
According to a Kearney report, 96% of CEOs are seriously considering reshoring their operations—or have already done so or put plans in place for it. Compare that to 78% just a year before, and the trend toward reshoring is clear.
Risks and Complications of Reshoring
It’s no secret that in most countries, it tends to be more expensive to produce back home—that’s the whole driver for most outsourcing decisions in the first place. But the question has now become how much risk a company is willing to take in their current outsourcing environment and at what point does that risk outweigh cost savings? There’s certainly something to be said for the cost of a disruption to production or a delay in meeting customer demands even when a company is working with the cheapest suppliers possible; the cost of the former can quickly outweigh the benefits of the latter.
The actual act of reshoring presents some risk because of how expensive and disruptive it can be in the short term. When planning on a reshoring move, companies need to ensure they’ve accounted for the many important factors that are in play. The primary costs to account for in a move include the outright expenses of the relocation via lease selling, transport and other costs; setup costs associated with infrastructure and capital costs; increased labor costs related to the relocation; and regulatory and compliance costs since reshoring usually results in production to a more highly regulated region with more expensive costs relating to safety and environmental regulations.
While those are the main cost drivers, there are other factors to consider, including the lost revenue due to any disruptions in production or bringing the new facility up to speed, consumer and shareholder perception of the move, price differential (and all the complications that come along with changing the price of the end product offered to consumers, if that must be done) and more.
Production timelines are often pushed back as a result of reshoring, since the process is so involved. Companies need to source, assess, and approve new suppliers back home, and then onboard each. This is where you can see reshoring initiatives go awry: companies sometimes don’t dedicate enough time or resources to properly investigate and compare potential new suppliers to confirm that they can meet a certain level of quality and production quantity while also checking those suppliers for potential security, compliance, or data risks were they to come on board. This holds true for sub-suppliers as well.
Onboarding new suppliers properly needs to be accounted for in any overall reshoring plan, otherwise a company is opening itself up to a whole different group of risks. This is why many companies carefully screen all potential suppliers through third-party management platforms and other tools to make sure they have access to a diverse group of partners and suppliers that fit their business goals. Those tools also allow a company to establish a standard, thorough onboarding process that doesn’t leave anything out and keeps things moving according to schedule, in order to increase the chances of a successful reshoring initiative back home.
Reshoring in the Future
Right now, we’re seeing a major push toward reshoring that should extend for the foreseeable future, but that doesn’t mean all production will come back to the US soon. Rather, expect strategic reshoring, friend-shoring, and other changes—like multi-sourcing, which spreads out the risk among different suppliers and regions—depending on what a specific company needs.
In the end, it comes down to building agility and limiting rigidity in a supply chain. Businesses need to adopt flexible strategies that can adapt to an increasingly disruptive environment; they might need to pivot between reshoring, offshoring, or other strategies in a short time frame when looking at real-time data.
For some, a move today is risky due to recent inflation, but for others, it’s the best way to reduce risk elsewhere. Overall, expect more companies to fall in the latter camp; Goldman Sachs has reported that stocks of US companies who are involved in reshoring have been performing well. In fact, with tools enhancing the ability for digital automation in supply chains, we could see local operations close the gap with offshore production when it comes to cost. And as ESG regulations ramp up and the value of a sustainable and local supply chain grows, enabling circular economic models that emphasize recycling and reusing materials will be far more feasible when production is located close to home rather than overseas.
It’s worth noting that a careful and measured approach to reshoring is better than haphazardly burning bridges with international suppliers. Procurement teams have spent years or even decades, nurturing these relationships, and cutting ties abruptly isn’t recommended; after all, you might need them again in the future. A resilient supply chain is one that can plan for a multitude of different scenarios and periodically shift to adapt to current and future needs. In five or ten years, the most effective move might be shifting some production back overseas, after all. It’s good practice to keep these relationships healthy even when moving some production back home.
While reshoring focuses on bringing production back home to reduce risk, nothing done now is set in stone. By building adaptability and resilience into their supply chains, companies will be ready to not only take advantage of today’s move toward reshoring, but also effectively react to whatever unexpected scenario greets us in 2024, 2025 and well beyond.