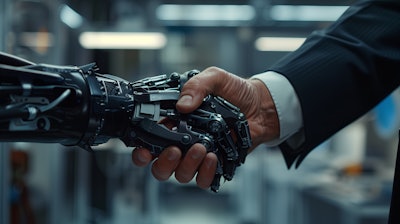
When we think about the fourth industrial revolution, it’s often through the lens of its foundational technologies — connectivity, cyberphysical systems like digital twin and simulation, and especially automation. But those tools are only useful because of the skilled manufacturing workers who use them.
In the early days of Industry 4.0, some manufacturers believed automation could serve as an electronic equivalent to humans. Those who instead maintained a people-centric approach proved the former to be a massive misconception.
People are necessary in manufacturing. Technology is complementary, not a competitor, as not everything can or should be automated. Automation is a tool that enhances human capabilities, aiding, guiding, and supporting human workers to make their work easier — not replacing them.
Building synergy between humans and machines is crucial for a successful digital factory and delivering cutting-edge solutions to customers. Effective human-machine interaction can reduce waste and create efficiencies through cost reductions, accelerated ramp times via automated processes and simply doing things the right way the first time thanks to high-quality simulation.
Here are four steps manufacturers can take to create a harmonious environment for human-machine collaboration.
1. Reframe perceptions of technology.
One of the biggest challenges manufacturers face when implementing new technology, particularly automation, is negative perceptions. Clearly communicating the opportunity that technology presents for workers is key to overcoming this hurdle.
As a general rule of thumb, automation should be used to replace tasks that are dangerous, simple or repetitive, while humans focus on items that require flexibility and creativity. It creates a safer workplace and can lead to opportunities for upskilling, new roles, and enhanced job satisfaction; the onus is on employers to communicate these benefits to their workforce.
It’s understandable that shopfloor employees might fear a new tool or software that seems to do the same thing they would do during their shift. However, leadership must show those employees that they now have the chance to upskill. If their station is automated, they can learn how to fix, program and implement the robot across the factory, elevating their role from an operator to a technician.
This type of cross-training also gives employees flexibility in their skill set, allowing them to move to different roles or even different facilities to pursue their personal development goals and the needs of customers. Providing employees with this training is the next step in making a human-centered digital factory work effectively.
2. Upskill workers to support complex tools and tasks.
Manufacturers can’t make the same widget forever; they must respond to human-driven changes in demand. It follows that machines and digital tools cannot autonomously adapt to shifts in customer needs without input from other humans.
Upskilled talent is necessary to continuously maintain, optimize and improve manufacturing technology according to market changes. However, training on modern tools and software is typically available only on the factory floor.
It’s crucial that employers provide on-the-job experience and learning opportunities for employees to develop their skills. They must make that training widely accessible, even for those who might be less tech-savvy. By the same token, manufacturers should be strategic about the tools and software they choose to invest in. Technologies that are flexible, simple to learn and used across multiple areas of the factory will make upskilling significant portions of the workforce much easier.
Additionally, employers might consider looking outside their four walls. Collaborating with local schools and universities to provide tours, give guest lectures, or even develop curriculum based around necessary real-world skills can help manufacturers better prepare the next generation of manufacturing talent in their own backyard.
3. Ensure factory workers are data-literate.
One of the most important areas of upskilling for anyone working in manufacturing today is data literacy. For knowledge workers supporting frontline manufacturing, this also includes computer literacy, an understanding of the connections between software and hardware and the ability to work with large, complex systems.
For employees on the floor, their primary role is data capture. These employees have the critical responsibility of ensuring they collect complete and accurate data — scanning when they need to scan, following proper nomenclature when uploading information — to help leadership make informed decisions and process improvements.
Once again, how employers communicate the opportunities associated with data literacy is key. Accurate data can diagnose, reduce or even eliminate operational challenges; it also helps identify which tasks are dangerous, repetitive, or overly simple. Armed with that information, leadership can identify where automation is appropriate so employees can be reassigned to more engaging, enjoyable tasks.
Giving employees on the floor the “why” and not just the “what” and “how” of data collection will help them connect the dots between everything described so far — from automation and other technologies to the training they receive. Making these links, however, starts with the technological vision set from the top.
4. Create alignment on the automation strategy from leadership through the organization.
It is critical that leadership, from the C-suite down, understands the role automation and other manufacturing technologies play in their organization. Automation and the training needed to use it properly is an investment. It must be able to shift and changes in response to market demands; it’s not “set it and forget it.”
By developing a culture of accurate data collection, optimized processes and streamlined operations, leadership creates an environment where technology is useful for meeting their goals — cost reductions, accelerated ramps and improved quality.
Having this clear direction from the top can then help management place the right people in the right roles at the right time to align with the organization's technological vision —enabling a more successful integration of technology with a skilled workforce.
It’s become clear that manufacturers can’t advance on digitalization without the people to make it happen. Workers are the connecting link between technology and a company’s financial success. While technology might open the door to new capabilities and skills, manufacturing is still a people business.