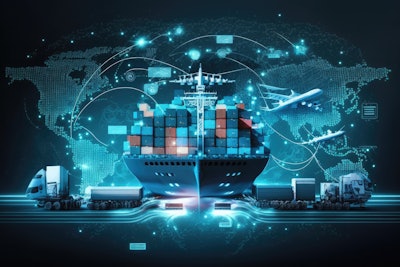
Supply chains have rarely been in the spotlight so much as over the past three years. The pandemic created historic supply shortages and severe demand swings, then just as things seemed to be reaching a new normal inflation and the war in Ukraine disrupted operations again.
As McKinsey notes, supply chain leaders now have “the attention of top management and a mandate to make real change.” After decades of relative stability in global trade, manufacturers can no longer assume that calm waters will return soso supply chain leaders must find ways to economically increase resilience and agility in their supply networks moving forward.
Achieving this requires greater visibility up and down the supply chain, with the ability to anticipate disruption and take the right steps quickly to mitigate its impact. Less than half of companies understand the location of their tier-one suppliers and the risks those suppliers face, McKinsey says, and visibility of visibility of suppliers beyond the second tier that figure is just 2%.
Data has transformed much of the business world, but supply chains have been slower to digitize. To achieve a holistic view of their supply networks and be able to react in the smartest, most cost-efficient way possible, supply chain leaders must make more data-driven decisions based on complete and timely information.
Here are five ways supply chain leaders can put data to work to build greater resiliency in the face of continued disruption and uncertainty.
Smarter shipping and transportation decisions
The most innovative manufacturers are using real-time data to spot potential bottlenecks and react accordingly, choosing alternative shipping routes and shipping modes based on the most reliable and cost-effective option at any given time. Shipping data experts forecast where delays are likely to occur so that organizations can take preventative steps where the greatest risk is present.
With severe weather events more common, data from sources like AccuWeather can help organizations stay ahead of delays caused by typhoons, floods and other events. Ideally, all of these data sources are combined with operational data, allowing for better decisions about how and where to move goods to minimize both risk and cost.
Connect siloed ERP systems
Many manufacturers have expanded globally via acquisitions, leading to siloed ERP and other IT systems that make it hard to gain a centralized view of what’s happening across the network in a timely fashion. Often, reports on inventory and other metrics at regional plants and transport hubs are delivered weekly or monthly, making it impossible to glean timely intelligence to maximize efficiency.
Digitally savvy manufacturers are bringing these streams of ERP data together in the cloud with high refresh rates that provide faster views of operations. Here, this ERP data can be combined with operational and third-party data to build a 360-degree view of the supply chain, surrounding market and environmental conditions, allowing for more accurate planning and mitigation strategies.
Having visibility across all ERP systems also enables improved spend analytics, including benchmarking prices and consolidating supplier purchases to improve buying power. Access to real-time inventory data across the network also helps teams to manage replenishment more closely.
Getting smarter about energy and raw material costs
One of the biggest challenges of the past year has been wildly fluctuating energy costs caused largely by the conflict in Ukraine. While this has stabilized somewhat, the future remains highly uncertain.
To address this, data providers provide data on current and future oil, gas and electricity costs in real time across different regions. These insights help navigate commodity purchases and negotiate prices, while predictive models help with longer term decisions for energy sourcing, plant locations and transportation. decisions such as where to locate new plants or add capacity.
Raw material costs have also been in flux, impacting everything from chips to steel, and data sets can provide predictive insights about commodity and material prices, allowing manufacturers to stay ahead of the market with dynamic pricing and timely purchase contracts.
Monitoring for supply risks such as factory fires, power outages, labor strikes and litigation is also a critical factor in maintaining resiliency.
Enrich demand forecasts with macro data
There's only so much predictability you can build into a supply chain, but companies that perform best tend to be those that maximize their ability to more accurately forecast demand. That means having the right indicators and applying machine learning to enable sophisticated predictive analytics.
Dozens of governmental and non-governmental organizations provide data that allow companies to track market trends regionally and globally. Datasets from these providers that help predict demand include consumer spending insights, economic outlooks, inflation rates and unemployment trends.
Improve product quality and output with smart manufacturing
Supply chain resiliency comes not only from better visibility and communication with partners, but also from maximizing yield and increasing the predictability of production. Even the best performing supply chain can't overcome production inconsistencies. Variance in factory cycle times and product yield can lead to late orders even if all raw materials are in full stock.
Combining the intelligence that comes from ERP systems with shop floor data -- the convergence of IT and OT -- allows manufacturers to better manage predictability of factory performance and yields. Having greater predictability into product yields allows for more accurate predictions of production output, which in turn means reliable fulfillment of customer orders while right-sizing inventories.
Many of these shop-floor systems have yet to be connected to the wider business for security and other reasons, but the benefits of connectivity and maturity of cloud security means the opportunity for greater efficiency and visibility now outweighs many of those concerns.
A more resilient, adaptable future
Supply chain leaders can’t afford to assume that the world will stabilize any time soon. Organizations that thrive will be those who can spot challenges before they arise and adapt quickly. This depends on understanding the economic, geopolitical and environmental changes happening in their supply chains, and having the visibility to make the best decisions about how and where to adjust production, supply and logistics. Making full use of all available data is key to improving visibility and maximizing agility.