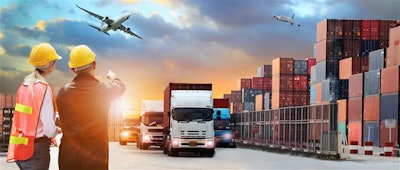
Supply chain disruption didn’t start during the pandemic; COVID-19 just revealed all the cracks in the cycle. As a result, companies and suppliers are actively innovating in an effort to figure out how to improve supply chain strategies.
It hasn’t been easy, of course. Raw material shortages, rising shipping costs, and other factors make it challenging to implement viable supply chain solutions. Despite these obstacles, businesses worldwide are testing the waters with a variety of strategies — and they’re making positive waves.
For instance, many companies are reshoring or adding new distribution centers. Port congestion has been an issue for years, especially along the East and West Coasts. Not being able to access raw products, talent, and global distribution sets the stage for friction, frustration, and delays. Relocating a business to an area with better accessibility to interstates, airports, railways, and other infrastructure makes it possible to move products quickly. As noted in Thomas’ 2021 “State of North American Manufacturing Report,” 83% of manufacturers say they’re likely going to reshore.
General Motors recently announced reshoring initiatives. As freight bills increase and shipping delays lengthen, the company will pour $7 billion into four electric vehicle manufacturing facilities in Michigan. This decision will help GM minimize the time its products are in transit and provide an additional 4,000 jobs in the state. Ultimately, GM has chosen to reshore for the supply chain resiliency it offers: Many U.S. companies have found that keeping processes closer to home provides more security against disruptions in the supply chain.
That said, business relocation and expansion aren’t to be taken lightly. Finding the right site is essential. That’s why Chewy took its time before opening a distribution center in Belton, Missouri, at the start of the pandemic. The online pet retailer needed a strategic location to meet growing demand, and the decision proved to be the right one when lockdowns occurred and people turned to online vendors for items they — and their pets — needed.
Solving ongoing supply chain issues
The end game is the same for all businesses: Stay ahead of disruptions in the supply chain. There’s no perfect way to deal with the sourcing, distribution, and other problems happening today, and reshoring initiatives might not be right for all cases. Fortunately, companies have other ways to tackle modern supply chain issues. Here are five strategies that leaders can implement:
1. Consider multiple facilities.
As mentioned above, opening centrally located distribution centers helps transfer products from warehouses to customers swiftly. Expansion also has another benefit: It spreads out companies’ workforces, making it easier to stay in business if a location must shut down due to a situation like another pandemic.
Deciding where to expand can be tricky. Manufacturers typically look for places that have attractive mixes of updated infrastructure and ready labor. Opening multiple distribution centers costs money at the outset, but they can pay for themselves in lowered transportation fees and improved inventories. This strategy can even showcase a company’s commitment to sustainability by reducing the carbon emissions needed to move materials or items from place to place.
2. Look inward for areas of improvement.
Making changes on a micro level can have a macro effect. Businesses can often make an impact on their supply chains by rethinking workflows. This requires a deep dive into all parts of a company’s supply chain to spot areas that could be adjusted or corrected. Once leaders pinpoint those areas, they can brainstorm and implement new strategies.
For instance, some processes can hold up operations unnecessarily. If those processes can be reworked, companies might smooth out upstream or downstream supply chain disruptions. The key is to get creative and stay open to new concepts.
3. Embrace supply chain diversification.
Having a single supply chain can lock down a company and make it hard to pivot. Diversifying supply chain frameworks reduces risks by leveraging a healthier geographical spread and accessibility to ample raw materials.
To diversify their supply chains, leaders should understand the full breadth of possibilities along the chain. They should also investigate alternative materials or sources that could be used to generate products that will satisfy end users’ needs and expectations. Quality, capacity, and added costs should be taken into consideration when mapping out more diverse, widespread supply chains.
4. Invest in emerging supply chain technology.
The future of the supply chain is intertwined with the future of technology. Many programs and systems can help leaders tighten their supply chains and better understand the entire process. For example, some manufacturers are using “digital twin” technology. This type of technology allows companies to use virtualization to test supply chain scenarios against a baseline and each other.
Ultimately, technological advancements, such as digital twins and artificial intelligence-enhanced data parsing, will be integral for finding strengths and weaknesses in supply chains. Additionally, they’ll promote unparalleled visibility, speed, and scalability.
Many supply chains are broken, but not irreversibly so. With a little bit of innovative future-proofing, leaders can overcome today’s — and tomorrow’s — distribution disruptions.