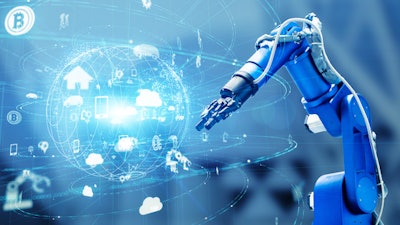
Over the past two years, we have seen considerable changes in how consumers behave, what they expect and how they make decisions in the marketplace. Companies have had to adapt on the fly when it comes to supply and demand.
As we head into a New Year, here are six themes to expect in 2022:
Continuous assessment of workforce strategies
Many companies have remained comfortable operating for years with legacy systems. The global pandemic accelerated the adoption of automated systems to maintain reliable and consistent supply chain operations. Companies slow to adopt new technologies fall quickly behind their competitors. Many businesses are already playing catchup from the impact of the Coronavirus disease (COVID-19), both with their own business and amongst their competitors.
In the wake of COVID-19, companies experienced booming volume while needing to operate with a lean staff due to social distancing for the health and safety of their teams. End-consumers and industry workers relied on the supply chain more than ever before, albeit for household necessities or to keep their jobs.
While inbound goods and transportation are vital to the process, these bottlenecks are only the beginning. We have not even addressed the most hands-on component of the supply chain yet; sortation. As COVID-19 forced companies to pivot from typical work structures and companies adapted to remote work or set up warehouse workspaces for social distancing, the warehouse presented a unique challenge. Social distancing can be difficult in warehouse sortation facilities. Manual sortation and piece-picking are very high-touch, and employees are working shoulder to shoulder to move packages through the building.
Implementing automation allowed companies to maintain full-time teams with less reliance on temp workers, while ensuring social distancing among existing warehouse tasks. Automated sorting solutions are equipping warehouse workers to more than double their throughput per hour, safely. Additionally, working with artificial intelligence (AI) systems helps to upskill warehouse associates who want to manage and operate advanced technologies.
Resiliency that starts within
Building resiliency is focused primarily on people. Leaders, employees and customers need to feel confident in the organization’s future. Here are two key ways to build resiliency within the workplace.
Prepare leaders at all levels. With the quick advancement of technology in the workplace in response to COVID-19, businesses must have buy-in from all levels of the organization when implementing change. Every aspect of the business will be impacted if a decision is made at the top but those who lead the boots on the ground are confused about the “how” and “why.” Develop a plan, identify key stakeholders and provide transparency. Communication is key, as well as educating on new technologies where applicable.
Focus on the customer’s needs. Supply chains need to scale at the pace of changing consumer behavior. Needless to say, in the past two years, we have seen consumer behavior change at an incredible rate. Legacy systems did the job when e-commerce was a supplemental experience to brick and mortar, but now consumers do a majority of their shopping and consumption online. The only way for brands to meet the demand is to adopt new technologies designed for our new reality and automate where they can.
Real-time visibility will be paramount
Gartner reports the cost of downtime can be upwards of $300,000 per hour. Real-time visibility with warehouse management software and automation helps companies see trends before they become problems and identify opportunities to lower costs, increase throughput and upskill employees.
Automation helps companies free up time to focus on more important tasks. With automated systems augmenting the monotonous and repetitive tasks, the human workforce can focus on more complex activities and contribute to innovative solutions in the warehouse. When teams are free to focus on value-added, rewarding and stimulating tasks, associates feel valued and challenged, which increases productivity, retention and performance.
3PL integrations will be essential for optimization
Companies will seek third-party logistics (3PL) companies to reduce costs and optimize their supply chains. Here are three things to consider when selecting your 3PL partner:
- Aptitude. Understand whether your 3PL partner can handle your unique, ever-changing needs. Do your homework to ensure this provider can easily integrate with existing platforms and technologies throughout your operations.
- Customer service. The supply chain moves fast, and one issue can have a ripple effect throughout your operations. The right partner will provide excellent service and the attention you deserve to proactively identify issues and effortlessly resolve problems. Businesses need full transparency into cost reductions, traceability, trackability and delivery timing.
- Scalability. Organizations need to be able to grow with their partners and vice versa. Multi-channel capacity and seamless integrations with customized solutions to meet the unique needs of a business should always be top of mind.
Reverse logistics will create return customers
People are buying online more than ever, so what are the ramifications to the business when the customer, or many customers, needs to make a return?
A seamless return process is vital to customer satisfaction and can drive growth when customers have good experiences. The return process should be as seamless as ordering the product. With an effortless process, businesses can retain customers who are familiar with the brand. With an effortless shopping and return experience, they are more likely to be confident (and loyal) when they are ready to order from you again.
Last-mile innovation investments
A 2020 Pew Research Center survey revealed that 91% of respondents share a favorable view of the USPS. E-commerce customers have become accustomed to faster deliveries than ever before and want real-time visibility into the status of their packages. Postal operators are focusing on increasing efficiency for sorting and routing orders to their final destination while reducing operating expenses to save both the customer and business money.
With parcel volume growing 27% in just one year, we are expecting the busiest and most extended peak holiday shopping season yet where there are more open warehouse positions than ever before. Supply chain demand is growing due to a shift in consumer behavior to online shopping, inspired by health and safety concerns associated with COVID-19.
Retailers and global e-commerce brands are operating in a year-round ‘peak’ season. Executives from the largest logistics companies and global retailers are turning to AI and robotics to solve some of their most challenging tasks throughout the supply chain.