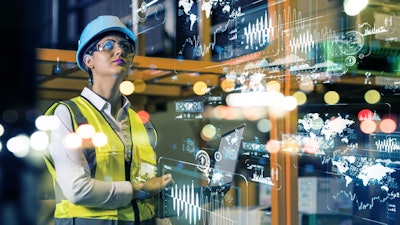
Following the global electronics value chain's hard re-set, leading indicators from a recent survey published by the Electronic Components Industry Association (ECIA) show signs the industry is gradually stabilizing and making small improvements. According to the Institute for Supply Management (ISM), June 2020 Manufacturing ISM Report On Business, the computer and electronic product sector was one of 13 industries reporting growth in June and one of 11 seeing growth in new orders. Seven of the 11 leading indicators on the ISM's Manufacturing at a Glance, June 2020 dashboard are trending positive.
However, electronics suppliers, distributors and manufacturers are seeing fluctuating lead times and shifting allocations for many popular components that are challenging assumptions of risk in bill of materials (BOM) and new product introductions across multiple downstream industries, including high tech, automotive, medical devices, consumer durables and industrial equipment.
Unlocking the value in BOM component lead times
Marcus Aurelius, the Roman emperor and philosopher wrote “the impediment to action advances action. What stands in the way becomes the way." He perceived that the data and insight that constraints provide often actually hold the answers for overcoming them. Back in the late nineties, Dr. Eliyahu M. Goldratt's book, “The Goal,” showed how focusing on constraints offers valuable insights to achieve improved total process throughput to any system, particularly manufacturing plants and supply chain networks. Many of the key points are directly applicable to overcoming continuity of supply and component lead time obstacles during these uncertain times.
One of the more fascinating areas of innovation today with regard to reducing risk to improve component lead times is the application of artificial intelligence (AI) and machine learning (ML) methods to differentiate between random and systematic variation in component demand and lead times. ML techniques can unlock the most valuable data in any lead time constraint. Removing the randomness from component lead times and knowing what factors make them fluctuate, then risk scoring them, are key to turning any component lead time constraint into an actionable insight. AI and ML methods have the potential to dramatically improve risk assessment of BOMs in early design phases, and improve the overall product margin and time to market for new products. The electronics industry’s hard economic reset caused by the pandemic has accelerated adoption of AI and ML methods in this area.
Taking the following actions to improve component lead times is a great way to get started:
● Strive to build a collaborative working relationship that benefits suppliers equally across your entire supply chain. Creating sourcing programs that are balanced, fair, and allow every supplier to earn more business and margin, especially on new products, is key. The stronger the collaborative relationship you have with suppliers, the lower the potential commercial risk. Providing frequent forecasting updates so they're current on the sales and production schedules and have long-term visibility into order plans is critical to alignment. For new product introductions, share the launch schedule, forecasts, and BOM requirements now and in future product upgrades. Also ask for guidance on any potential component lead time challenges. The goal is to have suppliers become partners in the success of every existing and new product. Providing a series of smaller, more consistent component orders keeps suppliers engaged with your business. Also, consider diversifying your suppliers, so you'll have recourse in the event of a spike in lead times. Negotiating quotes with suppliers can also open up opportunities to reduce lead times if you need a rush order to get your product to market faster than the competition.
● From initial prototype through production, design with long lead time component constraints in mind. Researching which components are the most and least risky from a lead time standpoint is becoming commonplace. Collaborating with manufacturers early in the design process and asking for their insights into how design for manufacture can be improved is an effective strategy. Suppliers are providing insights into the reliability of components and their availability to support a ramp to volume plan.
● Resiliency at the point of design is a key goal. Product designers are concentrating on adding greater adaptability and flexibility to product designs in response to longer and often more uncertain component lead times. The first BOM created for any new product needs to have multiple alternative suppliers and equivalent parts available. Designing resiliency into a BOM gives engineers, sourcing, and supply chain managers the flexibility of transitioning from one supplier to another quickly.
● Consider sourcing directly from factories of suppliers with which you've built strong, collaborative relationships. Asking if your orders can be added to other customers' larger orders is proving effective for reducing component lead times. This gives you immediate visibility into when your order will be produced and shipped, and the availability of components that are otherwise on allocation through distribution. The downside is that you will have to wait for the larger orders. Despite the potential time lag, factories often get better allocations in times of scarcity of raw materials for electronic components. But ,you'll have to pay the supplier to stockpile your components if you don't take delivery once they're produced.
● Partner with electronics distributors, making use of their vendor managed inventory (VMI) services to reduce risk, and rely on their purchasing power for in-demand components. The largest electronics distributors have the purchasing power to buy in-demand components in bulk, inventorying them across their network of warehouses globally. The combination of the scale to procure components and VMI services makes distributors a viable alternative for reducing component lead times.
Designing next-generation products that are resilient, adaptive, and scalable is the future of electronic components sourcing and intelligent design. Knowing which components have the longest lead times and devising strategies for bypassing or overcoming these constraints as early as possible is critical to downstream performance.
The five approaches listed above can help designers, engineers, supply managers, and sourcing professionals to see beyond the immediate challenge of component availability to deliver a unique product. Applying AI and ML methods to solve component lead time constraints is a fascinating arena of innovation, as is developing more real time and comprehensive risk scores for products during new product introduction.