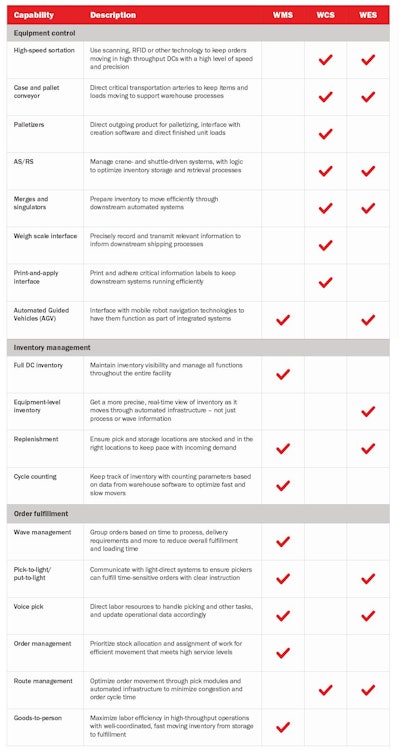
WMS. WCS. WES. Let’s face it, the industry faces a W_S acronym overload—to the point even the most seasoned warehouse professionals can find the software market a confusing scene.
After all, the lines that separate each system continue to blur and crossover in one way or another. Some warehouse management solutions (WMS) try to bridge the gap to and provide warehouse control system (WCS) performance, while many WCS offerings now offer inventory management and other functionality in an effort to occupy the role of a WMS. Then there’s the latest entrant – warehouse execution systems (WES), which aims to be a true hybrid of WMS and WCS. But, what does that really mean for operations looking to make the right investment?
Let’s examine the established software paradigm for warehouses and distribution centers and weigh an alternative approach - a modular package, customized according to the functions required by unique, high-performance operations.
Defining the labels: WMS, WCS and WES
To grasp the potential of a fresh approach to warehouse software, it’s important to first understand the landscape.
A WMS is an application that controls inventory flow into, within and out of distribution centers and warehouses. The WMS ensures that inventory, orders and employee responsibilities are cohesively managed from the moment products enter the facility, to the when they ship.
A WCS manages automated equipment like automated storage retrieval systems (AS/RS), conveyors and sorters, and the flow of individual items, cases and pallets that travel on them. The WCS sits between the automated equipment and the WMS. It determines the most efficient ways to route materials through automated equipment, can re-optimize order paths as business conditions change and even send updates to keep the WMS informed or report a routing error.
Then there’s a new kid on the block – WES -- which takes the approach of manufacturing execution systems, controlling multiple elements of the production process and making adjustments based on real-time conditions to improve output and applies it to warehouses and distribution centers. WES combines equipment control of WCS with some of the functionality of a WMS, such as basic receiving, replenishment, parcel manifesting and pick management, but no order management, wave management or slotting capability.
Limitations of the W_S acronym world
This partnership between WMS and WCS has been standard operating procedure for automated order fulfillment operations for many years. But, today’s supply chains operate faster than ever to serve the demands of e-commerce. The problem with the existing WMS-WCS paradigm is that the virtual handshakes between different software layers do not enable the agility and adaptability necessary to direct orders, labor and automation to meet the moving targets of e-commerce at great speed.
Additionally, there is no “one-size-fits-all” solution. Some facilities may not be automated, so they only require WMS, while others may be highly automated, thereby relying heavily on WCS or WES. The integration of WMS, WCS and now WES varies so often from one warehouse to the next, that it is virtually impossible to determine how, when and where the systems should be assimilated.
Instead, simply consider the software modules necessary to fit business requirements.
Understand the building blocks
What are common warehouse software capabilities that facilities must consider to meet business requirements? The first step to breaking through the various labels is to look at what software in the warehouse actually does.
The chart below lists common warehouse software functions for equipment control, inventory management and order fulfillment, along with the platform on which they typically reside. With such variability between systems that go to market under the same label, keep in mind that the designations are an approximation.
MHS
Breaking out of software silos
Warehouses and distribution centers now have the choice to break out of these established W_S silos, accessing a wide range of modules running on a single software platform, designed to work together in any number of configurations to fit what each individual operation needs. Such consolidation can improve overall control, resulting in greater efficiency, flexibility, visibility and precision.
Consolidating such broad functionality onto a single platform requires no integrations and digital handshakes, enabling the agility that modern e-commerce-driven supply chains require.
Warehouse software based on function
The old software paradigm goes from the outside-in, applying established W_S solutions to fit operations, oftentimes with complex integrations and crooked roads to scalability.
But, today, businesses can take a more open-ended approach that builds a balanced, best-fit package of capabilities around their operation. A lean package of powerful modules that puts the end user in control to define necessary functionality, with the ability to easily scale and change as business dictates.
Keep an eye on tomorrow
As businesses grow, their supply chain infrastructure must adapt. For example, while operators roaming pick aisle with pick lists may work in the near term, new workflows like goods-to-person fulfillment and technologies like voice and lights may be appropriate as growth dictates.
Warehouse software should be able to scale with the business, handling the necessary changes to processes and technology without costly new platforms or complex reconfigurations.