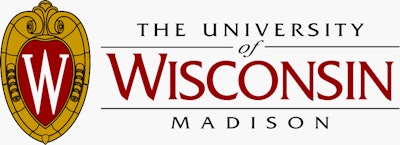
There may be huge demand for goods caused by severe weather or a natural disaster. It could be a spike driven by a product suddenly going viral.
Random demand surges represent a major challenge for supply chain managers, who are often well-equipped to deal with normal day-to-day or month-to-month variations in demand, but may not be ready for an unpredictable, yet substantial increase in demand in what had been a relatively stable environment.
Jordan Tong, assistant professor of operations and information management at the Wisconsin School of Business at the University of Wisconsin–Madison, along with Lu Huang of Google Inc., and Jing-Sheng Song of Duke University, challenge the notion that organizations are powerless to plan for these demand surges just because they are occur so randomly and are so difficult to predict.
The researchers created a model that identifies such factors as the frequency, duration, intensity and volatility of the surge. It then takes forecasts for those metrics (as well as confidence to predict each one) to determine how an organization should design its supply chain to best position itself to cope efficiently with random demand surges.
“It may seem counterintuitive to take an analytical approach to plan for something as random and unpredictable as demand surges,” says Tong of the Wisconsin School of Business. “But if firms carefully consider the characteristics of various types of surges that could occur and their likelihoods, they can still prepare for them systematically and intelligently.”
Tong adds, “Our research considers two key strategies for firms to employ in preparing for demand surges: having reactive capacity, the ability to ramp up production when needed and maintaining safety stock, an adequate inventory to deploy when a surge occurs.”
Firms can employ a combination of reactive capacity and safety stock. For example, a technology retailer the authors worked with not only holds extra machines in its own service centers (safety stock), but also compensates vendors to hold additional components so those vendors can quickly assembly the components into machines if needed (reactive capacity). Similarly, to prepare for disasters, humanitarian organizations maintain both safety stocks of key relief items at their own warehouses and contract with manufacturers for stand-by access to their production capacity should a disaster strike.
The researchers’ model helps organizations understand their own optimal supply chain planning strategy, while providing a general framework for managers and C-suite executives to think about the kinds of random surges their firms face and which strategies will be most appropriate in preparing for them.
The paper, “Supply Chain Planning for Random Demand Surges: Reactive Capacity and Safety Stock” was published by Manufacturing & Service Operations Management.