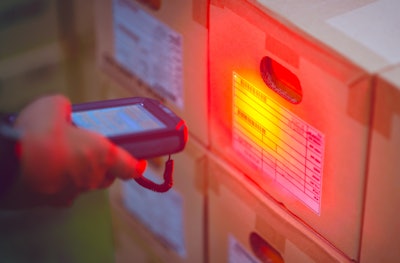
Higher returns go hand in hand with the holiday season and this increasingly affects Q1, right into March, for an even more drawn out holiday hangover.
This is especially true for progressive retailers and burgeoning e-commerce and DTC operations, with returns accounting for up to 10% of the business. In the United States approaching $500 billion worth of goods were returned last year say analysts - and while around 8-10% were for bricks-and-mortar purchases, that figure more than triples to a whopping average of 30% for online sales.
So, if you’re looking to revamp your DC processes to drive faster fulfillment, don’t forget that an efficient returns process is just as important in driving a better customer experience. Even for giants like Amazon, their millions of deliveries are only possible with a clear set of rules and advanced warehouse technology to guide returns.
Here’s how you can master reverse logistics and make the process count toward your bottom line during peak periods and beyond.
Work from the Ground Up
Speed, efficiency and organization are key factors in deploying successful and profitable returns processes. But your warehouse team shouldn’t shoulder the responsibility alone.
Reverse logistics is a strategic process that should be evaluated and deployed across all functions, from sales and finance to customer service and operations. Through collaboration across these groups you can determine which returns model is best for your business.
If you choose to manage returns in-house, work with your operations team to streamline processes and optimize layout. Achieving efficiency requires a better understanding of your pain points and performing a weekly productivity analysis can help you make the most of your resources.
Evaluate every step from unloading to restocking and determine how long it takes you to sort goods, calculate resale value and move the item to its final destination. This data can serve as a foundation when you set goals for improvement - i.e. sort stock 10% faster.
If you’ve completed a productivity analysis but would like to dig deeper into your data, a, leading edge warehouse management system (WMS) like SnapFulfil can help you understand where and how to organize your warehouse layout to ensure optimized processes - including reverse logistics. By providing insight into what was returned, why it was returned and whether it can be resold, a Tier 1 WMS enables a more streamlined returns process while helping you evaluate your best options for returned inventory.
Click here to hear more about technology in the warehouse:
Develop Clear Policies
To enhance returns performance, you’ll need to implement a realistic set of warehouse procedures to ensure your team can manage return volume without getting overwhelmed.
Start by speaking with your fulfillment center's frontline employees. They see the returned inventory, identify fraudulent returns and missing product components and make judgment calls regarding resell value. Tap into their experience to develop a logical returns strategy. By implementing a clear flow for returned goods you can help your operations team avoid inaccuracy, inefficiency and ultimately lost profits because of unclear procedures.
Once you’ve determined your optimal reverse logistics strategy, a highly flexible and configurable WMS will also help you maintain and develop the required new process rules. You’ll ease the burden on your returns team and simplify product storage procedures.
Logical, streamlined processes will also help you to keep up with demand and effectively recover the cost of returned products.
Measure to Improve
While you may not be able to master reverse logistics overnight, you can adopt a more strategic approach on technology for measuring current processes and identifying areas to improve. Each phase of the returns process must be analyzed and enhanced to drive optimal efficiency.
By evaluating current state, collaborating across the fulfillment center to develop a better strategy, and maximizing operations and implementing effective policies, your team can perform at the highest levels of productivity and optimization. Plus, you’ll quickly decrease profit loss from returns.
In these extraordinary times it’s never been more important to capture the maximum value from goods sold during peak periods by implementing a cost-effective and dynamic returns operation. Cloud-based WMS also facilitates much easier integration with other company systems like transportation management systems (TMS) - for reliable and consistent movement of goods and optimized transport operations, plus hauler activity and loading that’s also automated via the WMS - to facilitate a holistic reverse logistics operation.
The net result should be a significant increase in customer satisfaction and recovery value from returns – both leading to a much healthier bottom line.
What can be a cumbersome, manually controlled process is made both simple and speedy when automating the operation with a technologically advanced WMS featuring targeted return management functionality. It facilitates clever tracking and material flow processes, which can fully optimize the returns procedure from the dock to final dispositioning.
Such software will also provide a more accurate, efficient and consistent way of tracing returned products through the warehouse.