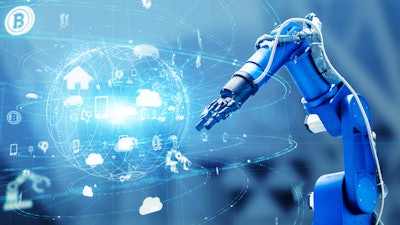
In the peak of a global pandemic, an e-commerce boom and a national labor crisis, warehouses and their workforces have been hit hard. The pandemic has led to one in three employees being unwilling to do work that requires them to be onsite full-time. On top of that, warehouse managers are struggling to keep people who are tired of walking 5-10 miles a day and suffering from health issues like degenerative musculoskeletal injuries.
It’s obvious that changes need to be made and thankfully, the industry is moving in the right direction. Warehouses of every type - manufacturing, storage, fulfillment - are on a path toward automation. And, for those who aren't, the question is not “if” but “when?” Eventually, the goal is to have the ability to automate all tasks remotely in an operation often called “lights out warehouses.” In this model, robots perform all of the rote, repetitive tasks while humans can oversee these tasks by providing more complex and problem-solving skill sets.
The path to get to these dark warehouses looks different for almost every business. They’ll move at different speeds, and some may leap ahead.
Let’s start at the beginning of the automation path and look at the primary phases a fulfillment warehouse will go through as they begin the process.
Unaided warehouse. Here there is no automation. All work is done manually and at its most basic level using pencil and paper. There is likely a limited warehouse management system (WMS) in place to manage inventory, but all material handling is done by people without aid. Employees are required to spend the majority of their shifts walking great distances and pushing heavy carts to pick up stock as part of the order fulfillment process. Conventional industry wisdom says that 80% of warehouses are still operating in this mode without any automation to help them realize efficiencies.
Aided warehouse. This is where you still have the same staff performing the same material handling tasks as in the unaided phase, but are benefitting from some intelligent guidance. They are directed on the paths they take and the sequencing of tasks by software that calculates more efficient movements. They are aided with specific directions on where to go and what to pick or place.
The software calculates the directions, and employees are guided by pick-to-light, pick-to-voice or pick-to-color tools. The efficiencies they realize come from inventory being assigned to locations strategically, and the people are not wasting as much time navigating paths through the warehouse. However, employees are still required to do a significant amount of walking.
Augmented warehouse. The number of people needed in the augmented warehouse can be reduced. The increased efficiency added in the aided warehouse is now boosted by the use of robots to carry out some fulfillment tasks. This is where autonomous mobile robots (AMRs) get introduced that can automate the rolling of order carts across a facility.
The employees still need to follow a path throughout the warehouse to pick or place goods, but they have a robot guiding them and carrying the goods. This creates path planning efficiencies and relieves some of the physical burden placed on people who no longer have to pull heavy order carts around.
Walk-less warehouse. Here, robots can take on a lot more of the remote tasks, including fully automated retrieval and putaway of goods. Employees are able to be more productive because they can focus on sorting and packing out products the robots retrieve. People no longer spend hours of their day walking through the aisles, an activity that usually takes up 50% of their shifts in unaided, aided or augmented warehouses.
Robots bring a bulk quantity of SKUs and then direct people to select the number of items needed for an order. People continue to do fine manipulation of the goods, which is hard for robots to do. This relieves a lot of physical burden from the employees, and it also boosts accuracy rates. The opportunity for human error is decreased when robots are responsible for goods retrieval and putaway.
Touchless warehouse. Automation systems are integrated to extend across operations in a touchless warehouse. You may have AMRs retrieving bulk goods to take to a robotic arm that performs fine manipulation and then places a product on a conveyor belt to go to the end of the line. This eliminates the need for people walking or touching products in the picking and putaway process.
It also eliminates people having to walk and work amid the automation equipment. There’s merely a hand-off to the final pack out. People can do jobs that require more decision-making vs repetitive, physical tasks, and robots are doing the rote, physical tasks with machine precision and eliminating mistakes made from human error.
Self-sufficient or “lights out.” This is a distant vision, but the “lights out” warehouse encapsulates the ultimate level of warehouse automation. Multiple automation systems would be integrated to work as one and create a continuous flow of goods across the warehouse. From inbound and reverse logistics to outbound orders and all of the points in between, machines would precisely execute every movement. Automated systems would work non-stop - no more needs for shifts, training or labor allocation and management.
Self-sufficient warehouses eliminate the need for onsite operators. For example, people who used to drive forklifts could control them remotely from the comfort of their homes. They’d have full mobile access and visibility, so they could monitor and take actions when needed.
Most tasks would be executed autonomously, and these systems would self-correct and self-heal. When an issue arises, the software and the machines that run on them would be able to identify it and implement a remedy without human direction. The systems would be designed with enough intelligence to have data sets that can be referenced to assess and solve problems.
These warehouses would change the role of managers, too. They’d no longer be consumed with personnel issues - hiring, training, managing temps, job assignments, eliminating bottlenecks and fixing problems. Managers would simply oversee operations, and that can be done from anywhere because they don’t have to be in the facility. Ideally, they could be on a beach or spending time with family, as long as they have internet access.
So, the future is bright on the path to warehouse automation. The innovation seen in the space the last few years has given businesses many options to choose from to create their plan. This level of flexibility allows everyone to move at their own pace and find the right technology to support their existing employees and business growth.