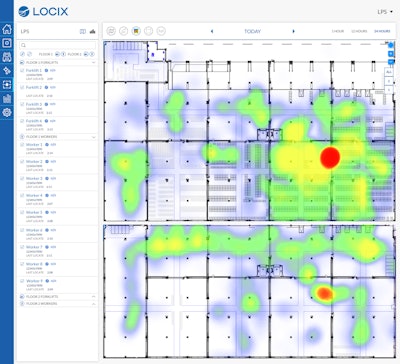
When warehouse management systems (WMS) were introduced in 1975 by J.C. Penney, it was a game-changer that improved inventory accuracy, alleviated human error and allowed more time to focus on business growth. Since then, the industry has continued to improve WMS, but has struggled to adopt new technologies to enhance operations.
According to Gartner, more than 80% of supply chain professionals feel that they could be making better decisions in response to disruptive events. The tools in use today are proving to be insufficient. Supply chains must have real-time operational data and prescriptive analytics to keep up with the inexorable demand for faster execution, rising costs and significant labor constraints confronting the industry.
While WMS has improved operations, it can only take warehouses so far. Today’s WMS’ lack real-time data and spatial context required to meet ever-increasing demand and do not provide operators and managers with the necessary insight and analytics, such as where assets and workers are precisely located in the warehouse at any given time and how tasks are actually executed. Additionally, this real-time and spatial context is critical as operators maximize productivity while improving labor conditions and worker safety.
As a new category of software solutions, warehouse spatial intelligence (WSI) has emerged to address these urgent warehousing needs. WSI solutions bridge the data gap between the WMS and the “real world” by providing real-time operational visibility, spatial context and analytics — helping to streamline efforts in the warehouse — and inherently maximizing productivity, efficiency and safety.
This new spatiotemporal approach combines unique spatial and real-time data (precise indoor location and HD images and videos via advanced sensors) with groundbreaking cloud-based analytics to gain actionable insights and make data-driven process changes. WSI solutions have been demonstrated to help improve real-time operational visibility, enabling logistics and warehouse operators to increase worker productivity, asset utilization and safety.
WSI solutions can be leveraged as a stand-alone deployment or integrated with a current WMS, transportation management system (TMS), logistics management system (LMS), Internet of Things (IoT) and enterprise resource planning (ERP) software applications via open APIs to extend and enhance the entire value proposition, creating a unifying layer on top of siloed data.
The commoditization of battery-operated wireless sensors, HD cameras and cloud-based artificial intelligence (AI)/machine learning (ML)-based analytics has made the deployment and use of WSI solutions cost-effective, easy to deploy and highly scalable – capable of achieving high ROI and instant returns for company executives, warehouse managers and operators.
The ease of integration allows operators to analyze massive amounts of data without the need for changes to their current software systems. Unlike traditional approaches that leverage periodic and batch-level data analytics, WSI solutions allow data to be captured and analyzed in real-time. Additionally, WSI systems can be used by operators to gain operational visibility concurrently across all their facilities, helping to improve forecasting and strategic planning.
By supplying an extra layer of spatial context to a WMS, the following are some of the representative benefits that WSI-based solutions can bring to logistics and warehouses.
Workforce optimization and safety
Labor cost is the highest overall operating cost of a warehouse; as such, ensuring that the workforce is properly optimized is key. Given WSI can precisely locate and track workers with a precision of tens of centimeters in real-time, operators can accurately measure and improve overall warehouse efficiency by monitoring KPIs such as travel time and distance traveled per worker. In a recent case study, it was found that WSI solutions reduced worker walking distance by over 30% and increased worker picking efficiency by 25%.
WSI’s real-time location data and heat maps offer detailed congestion analysis, allowing operators to optimize warehouse layout, which helps to improve movement within the warehouse and avoid collisions and other safety concerns. Additionally, WSI can be integrated with forklifts to assess and improve driver behavior and set up alerts to prevent unsafe forklift and worker interactions. In a recent case study, it was found that WSI solutions reduced potential unsafe worker and forklift interactions by up to 50% while increasing worker productivity by 11% during peak pick periods.
By integrating WSI with WMS, the workforce will see improvements in slotting, labor scheduling, safety, productivity and inventory placement.
Space utilization and asset usage
As warehouses and distribution centers move into urban locations for e-commerce purposes, the spaces get smaller, yet the demand continues to increase. In these locations, there is significant emphasis on space utilization and increased warehouse efficiency. WSI solutions can generate precise aisle and shelf-level heat maps that can optimize warehouse layouts, reduce aisle widths and drive better space utilization. When WSI pulls time-based activity analysis it provides insight into how to improve resource allocation and can be utilized to precisely locate and track forklifts, assets and other material handling equipment.
While WMS provides insight into tasks performed, when paired with WSI – it provides guidance and an understanding of what is actually happening in the warehouse.
Loading dock efficiency
In the United States alone, dock inefficiency and extended dwell time can cost warehouse and distribution centers upwards of $40 billion a year. Even the smallest bottleneck at a loading dock is costly and demands the attention of the workforce – ultimately causing a domino effect of problems including delays, detention fees and increased shipping costs.
Integration of WSI with WMS helps warehouse operators to better predict truck arrival and departure times across the facility – allowing for renegotiated shipping contracts and reduced costs through tighter dwell time limits. Additionally, WSI can be integrated with truck appointment and scheduling applications, as well as to accurately track the arrival of trucks to the warehouse. With WSI, operators can improve loading dock efficiency by as much as 30%.
The future of WSI
As the industry evolves, there will be an increase in the number of automated material handling equipment (MHE) that will be deployed within warehouses, including automated storage retrieval systems (AS/RS), cobots and automated guided vehicles (AGVs). Current warehouses will evolve from the current “four walls and a roof” to becoming fully connected with advanced analytics capabilities preconfigured so that operators can move in and start leveraging the added capabilities immediately. Building a connected warehouse that allows automated devices to easily interact with workers and legacy MHE will be critical for most operations.
WSI solutions can play a key role in integrating the real-time location of workers, legacy material handling and new automated MHE for seamless interoperability. New versions of wireless connectivity, including Wi-Fi, 5G and IoT will accelerate the integration of WSI into these connected warehouses, enabling the realization of a truly smart warehouse.
Changing, or even upgrading, a WMS is a huge time and financial investment that carries significant operational risks, but inefficient warehouses and loading docks can be even more costly in the long run. With WSI solutions’ ability to consume existing WMS and WSI data, warehouse operators get cutting-edge analytics and analysis that enables them to enhance operational productivity in a cost-effective, highly scalable and easily deployable manner. Warehouses leveraging WSI solutions now have access to real-time operational data and prescriptive analytics to keep up with demand, provide actionable insight into operations and address the significant labor challenges facing the industry.